Ammoniak ist bei der Herstellung von Düngemitteln von entscheidender Bedeutung und eine der größten synthetischen Chemikalien, die weltweit hergestellt werden. Dieser Artikel untersucht die Entwicklung der Ammoniakproduktion und beschreibt die aktuellen Fertigungstechnologien.
Die meisten Menschen assoziieren den stechenden Geruch von Ammoniak (NH3) mit Reinigern oder Riechsalzen. Die Verwendung von Ammoniak in diesen beiden Produkten macht jedoch nur einen kleinen Teil der gesamten globalen Ammoniakproduktion aus, die 2014 rund 176 Millionen Tonnen betrug (1)., Um zu schätzen, wo Industrie und Technologie heute sind, werfen wir zunächst einen Blick darauf, wie wir hierher gekommen sind.
Ammoniak ist seit mehr als 200 Jahren bekannt. Joseph Priestley, ein englischer Chemiker, isolierte erstmals 1774 gasförmiges Ammoniak. Seine Zusammensetzung wurde 1785 vom französischen Chemiker Claude Louis Berthollet festgestellt., Im Jahr 1898 stellten Adolph Frank und Nikodem Caro fest, dass N2 durch Calciumcarbid unter Bildung von Calciumcyanamid fixiert werden konnte, das dann mit Wasser zu Ammoniak hydrolysiert werden konnte (2):
CaO + 3C ↔ CaC2 + CO
CaC2 + N2 ↔ CaCN2 + C
CaCN2 + 3H2O ↔ CaCO3 + 2NH3
Die Produktion signifikanter Mengen Ammoniak unter Verwendung des Cyanamidprozesses erfolgte erst nach das frühe 20.Jahrhundert. Da dieser Prozess große Energiemengen erforderte, konzentrierten sich die Wissenschaftler auf die Reduzierung des Energiebedarfs.,
Der deutsche Chemiker Fritz Haber führte einige der wichtigsten Arbeiten in der Entwicklung der modernen Ammoniakindustrie durch. Arbeiten mit einem Studenten an der Univ. natürlich synthetisierte er Ammoniak im Labor aus N2 und H2.
Inzwischen ist Walther Nernst, Professor für Physikalische Chemie an der Univ. von Berlin entwickelte ein Verfahren zur Herstellung von Ammoniak durch Passieren einer Mischung aus N2 und H2 über einen Eisenkatalysator bei 1.000°C und 75 barg Druck. Er konnte bei diesem Druck größere Mengen Ammoniak produzieren als frühere Experimente von Haber und anderen bei Atmosphärendruck., Nernst kam jedoch zu dem Schluss, dass das Verfahren nicht durchführbar war, da es (damals) schwierig oder fast unmöglich war, große Geräte herzustellen, die mit diesem Druck arbeiten konnten.
Dennoch verfolgten sowohl Haber als auch Nernst den Hochdruckweg, um Ammoniak über einen Katalysator zu erzeugen. Haber entwickelte schließlich ein Verfahren zur Herstellung kommerzieller Ammoniakmengen und konnte 1906 in einem mit einem Osmiumkatalysator beladenen Reaktor eine Ammoniakkonzentration von 6% erreichen., Dies wird allgemein als der Wendepunkt in der Entwicklung eines praktischen Prozesses zur Herstellung von Ammoniak in kommerziellen Mengen anerkannt.
Haber erkannte, dass die Menge an Ammoniak, die in einem einzigen Durchgang durch einen Konverter gebildet wurde, viel zu niedrig war, um von kommerziellem Interesse zu sein. Um mehr Ammoniak aus dem Make-up-Gas zu produzieren, schlug er ein Recycling-System vor und erhielt ein Patent für das Konzept. Habers neue Idee veränderte die Wahrnehmung der Verfahrenstechnik als statisch zugunsten eines dynamischeren Ansatzes., Neben dem chemischen Reaktionsgleichgewicht erkannte Haber, dass die Reaktionsgeschwindigkeit ein bestimmender Faktor war. Statt einfacher Ausbeute in einem einmaligen Prozess konzentrierte er sich auf Raum-Zeit-Ausbeute in einem System mit Recycling.
