ammoniak er kritisk i fremstillingen af gødning, og er en af de største volumen syntetiske kemikalier produceret i verden. Denne artikel udforsker udviklingen af ammoniak produktion og beskriver de nuværende produktionsteknologier.
de fleste mennesker forbinder den skarpe lugt af ammoniak (NH3) med rengøringsmidler eller ildelugtende salte. Anvendelsen af ammoniak i disse to produkter udgør dog kun en lille brøkdel af den samlede globale ammoniakproduktion, som var omkring 176 millioner tons i 2014 (1)., For at værdsætte, hvor branchen og teknologien er i dag, lad os først se på, hvordan vi kom her.
ammoniak har været kendt i mere end 200 år. Joseph Priestley, en engelsk kemiker, isolerede først gasformig ammoniak i 1774. Dens sammensætning blev konstateret af den franske kemiker Claude Louis Berthollet i 1785., I 1898, Adolph Frank og Nikodem Caro fandt, at N2 kan fastsættes ved calciumcarbid til at danne calciumcyanamid, som derefter kunne være hydrolyseret med vand og danner ammoniak (2):
CaO + 3C ↔ CaC2 + CO
CaC2 + N2 ↔ CaCN2 + C
CaCN2 + 3H2O ↔ CaCO3 + 2NH3
produktion af betydelige mængder af ammoniak hjælp cyanamid proces ikke forekommer indtil begyndelsen af det 20.århundrede. Fordi denne proces krævede store mængder energi, fokuserede forskerne deres bestræbelser på at reducere energibehovet.,
tysk kemiker frit.Haber udførte noget af det vigtigste arbejde i udviklingen af den moderne ammoniakindustri. Arbejder med en studerende på Univ. af Karlsruhe syntetiserede han ammoniak i laboratoriet fra N2 og H2.i mellemtiden er Meanwhilealther Nernst, professor i fysisk kemi ved Univ. en proces til fremstilling af ammoniak ved at føre en blanding af N2 og H2 over en jernkatalysator ved 1.000 and C og 75 barg tryk. Han var i stand til at producere større mængder af ammoniak ved dette pres end tidligere eksperimenter ved Haber og andre ved atmosfærisk tryk., Nernst konkluderede imidlertid, at processen ikke var mulig, fordi det var vanskeligt eller næsten umuligt (på det tidspunkt) at fremstille stort udstyr, der kunne fungere ved det tryk.
ikke desto mindre forfulgte både Haber og Nernst højtryksruten for at producere ammoniak over en katalysator. Haber udviklede endelig en proces til fremstilling af kommercielle mængder ammoniak, og i 1906 kunne han opnå en 6% ammoniakkoncentration i en reaktor fyldt med en osmiumkatalysator., Dette anerkendes generelt som vendepunktet i udviklingen af en praktisk proces til produktion af ammoniak i kommercielle mængder.Haber indså, at mængden af ammoniak dannet i en enkelt passage gennem en konverter var alt for lav til at være af kommerciel interesse. For at producere mere ammoniak fra makeupgassen foreslog han et genanvendelsessystem og modtog et patent på konceptet. Habers genanvendelsesidee ændrede opfattelsen af procesteknik som statisk til fordel for en mere dynamisk tilgang., Ud over den kemiske reaktionsbalance erkendte Haber, at reaktionshastigheden var en afgørende faktor. I stedet for simpelt udbytte i en engangsproces koncentrerede han sig om rumtidsudbytte i et system med genbrug.
