L’ammoniaca è fondamentale nella produzione di fertilizzanti ed è una delle sostanze chimiche sintetiche di maggior volume prodotte al mondo. Questo articolo esplora l’evoluzione della produzione di ammoniaca e descrive le attuali tecnologie di produzione.
La maggior parte delle persone associa l’odore pungente di ammoniaca (NH3) con detergenti o sali odoranti. Tuttavia, l’uso di ammoniaca in questi due prodotti rappresenta solo una piccola frazione della produzione globale totale di ammoniaca, che era di circa 176 milioni di tonnellate nel 2014 (1)., Per apprezzare dove sono oggi l’industria e la tecnologia, diamo prima un’occhiata a come siamo arrivati qui.
L’ammoniaca è nota da più di 200 anni. Joseph Priestley, un chimico inglese, isolò per la prima volta l’ammoniaca gassosa nel 1774. La sua composizione fu accertata dal chimico francese Claude Louis Berthollet nel 1785., Nel 1898, Adolph Frank e Nikodem Caro scoperto che N2 potrebbe essere risolto dal carburo di calcio di calcio cianammide, che potrebbe poi essere idrolizzato con l’acqua per formare ammoniaca (2):
CaO + 3C ↔ CaC2 + CO
CaC2 + N2 ↔ CaCN2 + C
CaCN2 + 3H2O ↔ CaCO3 + 2NH3
La produzione di notevoli quantità di ammoniaca utilizzando la cianammide processo non si è verificato fino al 20esimo secolo. Poiché questo processo richiedeva grandi quantità di energia, gli scienziati hanno concentrato i loro sforzi sulla riduzione del fabbisogno energetico.,
Il chimico tedesco Fritz Haber ha svolto alcuni dei lavori più importanti nello sviluppo della moderna industria dell’ammoniaca. Lavorare con uno studente presso l’Univ. di Karlsruhe, ha sintetizzato l’ammoniaca in laboratorio da N2 e H2.
Nel frattempo, Walther Nernst, professore di chimica fisica presso l’Univ. di Berlino, ha sviluppato un processo per fare ammoniaca passando una miscela di N2 e H2 attraverso un catalizzatore di ferro a 1.000°C e 75 barg di pressione. Fu in grado di produrre grandi quantità di ammoniaca a questa pressione rispetto ai precedenti esperimenti di Haber e altri a pressione atmosferica., Tuttavia, Nernst ha concluso che il processo non era fattibile perché era difficile o quasi impossibile (all’epoca) produrre apparecchiature di grandi dimensioni in grado di funzionare a tale pressione.
Tuttavia, sia Haber che Nernst hanno seguito la via ad alta pressione per produrre ammoniaca su un catalizzatore. Haber finalmente sviluppato un processo per la produzione di quantità commerciali di ammoniaca, e nel 1906 è stato in grado di raggiungere una concentrazione di ammoniaca 6% in un reattore caricato con un catalizzatore di osmio., Questo è generalmente riconosciuto come il punto di svolta nello sviluppo di un processo pratico per la produzione di ammoniaca in quantità commerciali.
Haber si rese conto che la quantità di ammoniaca formata in un singolo passaggio attraverso un convertitore era troppo bassa per essere di interesse commerciale. Per produrre più ammoniaca dal gas trucco, ha proposto un sistema di riciclo, e ha ricevuto un brevetto per il concetto. L’idea di riciclo di Haber ha cambiato la percezione dell’ingegneria di processo come statica a favore di un approccio più dinamico., Oltre all’equilibrio della reazione chimica, Haber riconobbe che la velocità di reazione era un fattore determinante. Invece di semplice resa in un processo una tantum, si è concentrato sulla resa spazio-temporale in un sistema con riciclo.