BASF erwarb die Patente von Haber und begann mit der Entwicklung eines kommerziellen Verfahrens. Nach dem Testen von mehr als 2.500 verschiedenen Katalysatoren entwickelten Carl Bosch, Alvin Mittasch und andere BASF-Chemiker 1910 einen Eisen-Katalysator zur Herstellung von Ammoniak., Die Entwicklung von Geräten, die den erforderlichen hohen Temperaturen und Drücken standhalten konnten, war eine noch schwierigere Aufgabe. Ein früher Milchstahlreaktor dauerte nur 80 Stunden vor dem Ausfall aufgrund der Dekarbonisierung. Das Auskleiden von Baustahlreaktoren mit weichem Eisen (das nicht anfällig für Dekarbonisierung war) und das Hinzufügen von Rillen zwischen den beiden Auskleidungen zur Freisetzung von Wasserstoff, der durch die weiche Eisenauskleidung diffundiert war, löste dieses Problem., Weitere große Herausforderungen waren die Entwicklung eines Wärmetauschers, um das Einlassgas auf Reaktionstemperaturen zu bringen und das Austrittsgas zu kühlen, und die Entwicklung eines Verfahrens, um den Katalysator auf Reaktionstemperatur zu bringen.
Die erste kommerzielle Ammoniakanlage nach dem Haber-Bosch-Verfahren wurde von der BASF in Oppau gebaut. Die Anlage ging am Sept. in Betrieb. 9, 1913, mit einer Produktionskapazität von 30 m. t. / Tag.
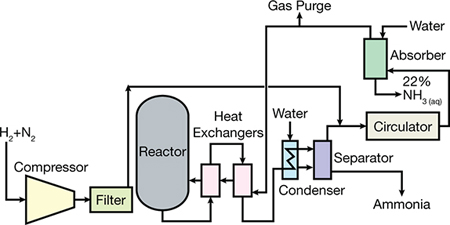
▲Abbildung 1. Dies ist ein vereinfachtes Fließblatt der ersten kommerziellen Ammoniakanlage von BASF.,
Abbildung 1 ist ein Fließblatt der ersten kommerziellen Ammoniakanlage. Der Reaktor enthielt zusätzlich zu den im Schaltplan gezeigten einen internen Wärmetauscher.
Globale Produktionsraten
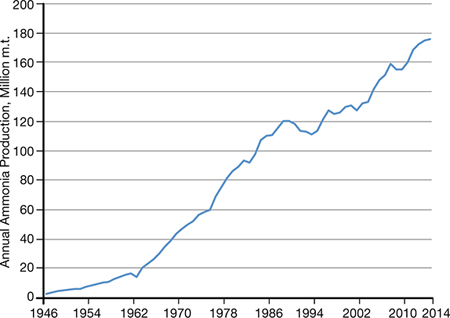
▲Abbildung 2. Die weltweite Ammoniakproduktion ist von 1946 bis 2014 stetig gestiegen.
Die Ammoniakproduktion hat sich zu einer der wichtigsten Industrien der Welt entwickelt. Ohne den Ernteertrag, der durch Düngemittel und Chemikalien auf Ammoniakbasis erzielt wird, würde die Weltbevölkerung mindestens zwei bis drei Milliarden Menschen weniger haben als heute (3)., Die Ammoniakproduktion hat seit 1946 stetig zugenommen (Abbildung 2), und es wird geschätzt, dass die jährliche Ammoniakproduktion mehr als 100 Milliarden US-Dollar wert ist, wobei einige Anlagen mehr als 3,000 m produzieren.t./Tag NH3.
Anlässlich des 75-jährigen Gründungsjubiläums von AIChE nannte 1983 eine Gruppe angesehener Chemieingenieure das, was sie für die zehn größten Chemieingenieurleistungen der Welt hielten (4)., Das Zitat umfasste Kunststücke wie Wunderdrogen, synthetische Fasern und Atomenergie und beinhaltete auch den Durchbruch, der die Produktion großer Mengen Ammoniak in kompakten Anlagen mit einer Einheit ermöglichte.
