ammoniak is van cruciaal belang bij de productie van meststoffen en is een van de grootste synthetische chemische stoffen die in de wereld worden geproduceerd. Dit artikel onderzoekt de evolutie van ammoniakproductie en beschrijft de huidige productietechnologieën.
De meeste mensen associëren de penetrante geur van ammoniak (NH3) met reinigingsmiddelen of reukzouten. Het gebruik van ammoniak in deze twee producten vertegenwoordigt echter slechts een klein deel van de totale wereldwijde ammoniakproductie, die in 2014 ongeveer 176 miljoen ton bedroeg (1)., Om te waarderen waar de industrie en technologie vandaag zijn, laten we eerst een kijkje nemen op hoe we hier zijn gekomen.
ammoniak is al meer dan 200 jaar bekend. Joseph Priestley, een Engelse chemicus, isoleerde voor het eerst gasvormige ammoniak in 1774. De samenstelling werd vastgesteld door de Franse chemicus Claude Louis Berthollet in 1785., In 1898 ontdekten Adolph Frank en Nikodem Caro dat N2 door calciumcarbide kon worden gefixeerd tot calciumcyaanamide, dat vervolgens met water kon worden gehydrolyseerd tot ammoniak (2):
CaO + 3C ↔ CaC2 + CO
CaC2 + N2 ↔ CaCN2 + C
CaCN2 + 3H2O ↔ CaCO3 + 2NH3
de productie van significante hoeveelheden ammoniak met behulp van het cyaanamideproces vond niet plaats totdat de begin 20e eeuw. Omdat dit proces grote hoeveelheden energie vereiste, richtten wetenschappers hun inspanningen op het verminderen van de energiebehoefte.,de Duitse chemicus Fritz Haber heeft enkele van de belangrijkste werkzaamheden verricht in de ontwikkeling van de moderne ammoniakindustrie. Werken met een student van de Univ. van Karlsruhe synthetiseerde hij ammoniak in het laboratorium uit N2 en H2.ondertussen was Walther Nernst, hoogleraar fysische chemie aan de Univ. van Berlijn, ontwikkelde een proces om ammoniak te maken door het passeren van een mengsel van N2 en H2 over een ijzerkatalysator bij 1.000°C en 75 barg druk. Hij was in staat om grotere hoeveelheden ammoniak te produceren bij deze druk dan eerdere experimenten door Haber en anderen bij atmosferische druk., Nernst concludeerde echter dat het proces niet haalbaar was omdat het (op dat moment) moeilijk of bijna onmogelijk was om grote apparatuur te produceren die onder die druk kon werken.
niettemin volgden zowel Haber als Nernst de hogedrukroute om ammoniak te produceren via een katalysator. Haber ontwikkelde uiteindelijk een proces voor de productie van commerciële hoeveelheden ammoniak, en in 1906 kon hij een ammoniakconcentratie van 6% bereiken in een reactor geladen met een osmium katalysator., Dit wordt algemeen erkend als het keerpunt in de ontwikkeling van een praktisch proces voor de productie van ammoniak in commerciële hoeveelheden.
Haber realiseerde zich dat de hoeveelheid ammoniak die in een enkele gang door een converter werd gevormd, veel te laag was om commercieel interessant te zijn. Om meer ammoniak uit het make-upgas te produceren, stelde hij een recyclesysteem voor en kreeg een patent voor het concept. Haber ‘ s recycle idee veranderde de perceptie van process engineering als statisch in het voordeel van een meer dynamische aanpak., Naast het chemische reactie-evenwicht, erkende Haber dat de reactiesnelheid een bepalende factor was. In plaats van eenvoudige opbrengst in een eenmalig proces, concentreerde hij zich op ruimte-tijd opbrengst in een systeem met recycle.