BASF købte Habers patenter og begyndte at udvikle en kommerciel proces. Efter at have testet mere end 2.500 forskellige katalysatorer udviklede Carl Bosch, Alvin Mittasch og andre BASF-kemikere en fremmet jernkatalysator til produktion af ammoniak i 1910., Udvikling af udstyr, der kunne modstå de nødvendige høje temperaturer og tryk, var en endnu vanskeligere opgave. En tidlig mild stålreaktor varede kun 80 timer før fiasko på grund af dekarbonisering. Foring af milde stålreaktorer med blødt jern (som ikke var sårbart over for dekarbonisering) og tilføjelse af riller mellem de to foringer for at frigive brint, der havde diffunderet gennem den bløde jernforing, løste dette problem., Andre store udfordringer omfattede design af en varmeveksler for at bringe indløbsgassen til reaktionstemperaturer og afkøle udgangsgassen og udtænke en metode til at bringe katalysatoren til reaktionstemperatur.
det første kommercielle ammoniakanlæg baseret på Haber-Bosch-processen blev bygget af BASF i Oppau, Tyskland. Anlægget gik i gang på Sept. 9, 1913, med en produktionskapacitet på 30 m. t. / dag.
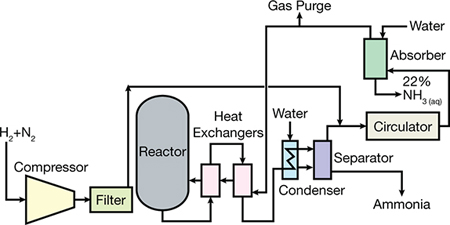
Figure Figur 1. Dette er et forenklet Flo .sheet af BASF ‘ s første kommercielle ammoniakanlæg.,figur 1 er et Flo .ark af det første kommercielle ammoniakanlæg. Reaktoren indeholdt en intern varmeveksler ud over dem, der er vist på skematisk.
globale produktionshastigheder
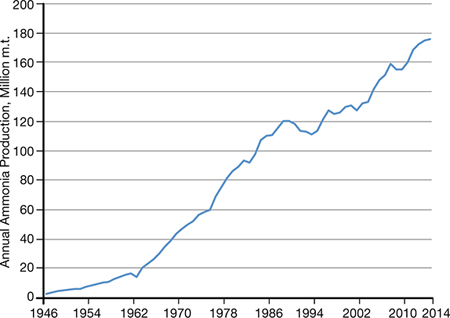
Figure figur 2. Den verdensomspændende ammoniakproduktion er steget støt fra 1946 til 2014.
ammoniakproduktion er blevet en af de vigtigste industrier i verden. Uden afgrødeudbyttet muliggjort af ammoniakbaserede gødninger og kemikalier, ville den globale befolkning være mindst to til tre milliarder mindre end den er i dag (3)., Ammoniak produktionen er steget støt siden 1946 (Figur 2), og det anslås, at den årlige produktion af ammoniak er mere værd end $100 milliarder, med nogle planter, der producerer mere end 3.000 meter.t./dag NH3.
i 1983, i anledning af 75-årsdagen for AIChE ‘ s grundlæggelse, navngav et blåt båndpanel af fremtrædende kemiske ingeniører, hvad de troede var verdens ti største kemitekniske resultater (4)., Citationen omfattede også det gennembrud, der tillod produktion af store mængder ammoniak i kompakte anlæg med en enhed.
inden for de seneste årtier, kemiske ingeniører har formået at skabe processer, der gør enorme mængder af ammoniak til relativt lave omkostninger. Så sent som for 80 år siden var den samlede årlige produktion af syntetiseret ammoniak lidt over 300.000 m.t. takket være kemitekniske gennembrud kan en moderne ammoniakfabrik producere mere end 750.000 m.T./år.,88% ammoniak fremstillet årligt forbruges til fremstilling af gødning. Det meste af resten går ind i produktionen af formaldehyd. Kina producerede omkring 32.6% af den globale produktion i 2014, mens Rusland, Indien og USA producerede henholdsvis 8.1%, 7.6% og 6.4% (1). Mens det meste af den globale produktion af ammoniak er baseret på dampreformering af naturgas, produceres betydelige mængder ved kulforgasning; de fleste forgasningsanlæg er placeret i Kina.,
moderne produktionsprocesser
den enorme stigning i ammoniakefterspørgslen fra 1950 til 1980 krævede større, mere energieffektive anlæg. Disse årtier oplevede også en ændring i designfilosofi. Indtil da, en ammoniak plante blev betragtet som en samling af uafhængige enheder, såsom gas forberedelse, gasrensning, gas kompression, og ammoniak syntese. Nye innovationer og et integreret design bundet procesenheder sammen på de mest effektive og effektive måder.