In den vergangenen Jahrzehnten ist es Chemieingenieuren gelungen, Prozesse zu schaffen, die große Mengen Ammoniak zu relativ geringen Kosten herstellen. Erst vor 80 Jahren betrug die jährliche Gesamtproduktion von synthetisiertem Ammoniak etwas mehr als 300.000 m. t. Dank Durchbrüchen in der Chemieindustrie kann eine moderne Ammoniakanlage mehr als 750.000 m. t produzieren. / Jahr.,
Ungefähr 88% des jährlich hergestellten Ammoniaks werden bei der Herstellung von Düngemitteln verbraucht. Der größte Teil des Restes geht in die Produktion von Formaldehyd. China produzierte 2014 etwa 32,6% der weltweiten Produktion, während Russland, Indien und die USA 8,1%, 7,6% bzw. Während der größte Teil der weltweiten Ammoniakproduktion auf der Dampfreformierung von Erdgas basiert, werden erhebliche Mengen durch Kohlevergasung produziert; Die meisten Vergasungsanlagen befinden sich in China.,
Moderne Produktionsprozesse
Der enorme Anstieg des Ammoniakbedarfs von 1950 bis 1980 erforderte größere, energieeffizientere Anlagen. In diesen Jahrzehnten änderte sich auch die Designphilosophie. Bis zu diesem Zeitpunkt galt eine Ammoniakanlage als Zusammenbau von nicht verwandten Einheiten wie Gasaufbereitung, Gasreinigung, Gaskompression und Ammoniaksynthese. Neue Innovationen und ein integraler Entwurf binden Prozesseinheiten auf effektivste und effizienteste Weise zusammen.
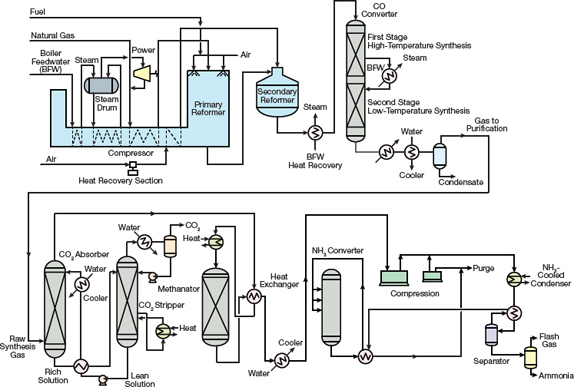
▲Abbildung 3., KBR entwarf eine der ersten Ammoniakanlagen mit großer Kapazität mit einem Zug.
Mitte der 1960er Jahre wurde die American Oil Co. installierte eine von M. W. Kellogg (MWK) entwickelte Ammoniakanlage mit einem einzigen Konverter in Texas City, TX, mit einer Kapazität von 544 m. t./Tag. Das Ein-Zug-Designkonzept (Abbildung 3) war so revolutionär, dass es 1967 den Kirkpatrick Chemical Engineering Achievement Award erhielt.,
Die Anlage verwendete einen Zentrifugalkompressor mit vier Gehäusen, um das Syngas auf einen Druck von 152 bar zu komprimieren, und in einem Kolbenkompressor trat eine endgültige Kompression auf einen Betriebsdruck von 324 bar auf. Zentrifugalkompressoren für den Synthesekreislauf und Kältedienstleistungen wurden ebenfalls implementiert, was zu erheblichen Kosteneinsparungen führte.,
Die Hauptunterschiede zwischen dem MWK-Verfahren und den in früheren Ammoniakanlagen verwendeten Prozessen waren:
- Verwendung eines Kreiselkompressors als Teil der Synthesegaskompression
- Maximierung der Rückgewinnung von Abwärme aus dem Prozess
- Erzeugung von Dampf aus der Abwärme für den Einsatz in Dampfturbinentreibern
- Verwendung des Kühlkompressors für heruntergekühlte und atmosphärische Kühlung.