BASF kocht Haber ‘ s patenten en begon met de ontwikkeling van een commercieel proces. Na het testen van meer dan 2.500 verschillende katalysatoren ontwikkelden Carl Bosch, Alvin Mittasch en andere BASF chemici een gepromoot ijzerkatalysator voor de productie van ammoniak in 1910., Het ontwikkelen van apparatuur die bestand was tegen de noodzakelijke hoge temperaturen en druk was een nog moeilijker taak. Een eerste reactor van zacht staal duurde slechts 80 uur voordat het door decarbonisatie uitvalt. Het bekleden van reactoren van zacht staal met zacht ijzer (dat niet kwetsbaar was voor decarbonisatie) en het toevoegen van groeven tussen de twee liners om waterstof vrij te geven die door de zachte ijzeren liner was verspreid, loste dit probleem op., Andere belangrijke uitdagingen waren het ontwerpen van een warmtewisselaar om het inlaatgas op reactietemperaturen te brengen en het uitlaatgas te koelen, en het ontwerpen van een methode om de katalysator op reactietemperatuur te brengen.de eerste commerciële ammoniakfabriek op basis van het Haber-Bosch-proces werd gebouwd door BASF in Oppau, Duitsland. De fabriek ging in bedrijf op Sept. 9, 1913, met een productiecapaciteit van 30 m. t. / dag.
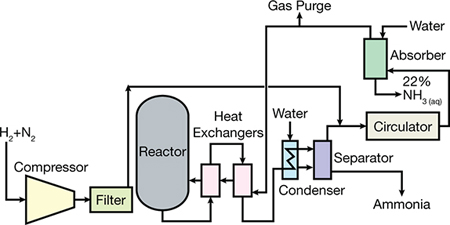
Figure figuur 1. Dit is een vereenvoudigde flowsheet van de eerste commerciële ammoniakfabriek van BASF.,
figuur 1 is een stroomschema van de eerste commerciële ammoniakinstallatie. De reactor bevatte een interne warmtewisselaar naast die op het schema.
globale productiepercentages
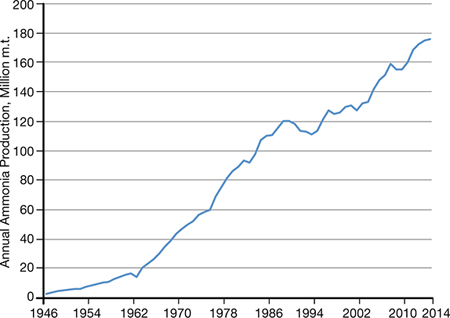
Figure figuur 2. Van 1946 tot 2014 is de wereldwijde ammoniakproductie gestaag toegenomen.de ammoniakproductie is een van de belangrijkste industrieën ter wereld geworden. Zonder de opbrengst van gewassen die mogelijk wordt gemaakt door meststoffen en chemicaliën op basis van ammoniak, zou de wereldbevolking ten minste twee tot drie miljard minder zijn dan vandaag (3)., De ammoniakproductie is sinds 1946 gestaag toegenomen (Figuur 2), en naar schatting is de jaarlijkse ammoniakproductie meer dan 100 miljard dollar waard, waarbij sommige installaties meer dan 3.000 ton NH3 per dag produceren.in 1983, ter gelegenheid van de 75ste verjaardag van de oprichting van AIChE, noemde een blue ribbon panel van vooraanstaande chemische ingenieurs wat zij geloofden dat ‘ s werelds tien grootste chemische technische prestaties waren (4)., De citatie omvatte ook de doorbraak die de productie van grote hoeveelheden ammoniak in compacte, één-eenheid planten mogelijk maakte.
in de afgelopen decennia zijn chemische ingenieurs erin geslaagd processen te creëren die tegen relatief lage kosten grote hoeveelheden ammoniak produceren. Nog 80 jaar geleden bedroeg de totale jaarlijkse productie van gesynthetiseerde ammoniak iets meer dan 300.000 m. t. dankzij doorbraken in de chemische techniek kan één moderne ammoniakfabriek meer dan 750.000 m.t./jaar produceren.,
ongeveer 88% van de jaarlijks geproduceerde ammoniak wordt verbruikt bij de vervaardiging van kunstmest. Het grootste deel van de rest gaat naar de productie van formaldehyde. China produceerde ongeveer 32,6% van de wereldwijde productie in 2014, terwijl Rusland, India en de VS respectievelijk 8,1%, 7,6% en 6,4% produceerden (1). Terwijl het grootste deel van de wereldwijde productie van ammoniak gebaseerd is op stoomreforming van aardgas, worden aanzienlijke hoeveelheden geproduceerd door kolenvergassing; de meeste vergassingsinstallaties bevinden zich in China.,
moderne produktieprocessen
de enorme toename van de vraag naar ammoniak tussen 1950 en 1980 maakte grotere, energie-efficiënte installaties noodzakelijk. Die decennia zagen ook een verandering in de ontwerpfilosofie. Tot die tijd werd een ammoniakinstallatie beschouwd als een samenstel van niet-verwante eenheden, zoals gasvoorbereiding, gaszuivering, gascompressie en ammoniaksynthese. Nieuwe innovaties en een integraal ontwerp koppelden proceseenheden op de meest effectieve en efficiënte manieren aan elkaar.