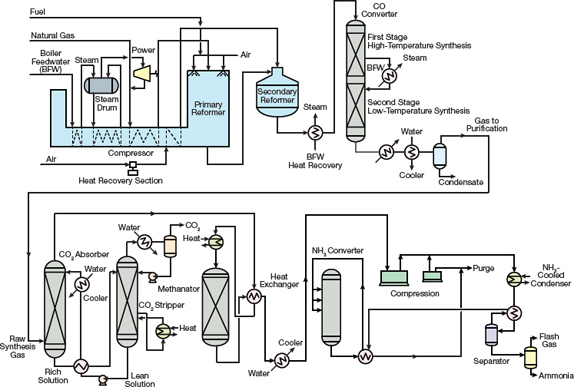
Figure figur 3., KBR designet en af de første single-tog, stor kapacitet ammoniak planter.
i midten af 1960 ‘ erne, American Oil Co. der er installeret et enkelt-converter ammoniak anlæg udviklet af M. W. Kellogg (MWK) i Texas City, TX, med en kapacitet på 544 mio.t./dag. Designkonceptet med et enkelt tog (figur 3) var så revolutionerende, at det modtog Kirkpatrick Chemical Engineering Achievement a .ard i 1967.,
anlægget anvendte en centrifugalkompressor med fire tilfælde til at komprimere syngas til et tryk på 152 bar, og endelig kompression til et driftstryk på 324 bar forekom i en frem-og tilbagegående kompressor. Centrifugalkompressorer til syntesesløjfe og køletjenester blev også implementeret, hvilket gav betydelige omkostningsbesparelser.,
de vigtigste forskelle mellem De MWK proces og de processer, der anvendes i tidligere ammoniak planter inkluderet:
- ved hjælp af en centrifugal kompressoren som en del af syntese gas kompression
- maksimere genvinding af spildvarme fra proces
- til at producere damp fra spildvarme til brug i dampturbine-drivere
- brug af køleanlæg eller kompressor for nedslidte og atmosfæriske køling.
en integreret ordning, der afbalancerede energiforbrug, energiproduktion, udstyr størrelse og katalysator mængder blev indarbejdet i hele anlægget.,
de fleste anlæg bygget mellem 1963 og 1993 havde store enkelt-tog design med syntese gasproduktion på 25-35 bar og ammoniak syntese på 150-200 bar. En anden variation af Braun (nu KBR) tilbød små ændringer af det grundlæggende design. Braun Purifier process plants udnyttede en primær eller rørformet reformator med lav udløbstemperatur og høj metan lækage for at reducere reformatorens størrelse og omkostninger. Overskydende luft blev tilsat til den sekundære reformator for at reducere metanindholdet i den primære reformator e .it stream til 1-2%., Overskydende nitrogen og andre urenheder blev fjernet nedstrøms for methanatoren. Fordi syntesegassen i det væsentlige var fri for urenheder, blev to aksialstrøm ammoniakomformere anvendt til at opnå en høj ammoniakomdannelse.