BASF ha acquistato i brevetti di Haber e ha iniziato lo sviluppo di un processo commerciale. Dopo aver testato più di 2.500 diversi catalizzatori, Carl Bosch, Alvin Mittasch e altri chimici BASF svilupparono un catalizzatore di ferro promosso per la produzione di ammoniaca nel 1910., Sviluppare attrezzature in grado di sopportare le alte temperature e la pressione necessarie era un compito ancora più difficile. Un primo reattore in acciaio dolce è durato solo 80 ore prima del guasto dovuto alla decarbonizzazione. Il rivestimento di reattori in acciaio dolce con ferro dolce (che non era vulnerabile alla decarbonizzazione) e l’aggiunta di scanalature tra i due rivestimenti per rilasciare idrogeno che si era diffuso attraverso il rivestimento in ferro dolce ha risolto questo problema., Altre sfide importanti includevano la progettazione di uno scambiatore di calore per portare il gas in ingresso alle temperature di reazione e raffreddare il gas in uscita, e l’elaborazione di un metodo per portare il catalizzatore alla temperatura di reazione.
Il primo impianto commerciale di ammoniaca basato sul processo Haber-Bosch è stato costruito da BASF a Oppau, in Germania. L ” impianto è andato on-stream il settembre. 9, 1913, con una capacità di produzione di 30 m. t. / giorno.
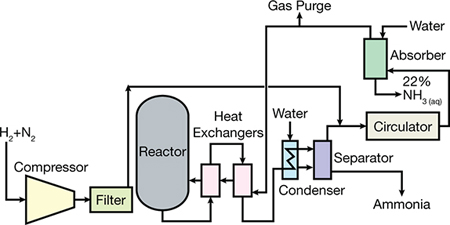
▲Figura 1. Questo è un flowsheet semplificato del primo impianto commerciale di ammoniaca di BASF.,
La figura 1 è un flowsheet del primo impianto commerciale di ammoniaca. Il reattore conteneva uno scambiatore di calore interno in aggiunta a quelli mostrati sullo schema.
Tassi di produzione globali
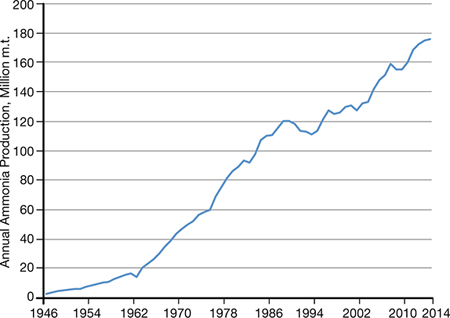
▲Figura 2. La produzione mondiale di ammoniaca è aumentata costantemente dal 1946 al 2014.
La produzione di ammoniaca è diventata una delle industrie più importanti al mondo. Senza la resa delle colture resa possibile dai fertilizzanti e dai prodotti chimici a base di ammoniaca, la popolazione mondiale sarebbe di almeno due o tre miliardi inferiore a quella attuale (3)., La produzione di ammoniaca è aumentata costantemente dal 1946 (Figura 2) e si stima che la produzione annuale di ammoniaca valga più di $100 miliardi, con alcune piante che producono più di 3.000 m.t./giorno di NH3.
Nel 1983, in occasione del 75 ° anniversario della fondazione di AIChE, un gruppo di ingegneri chimici illustri ha nominato quelli che credevano essere i dieci più grandi risultati di ingegneria chimica del mondo (4)., Abbracciando tali prodezze come farmaci miracolosi, fibre sintetiche, e l’energia atomica, la citazione comprendeva anche la svolta che ha permesso la produzione di grandi quantità di ammoniaca in impianti compatti, singola unità.