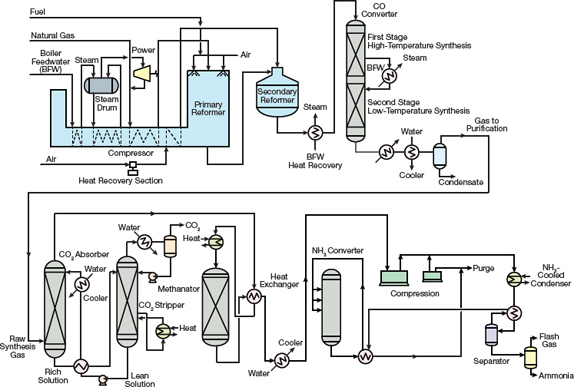
Figure figuur 3., KBR ontwierp een van de eerste ammoniakcentrales met een grote capaciteit.in het midden van de jaren zestig werd de American Oil Co. een door M. W. Kellogg (MWK) in Texas City, TX ontwikkelde ammoniakfabriek met één omzetter met een capaciteit van 544 m.t./dag. Het ontwerpconcept voor één trein (Figuur 3) was zo revolutionair dat het in 1967 de Kirkpatrick Chemical Engineering Achievement Award ontving.,
de installatie gebruikte een viercassige centrifugaalcompressor om het syngas te comprimeren tot een druk van 152 bar, en de uiteindelijke compressie tot een werkdruk van 324 bar vond plaats in een zuigercompressor. Ook werden centrifugaalcompressoren voor de synthesekringloop en koelservices geïmplementeerd, wat aanzienlijke kostenbesparingen opleverde.,
de belangrijkste verschillen tussen het MWK-proces en de processen die in eerdere ammoniakinstallaties werden gebruikt, waren:
- gebruikmakend van een centrifugale compressor als onderdeel van de synthesegascompressie
- maximaliseren van de terugwinning van afvalwarmte uit het proces
- stoom genereren uit de afvalwarmte voor gebruik in stoomturbinebestuurders
- gebruikmakend van de koelcompressor voor afvoer en atmosferische koeling.
een geïntegreerd schema dat een evenwichtige energieconsumptie, energieproductie, omvang van de apparatuur en katalysatorvolumes in de gehele installatie werd geïntegreerd.,de meeste centrales die tussen 1963 en 1993 werden gebouwd, hadden grote ontwerpen met een enkele trein, met synthesegasproductie bij 25-35 bar en ammoniaksynthese bij 150-200 bar. Een andere variant van Braun (nu KBR) bood lichte aanpassingen aan het basisontwerp. De Braun zuiveringsinstallatie gebruikte een primaire of buisvormige reformator met een lage uitlaattemperatuur en een hoge methaanlekkage om de grootte en de kosten van de reformator te verminderen. Overtollige lucht werd toegevoegd aan de secundaire reformer om het methaangehalte van de primaire reformer exit stroom te verminderen tot 1-2%., Overtollige stikstof en andere onzuiverheden werden verwijderd stroomafwaarts van de methanator. Omdat het synthesegas in wezen vrij was van onzuiverheden, werden twee axiale ammoniakconverters gebruikt om een hoge ammoniakconversie te bereiken.