nogle nybyggede anlæg har et syntesegasgenereringssystem med kun en reformator (ingen sekundær reformator), et tryk-s .ing adsorptionssystem (PSA) til H2-genvinding og et luftseparationsanlæg som kilde til N2., Forbedringer i Konverter design, såsom radiale og vandrette katalysator senge, interne varmevekslere, og syntese gas behandling, bidraget til at øge ammoniak koncentrationer forlader syntesen Konverter fra omkring 12% til 19-21%. En højere konvertering pr pass, sammen med mere effektive turbiner og kompressorer, yderligere reduceret energiforbruget. Mere effektive løsninger til fjernelse af CO2, såsom kaliumcarbonat og methyldiethanolamin (MDEA), har bidraget til forbedret energieffektivitet. De fleste moderne anlæg kan producere ammoniak med et energiforbrug på 28 GJ/m.t.,
ud over de design -, mekaniske og metallurgiske forbedringer, der blev foretaget i løbet af denne tid, blev driftstrykket i syntesesløjfen signifikant reduceret. Da det første single-train-anlæg blev bygget i 1960 ‘ erne, indeholdt det en højtrykssyntesesløjfe. I 1962, MWK modtaget en forespørgsel fra Imperial Chemical Industries (ICI) for et forslag om at bygge en 544-m.t./dag plante på deres Severnside site. M .k foreslog en 152-bar syntesesløjfe i stedet for en 324-bar sløjfe.,
da udviklingen af kinetiske data for ammoniakreaktionen ved 152 bar ville tage længere tid, end M .k skulle svare på ICI-undersøgelsen, kontaktede de Haldor Topsøe for at støtte deres planer. Topsøe havde data, der dækkede hele det trykområde, der var af interesse for m .k. Derudover havde de et computerprogram til beregning af mængden af katalysator, der var påkrævet ved det lavere driftstryk. Selvom ICI valgte Bechtel til at designe anlægget, kunne M .k udvikle et Flo .ark til en 544-m.t.,/ dag design med centrifugalkompressorer og en lavtryks syntese loop, som nogle mennesker anser den vigtigste begivenhed i udviklingen af single-train ammoniak anlæg.
cirka dobbelt så meget katalysator var påkrævet ved 152 bar som ved 324 bar, en stigning, der syntes økonomisk gennemførlig. Selvom konverteren ville have brug for to gange volumen, ville det lavere driftstryk reducere den krævede tykkelse af trykskallen. Som følge heraf forblev vægten af metal, der kræves til konverteren plus katalysatoren, omtrent den samme., Syntesesløjfen med lavere tryk tillod også brugen af centrifugalkompressorer i stedet for frem-og tilbagegående kompressorer. En anden forbedring var at genvinde varme til at generere højtryksdamp til dampturbinedrev.
plantedesign i det 21.århundrede
i løbet af de første par år af det 21. århundrede blev der foretaget mange forbedringer i ammoniakplanteteknologi, der gør det muligt for eksisterende anlæg at øge produktionshastighederne og nye anlæg, der skal bygges med større og større kapacitet. Konkurrencen mellem teknologileverandører er ret hård., Tre teknologicensgivere — KBR (Kellogg bro .n og Root), Haldor Topsøe og ThyssenKrupp Industrial Solutions (TKIS) – dominerer i øjeblikket markedet. Ammoniak Casale, som tilbyder en aksial-radial katalysator seng design, er markedsleder i fornyelser af eksisterende anlæg.
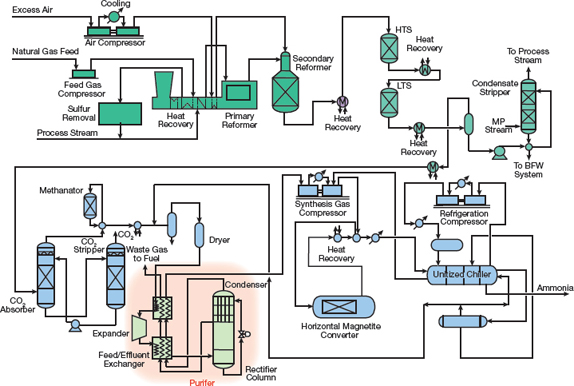
Figure figur 4. Moderne ammoniak planter designet af KBR ansætte sin proprietære Purifier design.,
de Fleste af ammoniak anlæg for nylig designet af KBR udnytte sin Purifier proces (Figur 4), som kombinerer lav sværhedsgrad reform i den primære reformator, en flydende N2 wash renser neden for methanator til at fjerne urenheder og justere H2:N2 ratio, en proprietær affald-heat kedel design, en unitized chiller, og en vandret ammoniak syntese converter.