Ein integriertes Schema, das Energieverbrauch, Energieerzeugung, Gerätegröße und Katalysatorvolumen ausbalancierte, wurde in der gesamten Anlage integriert.,
Die meisten Anlagen, die zwischen 1963 und 1993 gebaut wurden, hatten große Einzelzugkonstruktionen mit Synthesegaserzeugung bei 25-35 bar und Ammoniaksynthese bei 150-200 bar. Eine weitere Variante von Braun (jetzt KBR) bot leichte Änderungen am Grunddesign. Die Braun Purifier Process Plants verwendeten einen Primär – oder Rohrreformer mit niedriger Austrittstemperatur und hoher Methanleckage, um die Größe und die Kosten des Reformers zu reduzieren. Dem Sekundärreformer wurde überschüssige Luft zugesetzt, um den Methangehalt des Primärreformer-Austrittsstroms auf 1-2% zu reduzieren., Überschüssiger Stickstoff und andere Verunreinigungen wurden stromabwärts des Methanators entfernt. Da das Synthesegas im Wesentlichen frei von Verunreinigungen war, wurden zwei Axialstrom-Ammoniakwandler verwendet, um eine hohe Ammoniakumwandlung zu erreichen.
Einige kürzlich gebaute Anlagen verfügen über ein Synthesegaserzeugungssystem mit nur einem Reformer (kein Sekundärreformer), ein Druckschwungadsorptionssystem (PSA) zur H2-Rückgewinnung und eine Luftzerlegungsanlage als Quelle von N2., Verbesserungen im Konverterdesign wie radiale und horizontale Katalysatorbetten, interne Wärmetauscher und Synthesegasbehandlung trugen dazu bei, die Ammoniakkonzentrationen, die aus dem Synthesewandler austreten, von etwa 12% auf 19-21% zu erhöhen. Eine höhere Umwandlung pro Durchgang, zusammen mit effizienteren Turbinen und Kompressoren, reduzierte den Energieverbrauch weiter. Effizientere CO2-Entfernungslösungen wie Kaliumcarbonat und Methyldiethanolamin (MDEA) haben zu einer verbesserten Energieeffizienz beigetragen. Die meisten modernen Anlagen können Ammoniak mit einem Energieverbrauch von 28 GJ/m produzieren.t.,
Zusätzlich zu den konstruktiven, mechanischen und metallurgischen Verbesserungen, die während dieser Zeit vorgenommen wurden, wurde der Betriebsdruck der Syntheseschleife signifikant reduziert. Als in den 1960er Jahren das erste Einzelzugwerk gebaut wurde, enthielt es eine Hochdrucksyntheseschleife. 1962 erhielt MWK eine Anfrage von Imperial Chemical Industries (ICI) nach einem Vorschlag zum Bau einer 544-m. t./Tag-Anlage am Standort Severnside. MWK schlug eine 152-bar-Syntheseschleife anstelle einer 324-Bar-Schleife vor.,
Da die Entwicklung kinetischer Daten für die Ammoniakreaktion bei 152 bar länger dauern würde, als MWK auf die ICI-Anfrage antworten musste, kontaktierten sie Haldor Topsøe, um ihre Pläne zu unterstützen. Topsøe hatte Daten über den gesamten für MWK interessanten Druckbereich. Darüber hinaus verfügten sie über ein Computerprogramm zur Berechnung der Katalysatormenge, die bei dem niedrigeren Betriebsdruck benötigt wurde. Obwohl ICI Bechtel für die Planung der Anlage auswählte, konnte MWK ein Flowsheet für einen 544-m. t entwickeln.,/ tag Design mit Zentrifugalkompressoren und einer Niederdrucksyntheseschleife, die einige Leute als das wichtigste Ereignis bei der Entwicklung der Ammoniakanlage mit einem Zug betrachten.