sommige recent gebouwde installaties hebben een synthesegasgeneratiesysteem met slechts één reformator (geen secundaire reformator), een pressure-swing adsorption (PSA) – systeem voor H2-terugwinning en een luchtscheidingsinstallatie als bron van N2., Verbeteringen in het ontwerp van de converter, zoals radiale en horizontale katalysatorbedden, interne warmtewisselaars en synthesegasbehandeling, hebben ertoe bijgedragen dat de ammoniakconcentraties die de syntheseconvertor verlaten, werden verhoogd van ongeveer 12% tot 19-21%. Een hogere conversie per doorgang, samen met efficiëntere turbines en compressoren, verminderde het energieverbruik verder. Efficiëntere CO2-verwijderingsoplossingen, zoals kaliumcarbonaat en methyldiethanolamine (MDEA), hebben bijgedragen aan een verbeterde energie-efficiëntie. De meeste moderne installaties kunnen ammoniak produceren met een energieverbruik van 28 GJ/m.t.,
naast de ontwerp -, mechanische en metallurgische verbeteringen die in deze tijd werden aangebracht, werd de werkdruk van de synthesekringloop aanzienlijk verminderd. Toen in de jaren zestig de eerste centrale met één trein werd gebouwd, bevatte deze een hogedruksynthesekringloop. In 1962 ontving MWK een verzoek van Imperial Chemical Industries (ICI) voor een voorstel voor de bouw van een fabriek van 544 m.t./dag op hun locatie in Severnside. MWK stelde een 152-bar synthese lus in plaats van een 324-bar lus.,omdat de ontwikkeling van kinetische gegevens voor de ammoniakreactie bij 152 bar meer tijd in beslag zou nemen dan MWK nodig had om te reageren op het ICI-onderzoek, namen zij contact op met Haldor Topsøe om hun plannen te ondersteunen. Topsøe had gegevens over het volledige drukbereik dat van belang is voor MWK. Bovendien hadden ze een computerprogramma voor het berekenen van de hoeveelheid katalysator die nodig was bij de lagere bedrijfsdruk. Hoewel ICI voor Bechtel koos om de fabriek te ontwerpen, kon MWK een stroomschema voor een 544-m.t ontwikkelen.,/ dag ontwerp met centrifugale compressoren en een lagedruksynthese lus, die sommige mensen beschouwen als de belangrijkste gebeurtenis in de ontwikkeling van de single-train ammonia plant.
bij 152 bar was ongeveer tweemaal zoveel katalysator nodig als bij 324 bar, een toename die economisch haalbaar leek. Hoewel de converter tweemaal het volume nodig zou hebben, zou de lagere bedrijfsdruk de vereiste dikte van de drukschaal verminderen. Hierdoor bleef het gewicht van het metaal dat nodig was voor de converter plus de katalysator ongeveer gelijk., De lagedruksynthese lus stond ook het gebruik van centrifugale compressoren toe in plaats van zuigercompressoren. Een andere verbetering was het terugwinnen van warmte om hogedrukstoom te genereren voor stoomturbineaandrijvingen.
Installatieontwerpen in de 21e eeuw
in de eerste jaren van de 21e eeuw zijn veel verbeteringen aangebracht in de ammoniaktechnologie waardoor bestaande installaties de productie kunnen verhogen en nieuwe installaties met steeds grotere capaciteit kunnen worden gebouwd. De concurrentie tussen technologieleveranciers is vrij hevig., Drie technologie licentiegevers — KBR (Kellogg Brown en Root), Haldor Topsøe en ThyssenKrupp Industrial Solutions (TKIS) – domineren momenteel de markt. Ammonia Casale, dat een axiaal-radiaal katalysatorbeddesign biedt, is marktleider in het vernieuwen van bestaande installaties.
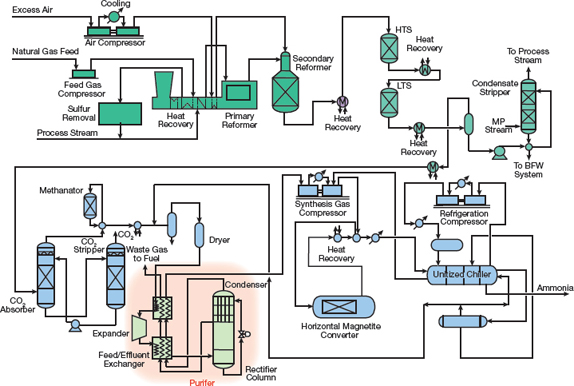
Figure figuur 4. Moderne ammoniakfabrieken ontworpen door KBR gebruiken zijn eigen zuiveringsinstallatie ontwerp.,
De meeste ammoniakinstallaties die onlangs door KBR zijn ontworpen, maken gebruik van het Zuiveringsprocédé (Figuur 4), dat een geringe reformering in de primaire reformator combineert, een vloeibare N2-reinigingsreiniger stroomafwaarts van de methanator om onzuiverheden te verwijderen en de verhouding H2:N2 aan te passen, een eigen ontwerp van een afvalwarmteboiler, een unitized chiller en een horizontale ammoniaksyntheseconvertor.