afhængigt af anlæggets konfiguration kan energiforbruget være så lavt som 28 GJ / m.T. fordi den sekundære reformator bruger overskydende luft, kan den primære reformator være mindre end i konventionelle designs., Den kryogene purifier (vist i Figur 4 i lys grøn med en lys orange baggrund), som består af en expander, kondensator, foder/spildevand varmeveksler, og ensretter kolonne, fjerner urenheder, såsom CO, CH4, og argon fra syntesegas, mens du justerer H2:N2 forholdet makeup gas i ammoniak loop til det optimale niveau. Ammoniakkoncentrationen, der forlader den vandrette konverter med lavt tryk, er 20-21%, hvilket reducerer energibehovet for genanvendelseskompressoren., KBR tilbyder også en lavtryks ammoniaksløjfe, der anvender en kombination af magnetitkatalysator og dens proprietære rutheniumkatalysator.
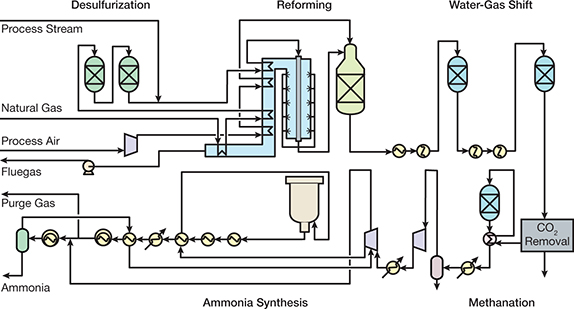
Figure figur 5. Haldor Topsøe tilbyder et ammoniakfabrikdesign, der har en proprietær sidefyret reformator, hvor strålebrændere leverer varme til reformeringsreaktionen.
syngasgenerationssektionen (eller forenden) af et Haldor Topsøe-designet anlæg (figur 5) er ret traditionelt med undtagelse af dets proprietære sidefyrede reformator, der bruger strålende brændere til at levere varme til reformeringsreaktionen., Haldor Topsøe tilbyder også en proprietær jernbaseret syntesekatalysator, radial-Flo.-omformere bestående af en, to eller tre senge og en proprietær bajonetrør-spildvarmekedel. Nyere udviklinger omfatter S-300 og S-350 konverter design. S-300 converter er et tre-sengs-radial-flow-konfiguration med interne varmevekslere, mens S-350 design kombinerer en S-300-konverter med en S-50 enkelt-seng design med affald varmegenvinding mellem omformere til at maksimere ammoniak konvertering.
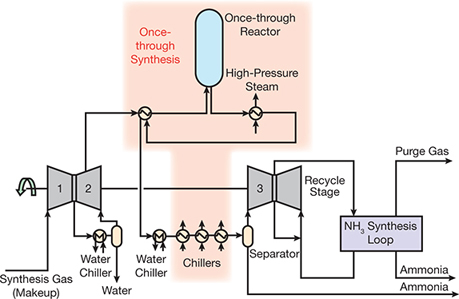
Figure figur 6., Thyssenkrupps dual-pressure syntese loop design har en gang gennem reaktor mellem syngas kompressorer.
ThyssenKrupp tilbyder et konventionelt anlæg (figur 6) med et unikt sekundært reformeringsdesign, en proprietær affaldsvarmekedel, radiale strømningsomformere og en ammoniaksyntesesløjfe med dobbelt tryk. I dag kan der opnås en produktionshastighed på 3.300 m.t./dag ved hjælp af tkis-dual-pressure-processen.