Bei 152 bar wurde etwa doppelt so viel Katalysator benötigt wie bei 324 bar, ein Anstieg, der wirtschaftlich machbar schien. Obwohl der Konverter das doppelte Volumen benötigen würde, würde der niedrigere Betriebsdruck die erforderliche Dicke der Druckschale verringern. Infolgedessen blieb das für den Konverter plus Katalysator erforderliche Metallgewicht ungefähr gleich., Die Niederdrucksyntheseschleife ermöglichte auch die Verwendung von Zentrifugalkompressoren anstelle von Kolbenkompressoren. Eine weitere Verbesserung war die Wärmerückgewinnung zur Erzeugung von Hochdruckdampf für Dampfturbinenantriebe.Jahrhundert
In den ersten Jahren des 21st Jahrhunderts wurden viele Verbesserungen in der Ammoniakanlagentechnologie vorgenommen, die es bestehenden Anlagen ermöglichen, die Produktionsraten zu erhöhen und neue Anlagen mit größeren und größeren Kapazitäten zu bauen. Der Wettbewerb zwischen Technologieanbietern ist ziemlich hart., Drei Technologie-Lizenzgeber — KBR (Kellogg Brown und Root), Haldor Topsøe und ThyssenKrupp Industrial Solutions (TKIS) – dominieren derzeit den Markt. Ammoniak Casale, das ein axial-radiales Katalysatorbett-Design bietet, ist Marktführer bei der Umrüstung bestehender Anlagen.
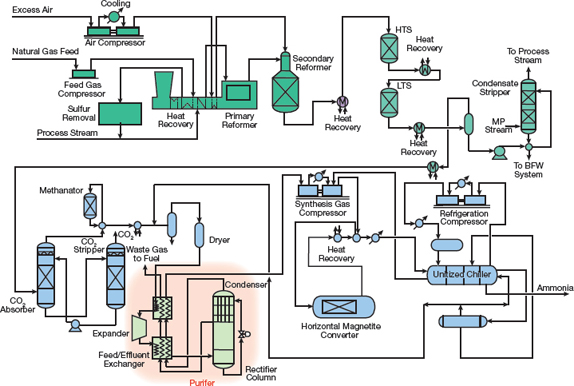
▲Abbildung 4. Moderne Ammoniakanlagen, die von KBR entworfen wurden, verwenden sein proprietäres Purifier-Design.,
Die meisten Ammoniakanlagen, die kürzlich von KBR entworfen wurden, nutzen das Reinigungsverfahren (Abbildung 4), das eine Reform mit geringem Schweregrad im Primärreformer, einen flüssigen N2-Waschreiniger nach dem Methanator kombiniert, um Verunreinigungen zu entfernen und das H2:N2-Verhältnis anzupassen, ein proprietäres Abwärmekesseldesign, ein Einheitskühler und ein horizontaler Ammoniaksynthesekonverter.
Je nach Konfiguration der Anlage kann der Energieverbrauch bis zu 28 GJ / m betragen. t. Da der Sekundärreformer überschüssige Luft verwendet, kann der Primärreformer kleiner sein als bei herkömmlichen Konstruktionen., Der kryogene Reiniger (in Abbildung 4 in hellgrün mit hellorangem Hintergrund dargestellt), der aus einem Expander, einem Kondensator, einem Zufuhr – /Abwassertauscher und einer Gleichrichtersäule besteht, entfernt Verunreinigungen wie CO, CH4 und Argon aus dem Synthesegas, während das H2:N2-Verhältnis des Ammoniakgases in der Ammoniakschleife auf das optimale Niveau eingestellt wird. Die Ammoniakkonzentration, die aus dem horizontalen Niederdruck-Abfall-Wandler austritt, beträgt 20-21%, was den Energiebedarf für den Recyclingkompressor reduziert., KBR bietet auch eine Niederdruck-Ammoniakschleife an, die eine Kombination aus Magnetitkatalysator und seinem proprietären Rutheniumkatalysator verwendet.