afhankelijk van de configuratie van de installatie kan het energieverbruik tot 28 GJ/m.t bedragen. omdat de secundaire reformer overtollige lucht gebruikt, kan de primaire reformer kleiner zijn dan bij conventionele ontwerpen., De cryogene zuiveringsinstallatie (in Figuur 4 in lichtgroen met een lichtoranje achtergrond), die bestaat uit een expander, condensor, feed/effluent exchanger en gelijkrichterkolom, verwijdert onzuiverheden zoals CO, CH4 en argon uit het synthesegas terwijl de verhouding H2:N2 van het vulgas in de ammoniaklus wordt aangepast aan het optimale niveau. De ammoniakconcentratie die de horizontale lagedrukvalconvertor verlaat, bedraagt 20-21%, wat de energiebehoefte van de recyclingcompressor vermindert., KBR biedt ook een lagedruk ammoniaklus die een combinatie van magnetietkatalysator en zijn eigen rutheniumkatalysator gebruikt.
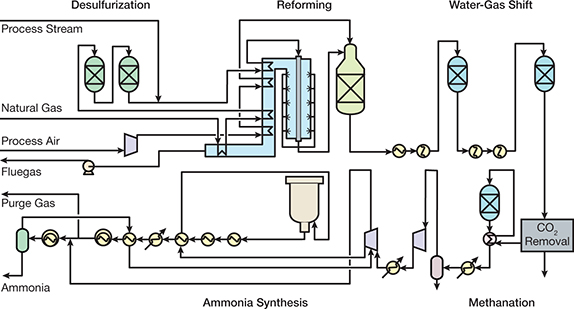
Figure figuur 5. Haldor Topsøe biedt een ammoniakfabriek met een gepatenteerde zijgestookte reformator waarin stralende branders warmte leveren voor de reformeringsreactie.
het syngasgeneratiegedeelte (of front-end) van een door Haldor Topsøe ontworpen installatie (Figuur 5) is vrij traditioneel, met uitzondering van de eigen zijgestookte reformator, die gebruik maakt van stralingbranders om warmte te leveren voor de reformeringsreactie., Haldor Topsøe biedt ook een gepatenteerde synthese-katalysator op ijzerbasis, radiale-flow converters bestaande uit een, twee, of drie bedden, en een gepatenteerde bajonet-buis afvalwarmte ketel. Meer recente ontwikkelingen zijn de S-300 en S-350 converter ontwerpen. De S-300 converter is een drie-bed radial-flow configuratie met interne warmtewisselaars, terwijl de S-350 ontwerp combineert een S-300 converter met een S-50 single-bed ontwerp met afval-warmteterugwinning tussen converters om ammoniak conversie te maximaliseren.
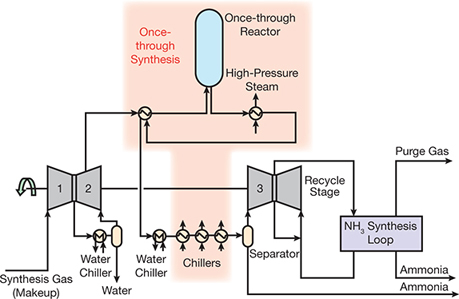
Figure figuur 6., Het dual-pressure synthesis loop design van ThyssenKrupp beschikt over een once-through reactor tussen syngascompressoren.
ThyssenKrupp biedt een conventionele installatie (Figuur 6) met een uniek ontwerp van de secundaire reformator, een eigen afvalwarmteboiler, radiale-stroomomvormers en een dual-pressure ammonia synthesis loop. Vandaag de dag kan een productiesnelheid van 3.300 m.t./dag worden bereikt met het tkis dual-pressure-proces.