Negli ultimi decenni, gli ingegneri chimici sono riusciti a creare processi che producono grandi quantità di ammoniaca a costi relativamente bassi. Fino a 80 anni fa, la produzione annuale totale di ammoniaca sintetizzata era poco più di 300.000 m. t. Grazie alle innovazioni dell’ingegneria chimica, un moderno impianto di ammoniaca può produrre più di 750.000 m. t. / anno.,
Circa l ‘ 88% dell’ammoniaca prodotta annualmente viene consumata nella produzione di fertilizzanti. La maggior parte del resto va nella produzione di formaldeide. La Cina ha prodotto circa il 32,6% della produzione globale nel 2014, mentre Russia, India e Stati Uniti hanno prodotto rispettivamente l ‘ 8,1%, il 7,6% e il 6,4% (1). Mentre la maggior parte della produzione globale di ammoniaca si basa sul reforming a vapore del gas naturale, quantità significative sono prodotte dalla gassificazione del carbone; la maggior parte degli impianti di gassificazione si trova in Cina.,
Processi produttivi moderni
L’enorme aumento della domanda di ammoniaca dal 1950 al 1980 ha reso necessari impianti più grandi e più efficienti dal punto di vista energetico. Quei decenni hanno visto anche un cambiamento nella filosofia del design. Fino a quel momento, un impianto di ammoniaca era considerato come un assemblaggio di unità non correlate, come la preparazione del gas, la purificazione del gas, la compressione del gas e la sintesi dell’ammoniaca. Nuove innovazioni e un design integrale hanno unito le unità di processo nei modi più efficaci ed efficienti.
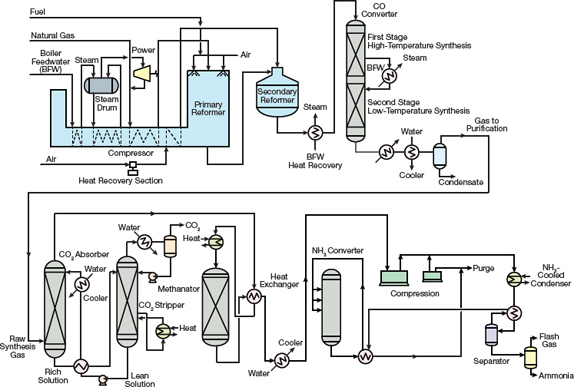
▲Figura 3., KBR ha progettato uno dei primi impianti di ammoniaca a treno singolo di grande capacità.
A metà degli anni 1960, l’American Oil Co. installato un impianto di ammoniaca a convertitore singolo progettato da M. W. Kellogg (MWK) a Texas City, TX, con una capacità di 544 m.t./giorno. Il concetto di design a treno singolo (Figura 3) era così rivoluzionario che ricevette il Kirkpatrick Chemical Engineering Achievement Award nel 1967.,
L’impianto ha utilizzato un compressore centrifugo a quattro casse per comprimere il syngas a una pressione di 152 bar e la compressione finale a una pressione di esercizio di 324 bar si è verificata in un compressore alternativo. Sono stati inoltre implementati compressori centrifughi per il ciclo di sintesi e i servizi di refrigerazione, che hanno consentito notevoli risparmi sui costi.,
Le principali differenze tra il MWK processo e i processi utilizzati nel precedente ammoniaca piante incluso:
- l’utilizzo di un compressore centrifugo come parte del gas di sintesi compressione
- massimizzare il recupero di calore di scarto dal processo
- la generazione di vapore dal calore di scarto per l’uso in turbina a vapore driver
- usare il compressore per refrigerazione per fatiscente e atmosferica di refrigerazione.
Uno schema integrato che ha bilanciato il consumo di energia, la produzione di energia, le dimensioni delle apparecchiature e i volumi dei catalizzatori è stato incorporato in tutto l’impianto.,
La maggior parte degli impianti costruiti tra il 1963 e il 1993 aveva grandi progetti a treno singolo con produzione di gas di sintesi a 25-35 bar e sintesi di ammoniaca a 150-200 bar. Un’altra variante di Braun (ora KBR) offriva leggere modifiche al design di base. Gli impianti di processo Braun Purifier utilizzavano un reformer primario o tubolare con una bassa temperatura di uscita e un’elevata perdita di metano per ridurre le dimensioni e il costo del reformer. L’aria in eccesso è stata aggiunta al reformer secondario per ridurre il contenuto di metano del flusso di uscita del reformer primario all ‘ 1-2%., L’eccesso di azoto e altre impurità sono stati rimossi a valle del metanatore. Poiché il gas di sintesi era essenzialmente privo di impurità, sono stati utilizzati due convertitori di ammoniaca a flusso assiale per ottenere un’elevata conversione dell’ammoniaca.