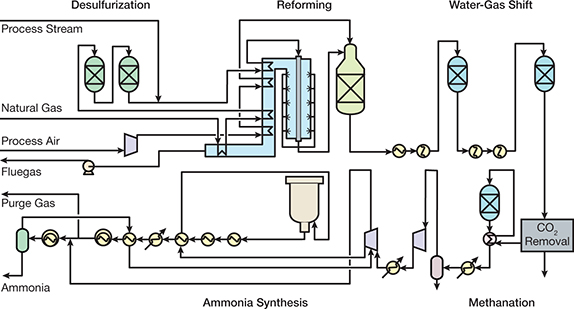
▲Abbildung 5. Haldor Topsøe bietet ein Ammoniak-Anlagendesign mit einem proprietären seitenbefeuerten Reformer, bei dem Strahlungsbrenner Wärme für die Reformierungsreaktion liefern.
Der Syngas-Erzeugungsabschnitt (oder Frontend) einer von Haldor Topsøe entworfenen Anlage (Abbildung 5) ist mit Ausnahme seines proprietären seitenbefeuerten Reformers, der Strahlungsbrenner verwendet, um Wärme für die Reformierungsreaktion zu liefern, ziemlich traditionell., Haldor Topsøe bietet auch einen proprietären Eisensynthesekatalysator, Radialstromwandler, bestehend aus einem, zwei oder drei Betten, und einen proprietären Bajonettrohr-Abwärmekessel. Neuere Entwicklungen umfassen die Konverterdesigns S-300 und S-350. Der S-300-Konverter ist eine Drei-Bett-Radialstromkonfiguration mit internen Wärmetauschern, während das S-350-Design einen S-300-Konverter mit einem S-50-Einzelbettdesign mit Abwärmerückgewinnung zwischen Konvertern kombiniert, um die Ammoniakumwandlung zu maximieren.
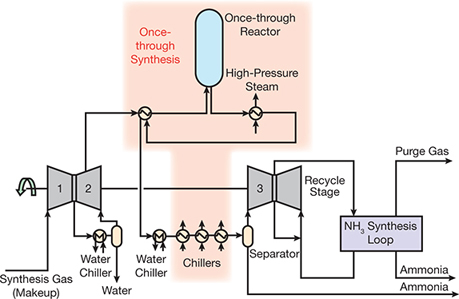
▲Abbildung 6., ThyssenKrupp ist dual-pressure synthesis loop-design verfügt über eine einmal-durch-Reaktor zwischen Synthesegas-Kompressoren.
ThyssenKrupp bietet eine konventionelle Anlage (Abbildung 6) mit einzigartigem Sekundärreformer-Design, einen eigenen Abwärmekessel, Radialstromwandler und eine Zweidruck-Ammoniaksyntheseschleife an. Heute kann mit dem TKIS Dual-Pressure-Verfahren eine Produktionsrate von 3.300 m. t. / Tag erreicht werden.
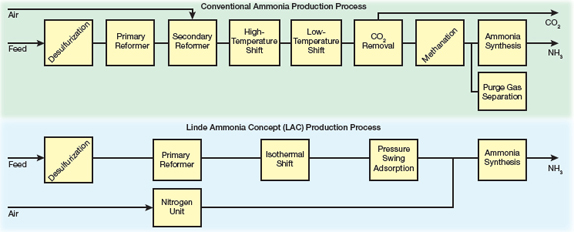
▲Abbildung 7., Das Linde Ammoniak Concept (LAC) verfügt über eine Druck-Swing-Adsorptionseinheit für die hochreine Wasserstoffproduktion und eine Luftzerlegungseinheit für die hochreine Stickstoffproduktion.
Das Linde Ammoniak Concept (LAC) ist ein etabliertes Technologie-Prozess-System mit über 25 Jahren Betriebserfahrung in Anlagen mit Kapazitäten von 200 m. t./Tag bis über 1.750 m. t./Tag., Das LAC-Prozessschema (Abbildung 7) ersetzt das kostspielige und komplexe Frontend einer konventionellen Ammoniakanlage durch zwei bewährte, zuverlässige Prozesseinheiten:
- Herstellung von ultrahochreinem Wasserstoff aus einem Dampf-Methan-Reformer mit PSA-Reinigung
- Herstellung von ultrahochreinem Stickstoff durch eine kryogene Stickstofferzeugungseinheit, auch als Luftzerlegungseinheit (ASU) bekannt.