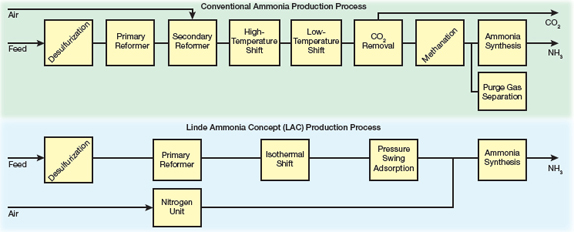
Figure Figur 7., Linde Ammoniak Koncept (LAC) er udstyret med en tryk-swing adsorption enhed for høj renhed brint-produktion og en luft separering af høj renhed kvælstof produktion.
De Linde Ammoniak Koncept (LAC) er en etableret teknologi, proces-ordningen med over 25 års erfaring i anlæg med kapaciteter fra 200 m.t./dag til over 1,750 m.t./dag., LAC proces-ordningen (Figur 7) erstatter dyre og komplekse forreste ende af en konventionel ammoniak anlæg med to gennemprøvede, pålidelige proces-enheder:
- produktion af ultra-høj renhed hydrogen fra en damp-metan reformator med PSA rensning
- produktion af ultra-høj renhed kvælstof ved en kryogene nitrogen generation enhed, også kendt som en luft separering (ASU).
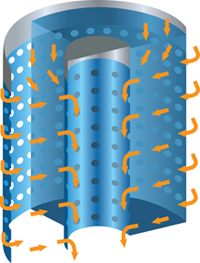
Figure figur 8., Ammoniak Casale proces anvender en katalysator seng, der udnytter aksial-radial teknologi, som har et lavere trykfald og højere effektivitet end standard katalysator senge.
ammoniak Casales plantedesign har en produktionshastighed på 2.000 m.t. / dag. Et af nøglefunktionerne i dette design er aksial-radial teknologi i katalysatorlejet (figur 8). I en aksial-radial katalysatorlejet passerer det meste af syntesegassen gennem katalysatorlejet i en radial retning, hvilket skaber et meget lavt trykfald., Resten af gassen passerer ned gennem et øverste lag af katalysator i en aksial retning, hvilket eliminerer behovet for et topdæksel på katalysatorlejet. Casales aksiale-radiale katalysatorbed-teknologi bruges i både høj temperatur og lav temperatur skiftomformere såvel som i syntesekonverteren.
andre teknologier
nogle teknologileverandører har tilbudt gasopvarmede reformatorer (GHR ‘ er) til produktion af ammoniak i småkapacitetsanlæg eller til kapacitetsforøgelse., I modsætning til konventionelt designede planter, der bruger en primær reformator og sekundær reformator, der opererer i serie, planter med GHRs bruger den varme procesgas fra den sekundære reformator til at levere varme til den primære reformator. Dette reducerer størrelsen af den primære reformator og eliminerer CO2-emissioner fra den primære reformatorstabel, hvilket gør processen mere miljøvenlig.,selvom nogle ammoniakproducenter går ind for distribueret produktion af ammoniak i små ammoniakanlæg, foretrækker de fleste virksomheder at bygge store faciliteter nær billige råvarekilder og transportere produktet med skib, jernbane eller rørledning til forbrugerne.
ammoniak fra kul
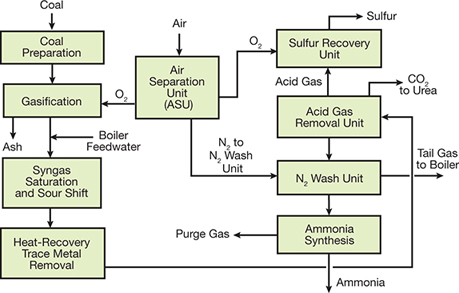
Figure figur 9. Kina producerer det meste af sin ammoniak fra kul.