Alcuni impianti di recente costruzione hanno un sistema di generazione di gas di sintesi con un solo reformer (nessun reformer secondario), un sistema di adsorbimento a pressione (PSA) per il recupero di H2 e un impianto di separazione dell’aria come fonte di N2., I miglioramenti nella progettazione del convertitore, come i letti catalizzatori radiali e orizzontali, gli scambiatori di calore interni e il trattamento dei gas di sintesi, hanno contribuito ad aumentare le concentrazioni di ammoniaca in uscita dal convertitore di sintesi da circa il 12% al 19-21%. Una conversione più elevata per passaggio, insieme a turbine e compressori più efficienti, ha ridotto ulteriormente il consumo di energia. Soluzioni di rimozione della CO2 più efficienti, come il carbonato di potassio e la metildietanolammina (MDEA), hanno contribuito a migliorare l’efficienza energetica. La maggior parte degli impianti moderni può produrre ammoniaca con un consumo energetico di 28 GJ / m. t.,
Oltre ai miglioramenti progettuali, meccanici e metallurgici apportati durante questo periodo, la pressione di esercizio del ciclo di sintesi è stata significativamente ridotta. Quando il primo impianto monotreno è stato costruito nel 1960, conteneva un ciclo di sintesi ad alta pressione. Nel 1962, MWK ricevette un’inchiesta dalla Imperial Chemical Industries (Imperial) per una proposta di costruzione di un impianto di 544 m.t./giorno nel loro sito di Severnside. MWK ha proposto un ciclo di sintesi a 152 bar invece di un ciclo a 324 bar.,
Poiché lo sviluppo di dati cinetici per la reazione di ammoniaca a 152 bar richiederebbe più tempo di quanto MWK avesse dovuto rispondere all’inchiesta IC, hanno contattato Haldor Topsøe per sostenere i loro piani. Topsøe disponeva di dati relativi all’intero intervallo di pressione di interesse per MWK. Inoltre, avevano un programma per computer per calcolare la quantità di catalizzatore richiesta alla pressione di esercizio inferiore. Anche se IC ha scelto Bechtel per progettare l’impianto, MWK è stata in grado di sviluppare un flowsheet per un 544-m.t.,/ day design con compressori centrifughi e un loop di sintesi a bassa pressione, che alcuni considerano il singolo evento più importante nello sviluppo dell’impianto di ammoniaca a treno singolo.
Era necessario circa il doppio del catalizzatore a 152 bar rispetto a 324 bar, un aumento che sembrava economicamente fattibile. Anche se il convertitore avrebbe bisogno di due volte il volume, la pressione di esercizio inferiore ridurrebbe lo spessore richiesto del guscio di pressione. Di conseguenza, il peso del metallo richiesto per il convertitore più il catalizzatore è rimasto all’incirca lo stesso., Il circuito di sintesi a bassa pressione ha anche permesso l’uso di compressori centrifughi invece di compressori alternativi. Un altro miglioramento è stato il recupero del calore per generare vapore ad alta pressione per gli azionamenti delle turbine a vapore.
Progetti di impianti nel 21 ° secolo
Durante i primi anni del 21 ° secolo, sono stati apportati molti miglioramenti nella tecnologia degli impianti di ammoniaca che consentono agli impianti esistenti di aumentare i tassi di produzione e di costruire nuovi impianti con capacità sempre maggiori. La concorrenza tra i fornitori di tecnologia è piuttosto feroce., Tre licenziatari tecnologici-KBR (Kellogg Brown e Root), Haldor Topsøe e ThyssenKrupp Industrial Solutions (TKIS) — attualmente dominano il mercato. Ammonia Casale, che offre un design a letto catalizzatore assiale-radiale, è leader di mercato nei rinnovi di impianti esistenti.