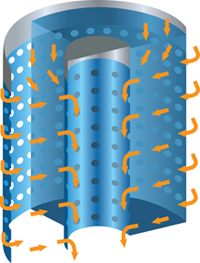
▲Abbildung 8., Das Verfahren von Ammoniak Casale verwendet ein Katalysatorbett, das die axial-radiale Technologie nutzt, die einen geringeren Druckabfall und einen höheren Wirkungsgrad als Standardkatalysatorbetten aufweist.
Ammoniak Casales Anlagenentwurf hat eine Produktionsrate von 2.000 m. t. / Tag. Eines der Hauptmerkmale dieser Konstruktion ist die Axial-Radial-Technologie im Katalysatorbett (Abbildung 8). In einem axial-radialen Katalysatorbett passiert der größte Teil des Synthesegases das Katalysatorbett in radialer Richtung, wodurch ein sehr niedriger Druckabfall entsteht., Der Rest des Gases geht in axialer Richtung durch eine obere Katalysatorschicht nach unten, wodurch eine obere Abdeckung auf dem Katalysatorbett entfällt. Die axial-radiale Katalysatorbetttechnologie von Casale wird sowohl in Hochtemperatur-als auch in Niedertemperatur-Schaltwandlern sowie im Syntheseumwandler eingesetzt.
Andere Technologien
Einige Technologieanbieter haben gasbeheizte Reformer (GHRs) zur Herstellung von Ammoniak in Kleinkraftwerken oder zur Kapazitätserhöhung angeboten., Im Gegensatz zu konventionell gestalteten Anlagen, die einen in Reihe betriebenen Primärreformer und Sekundärreformer verwenden, verwenden Anlagen mit GHRs das heiße Prozessgas des Sekundärreformers, um dem Primärreformer Wärme zuzuführen. Dies reduziert die Größe des Primärreformers und eliminiert CO2-Emissionen aus dem Primärreformerstapel, wodurch der Prozess umweltfreundlicher wird.,
Obwohl einige Ammoniakproduzenten sich für die verteilte Produktion von Ammoniak in kleinen Ammoniakanlagen einsetzen, ziehen es die meisten Unternehmen vor, große Anlagen in der Nähe billiger Rohstoffquellen zu bauen und das Produkt per Schiff, Schiene oder Pipeline zu den Verbrauchern zu transportieren.
Ammoniak aus Kohle
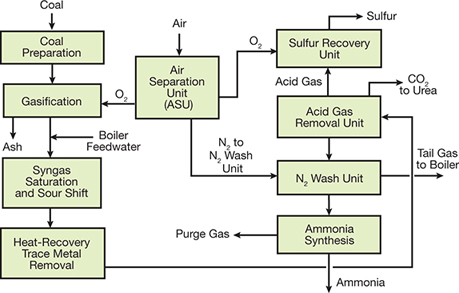
▲Abbildung 9. China produziert den größten Teil seines Ammoniaks aus Kohle.
China produziert mehr Ammoniak als jedes andere Land und produziert den größten Teil seines Ammoniaks aus Kohle (Abbildung 9).,
Die grundlegenden Verarbeitungseinheiten in einer Ammoniakanlage auf Kohlebasis sind die ASU für die Trennung von O2 und N2 von Luft, der Vergaser, die Sauergasverschiebungseinheit (SGS), die Säuregasentfernungseinheit (AGRU) und die Ammoniaksyntheseeinheit. Sauerstoff aus der ASU wird dem Vergaser zugeführt, um Kohle in Synthesegas (H2, CO, CO2) und CH4 umzuwandeln. Es gibt viele Vergaser-Designs, aber die meisten modernen Vergaser basieren auf Wirbelschichtbetten, die über Atmosphärendruck arbeiten und die Fähigkeit haben, verschiedene Kohlevorräte zu nutzen. Je nach Ausführung können CO-Werte von 30-60 Volumenprozent hergestellt werden.,
Nach der Vergasung werden alle Partikel im Synthesegas entfernt und Dampf in die Gaseinheit gegeben. Das SGS-Verfahren verwendet typischerweise einen Kobalt-und Molybdänkatalysator (CoMo), der speziell für den Betrieb in einer Schwefelumgebung entwickelt wurde.