Kina producerer mere ammoniak end noget andet land, og producerer størstedelen af sin ammoniak fra kul (figur 9).,
de grundlæggende behandlingsenheder i et kulbaseret ammoniakanlæg er ASU til adskillelse af O2 og N2 fra luft, forgaseren, sour gas shift (SGS)-enheden, acid gas removal unit (AGRU) og ammoniaksynteseenheden. Ilt fra ASU føres til forgaseren for at omdanne kul til syntesegas (H2, CO, CO2) og CH4. Der er mange forgasningsdesign, men de fleste moderne forgasere er baseret på fluidiserede senge, der opererer over atmosfærisk tryk og har evnen til at udnytte forskellige kulfoder. Afhængigt af designet kan der produceres CO-niveauer på 30-60 volumenprocent.,
efter forgasning fjernes eventuelle partikler i syntesegassen, og der tilsættes damp til SGS-enheden. SGS proces typisk udnytter en kobolt og molybdæn (CoMo) katalysator specielt designet til drift i et svovl miljø.
efter reduktion af co-koncentrationen i syntesegassen til mindre end 1 vol% føres syngas til en AGRU, hvor en afkølet methanol-skrubningsopløsning (f.eks. Rectisol) fjerner CO2 og svovl fra syntesegassen. CO2-overhead er enten udluftet eller fodret til en urinstofplante. Svovludløbsstrømmen føres til en svovlgenvindingsenhed (SRU).,
Syntesegas, der passerer gennem AGRU er typisk renset ved en af to metoder:
- kvælstof vaske-enheden for at fjerne resterende CO og CH4 fra syntesegas, før det føres til syntese løkke
- en PSA-system for CO og CH4 fjernelse.
lukning af tanker
i løbet af de sidste 60 år er ammoniakprocesteknologien forbedret drastisk. Plant layouts udviklet sig fra multi-tog design, ofte med forskellige antal tog i den forreste ende og syntese loop, til single-tog design., Syntese gas forberedelse i den forreste ende af anlægget steg fra atmosfærisk tryk til 30-50 barg tryk. Kapaciteten steg fra 100 m.t./dag til så meget som 3.300 m.T./dag i et enkelt tog.
energieffektiviteten er også forbedret — fra forbrug langt over 60 GJ/m.t. af ammoniak i koks-baserede anlæg til 40-50 GJ/m.t. i de første naturgasbaserede anlæg til 30-40 GJ / m.t. i de første enkelt-tog anlæg. Moderne planter har tilføjet varmegenvinding ved dampproduktion ved tryk så højt som 125 barg i både syngasforberedelsessektionen og syntesesløjfen.,
med hensyn til procesudstyr har der været et skift fra frem-og tilbagegående kompressorer til centrifugalkompressorer. En intern varmeveksler er blevet implementeret i syntesekonverteren for at øge omdannelsen af H2 og N2 til NH3. Designere har udnyttet brintgenvinding fra rensegas (i enheder som PSA-systemer) for at forbedre produktionen eller reducere plantens energiforbrug. Designere har også implementeret varm fodergasafsvovlingssystemer. Der har været betydelige forbedringer i katalysatorer anvendes i reformering, skift konvertering, methanation, og ammoniak syntese.,
for at forbedre processtyring og sikkerhed er distribuerede kontrolsystemer (DCSs) til avanceret processtyring samt sikkerhedsinstrumenterede systemer (SISs) nu standard i ammoniakanlæg. Før en proces går online, udføres ha .op-undersøgelser og beskyttelsesanalyser (LOPAs). Fremskridt inden for træningssimulatorer og uddannelsespraksis sikrer, at operatører og ingeniører kan udføre deres opgaver sikkert og effektivt.,
Dette er blot nogle få af de tusinder af forbedringer inden for teknologi og sikkerhed, der er implementeret for at gøre ammoniakindustrien til en af de mest produktive og sikre industrier i verden.
anerkendelser
forfatterne anerkender bistand fra KBR, ThyssenKrupp Industrial Solutions, Haldor Topsøe, Linde, og Casale til at levere teknisk litteratur om deres respektive procesteknologier.