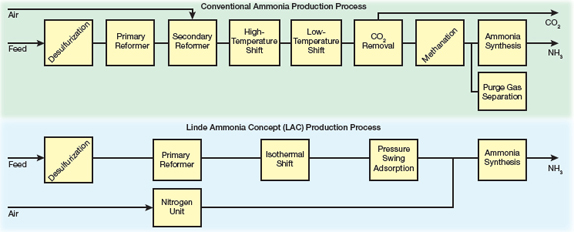
Figure figuur 7., Het Linde Ammonia Concept (LAC) is voorzien van een druk-swing adsorptie-eenheid voor hoogzuivere waterstofproductie en een luchtscheidingseenheid voor hoogzuivere stikstofproductie.
Het Linde Ammonia Concept (LAC) is een beproefd technologieprocesprogramma met meer dan 25 jaar bedrijfservaring in installaties met een capaciteit van 200 m.t./dag tot meer dan 1.750 m.t./dag., Het Lac-processchema (Figuur 7) vervangt de kostbare en complexe front-end van een conventionele ammoniakinstallatie door twee beproefde, betrouwbare proceseenheden:
- productie van ultrahoge zuiverheidswaterstof uit een stoom-methaanhervormer met PSA-zuivering
- productie van ultrahoge zuiverheidsstikstof door een cryogene stikstofgeneratie-eenheid, ook wel air separation unit (ASU) genoemd.
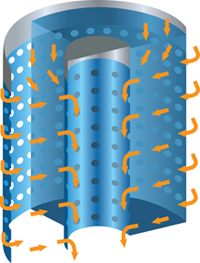
Figure figuur 8., Ammonia Casale ‘ s proces maakt gebruik van een katalysatorbed dat axiaal-radiale technologie gebruikt, die een lagere drukval en een hogere efficiëntie heeft dan standaard katalysatorbedden.
Het ontwerp van Ammonia Casale heeft een productiesnelheid van 2.000 M.t. / dag. Een van de belangrijkste kenmerken van dit ontwerp is de axiale-radiale technologie in het katalysatorbed (Figuur 8). In een axiaal-radiaal katalysatorbed gaat het grootste deel van het synthesegas in radiale richting door het katalysatorbed, waardoor een zeer lage drukval ontstaat., De rest van het gas gaat naar beneden door een bovenste laag van de katalysator in een axiale richting, waardoor de noodzaak voor een bovenste deksel op de katalysator bed. Casale ‘ s axiaal-radiale katalysator bed technologie wordt gebruikt in zowel hoge-temperatuur en lage-temperatuur shift converters, evenals in de synthese converter.
andere technologieën
sommige technologieleveranciers hebben gasverwarmde reformatoren (GHR ‘ s) aangeboden voor de productie van ammoniak in installaties met kleine capaciteit of voor capaciteitsverhogingen., In tegenstelling tot conventioneel ontworpen installaties die gebruik maken van een primaire reformer en secundaire reformer die in serie werken, gebruiken installaties met GHRs het hete procesgas van de secundaire reformer om warmte te leveren aan de primaire reformer. Dit vermindert de omvang van de primaire reformer en elimineert de CO2-uitstoot van de primaire reformer stack, waardoor het proces milieuvriendelijker wordt.,hoewel sommige ammoniakproducenten pleiten voor een gedistribueerde productie van ammoniak in kleine ammoniakfabrieken, geven de meeste bedrijven er de voorkeur aan om grote installaties te bouwen in de buurt van goedkope grondstoffenbronnen en het product per schip, spoor of pijpleiding naar de consument te vervoeren.
ammoniak uit kool
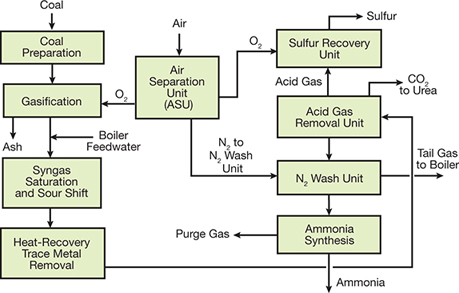
▲figuur 9. China produceert het grootste deel van zijn ammoniak uit steenkool.China produceert meer ammoniak dan enig ander land en produceert het grootste deel van zijn ammoniak uit steenkool (figuur 9).,
De basisverwerkingseenheden in een ammoniakinstallatie op basis van steenkool zijn de ASU voor de scheiding van O2 en N2 uit de lucht, de vergasser, de zuurgasverwijderingseenheid (SGS), de zuurgasverwijderingseenheid (AGRU) en de ammoniaksynthese-eenheid. Zuurstof uit de ASU wordt naar de vergasser gevoerd om steenkool om te zetten in synthesegas (H2, CO, CO2) en CH4. Er zijn veel vergassers, maar de meeste moderne vergassers zijn gebaseerd op wervelbedden die boven de atmosferische druk werken en de mogelijkheid hebben om verschillende kooltoevoer te gebruiken. Afhankelijk van het ontwerp kunnen CO-niveaus van 30-60 volumeprocent worden geproduceerd.,
na vergassing worden alle deeltjes in het synthesegas verwijderd en wordt stoom aan de SGS-eenheid toegevoegd. Het SGS-proces gebruikt typisch een kobalt en molybdeen (CoMo) katalysator die speciaal voor verrichting in een zwavelmilieu wordt ontworpen.