Nachdem die CO-Konzentration im Synthesegas auf weniger als 1 vol% reduziert wurde, wird das Syngas einem AGRU zugeführt, wo eine gekühlte Methanolwäschelösung (z. B. Rectisol) CO2 und Schwefel aus dem Synthesegas entfernt. Der CO2-Überkopf wird entweder entlüftet oder einer Harnstoffanlage zugeführt. Der Schwefelauslassstrom wird einer Schwefelrückgewinnungseinheit (SRU) zugeführt.,
Syngas, das durch die AGRU geleitet wird, wird typischerweise durch eine von zwei Methoden gereinigt:
- eine Stickstoffwascheinheit, um restliches CO und CH4 aus den Syngas zu entfernen, bevor es der Syntheseschleife zugeführt wird
- ein PSA-System zur Entfernung von CO und CH4.
Schlussgedanken
In den letzten 60 Jahren hat sich die Ammoniak-Prozesstechnologie drastisch verbessert. Anlagenlayouts entwickelten sich von Multi-Train-Designs, oft mit unterschiedlicher Anzahl von Zügen im Frontend und Syntheseschleife, zu Single-Train-Designs., Synthesegasvorbereitung im vorderen Ende der Anlage stieg von Atmosphärendruck auf 30-50 barg Druck. Die Kapazitäten stiegen von 100 m. t. / Tag auf bis zu 3.300 m. t. / Tag in einem einzigen Zug.
Auch die Energieeffizienz hat sich verbessert-vom Verbrauch deutlich über 60 GJ/m. t. Ammoniak in Koksanlagen auf 40-50 GJ/m. t. in den ersten Erdgasanlagen auf 30-40 GJ/m. t. in den ersten Einzelzuganlagen. Moderne Anlagen haben die Wärmerückgewinnung durch Dampferzeugung bei Drücken von bis zu 125 barg sowohl im Bereich der Syngasvorbereitung als auch im Synthesekreislauf hinzugefügt.,
In Bezug auf die Prozessausrüstung hat es eine Verlagerung von Kolbenkompressoren zu Zentrifugalkompressoren gegeben. Ein interner Wärmetauscher wurde im Synthesewandler implementiert, um die Umwandlung von H2 und N2 in NH3 zu erhöhen. Konstrukteure haben die Wasserstoffrückgewinnung aus Spülgas (in Einheiten wie PSA-Systemen) genutzt, um die Produktion zu steigern oder den Energieverbrauch der Anlage zu senken. Designer haben auch Heißgasentschwefelungssysteme implementiert. Es gab signifikante Verbesserungen bei den Katalysatoren, die bei der Reformierung, Schichtumwandlung, Methanisierung und Ammoniaksynthese verwendet wurden.,
Zur Verbesserung der Prozesssteuerung und-sicherheit sind Distributed Control Systems (DCSs) für fortschrittliche Prozesssteuerung sowie Safety-Instrumented Systems (SISs) heute Standard in Ammoniakanlagen. Bevor ein Prozess online geht, werden HAZOP-Studien (Hazard and Operability) und Layer of Protection Analyses (LOPAs) durchgeführt. Fortschritte bei Trainingssimulatoren und Schulungspraktiken stellen sicher, dass Bediener und Ingenieure ihre Aufgaben sicher und effektiv erfüllen können.,
Dies sind nur einige der tausenden von Verbesserungen in Technologie und Sicherheit, die implementiert wurden, um die Ammoniakindustrie zu einer der produktivsten und sichersten Branchen der Welt zu machen.
Acknowledgments
Die Autoren erkennen die Unterstützung von KBR, ThyssenKrupp Industrial Solutions, Haldor Topsøe, Linde und Casale für die Bereitstellung technischer Literatur zu ihren jeweiligen Prozesstechnologien an.