na vermindering van de CO-concentratie in het synthesegas tot minder dan 1 vol% wordt het syngas naar een AGRU gevoerd, waar een gekoelde methanol-wasoplossing (bv. Rectisol) CO2 en zwavel uit het synthesegas verwijdert. De CO2-overhead wordt ontlucht of naar een ureumfabriek gevoerd. De zwaveluitlaatstroom wordt toegevoerd aan een zwavelterugwinningseenheid (SRU).,
Syngas dat door de AGRU gaat, wordt doorgaans gezuiverd door een van de volgende twee methoden:
- een stikstofwasser om resterende CO en CH4 uit het syngas te verwijderen voordat het in de syntheserus wordt gevoerd
- een PSA-systeem voor co-en CH4-verwijdering.
Slotgedachten
gedurende de afgelopen 60 jaar is de ammoniakprocestechnologie drastisch verbeterd. Plant lay-outs evolueerden van multi-trein ontwerpen, vaak met verschillende aantallen treinen in de front-end en synthese loop, naar single-trein ontwerpen., De bereiding van het synthesegas aan de voorkant van de installatie nam toe van atmosferische druk tot 30-50 barg druk. De capaciteit steeg van 100 M. t. / dag tot maar liefst 3.300 m.t./dag in een enkele trein.de energie-efficiëntie is eveneens verbeterd-van een verbruik van meer dan 60 GJ/m.t. ammoniak in cokesfabrieken tot 40-50 GJ/m.t. in de eerste installaties op aardgas tot 30-40 GJ/m.t. in de eerste installaties met één trein. Moderne installaties hebben warmteterugwinning toegevoegd door stoomproductie bij een druk tot 125 barg in zowel het syngasvoorbereidingsgedeelte als de synthesecirkel.,
in termen van procesapparatuur is er een verschuiving geweest van zuigercompressoren naar centrifugaalcompressoren. Een interne warmtewisselaar is geïmplementeerd in de synthese converter om de omzetting van H2 en N2 naar NH3 te verhogen. Ontwerpers hebben gebruik gemaakt van waterstofterugwinning uit zuiveringsgas (in eenheden zoals PSA-systemen) om de productie te verbeteren of het energieverbruik van de installatie te verminderen. Ontwerpers hebben ook warmvoergasontzwavelingssystemen geïmplementeerd. Er zijn significante verbeteringen in de katalysatoren gebruikt bij het reformeren, shift conversie, methanation, en ammoniaksynthese geweest.,
om de procesbeheersing en veiligheid te verbeteren, zijn distributed control systems (DCSs) voor geavanceerde procesbeheersing, evenals safety-instrumented systems (SISs), nu standaard in ammoniakinstallaties. Voordat een proces online gaat, worden hazard and operability (HAZOP) studies en layer of protection analyses (LOPAs) uitgevoerd. De vooruitgang op het gebied van opleidingssimulatoren en onderwijspraktijken zorgt ervoor dat bedieners en ingenieurs hun taken veilig en effectief kunnen uitvoeren.,
Dit zijn slechts enkele van de duizenden verbeteringen in technologie en veiligheid die zijn doorgevoerd om van de ammoniakindustrie een van de meest productieve en veilige industrieën ter wereld te maken.
Dankbetuigingen
De auteurs erkennen de hulp van KBR, Thyssenkrupp Industrial Solutions, Haldor Topsøe, Linde en Casale voor het verstrekken van technische literatuur over hun respectieve procestechnologieën.