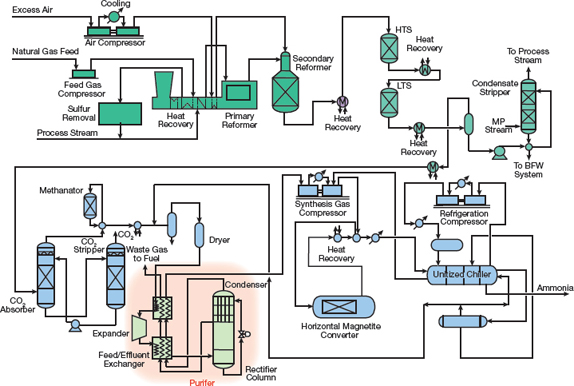
▲Figura 4. I moderni impianti di ammoniaca progettati da KBR impiegano il suo design proprietario di depuratore.,
La maggior parte degli impianti di ammoniaca recentemente progettati da KBR utilizza il suo processo di depuratore (Figura 4), che combina reforming a bassa gravità nel reformer primario, un depuratore di lavaggio N2 liquido a valle del metanatore per rimuovere le impurità e regolare il rapporto H2:N2, un design proprietario della caldaia di calore residuo, un refrigeratore
A seconda della configurazione dell’impianto, il consumo di energia può essere fino a 28 GJ / m.t. Poiché il reformer secondario utilizza aria in eccesso, il reformer primario può essere più piccolo rispetto ai progetti convenzionali., Il depuratore criogenico (mostrato in Figura 4 in verde chiaro con uno sfondo arancione chiaro), che consiste in un espansore, condensatore, scambiatore di alimentazione/effluente e colonna raddrizzatore, rimuove le impurità come CO, CH4 e argon dal gas di sintesi mentre regola il rapporto H2:N2 del gas di trucco nel ciclo dell’ammoniaca al livello ottimale. La concentrazione di ammoniaca che esce dal convertitore orizzontale a bassa caduta di pressione è del 20-21%, il che riduce il fabbisogno energetico del compressore di riciclo., KBR inoltre offre un ciclo a bassa pressione dell’ammoniaca che impiega una combinazione del catalizzatore della magnetite e del suo catalizzatore proprietario del rutenio.
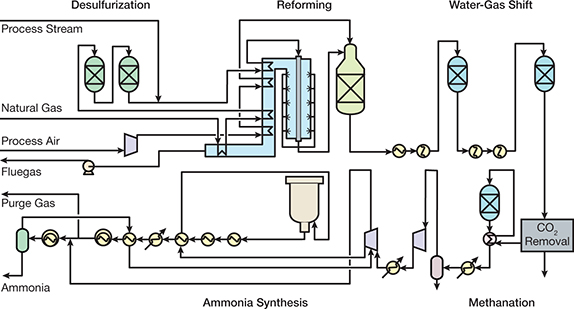
▲Figura 5. Haldor Topsøe offre un impianto di ammoniaca dotato di un reformer a combustione laterale proprietario in cui i bruciatori radianti forniscono calore per la reazione di reforming.
La sezione di generazione syngas (o front-end) di un impianto progettato da Haldor Topsøe (Figura 5) è piuttosto tradizionale con l’eccezione del suo reformer a fuoco laterale proprietario, che utilizza bruciatori radianti per fornire calore per la reazione di reforming., Haldor Topsøe offre anche un catalizzatore di sintesi proprietario a base di ferro, convertitori a flusso radiale costituiti da uno, due o tre letti e una caldaia proprietaria a baionetta. Gli sviluppi più recenti includono i modelli di convertitori S-300 e S-350. Il convertitore S-300 è una configurazione a flusso radiale a tre letti con scambiatori di calore interni, mentre il design S-350 combina un convertitore S-300 con un design a letto singolo S-50 con recupero del calore di scarto tra convertitori per massimizzare la conversione dell’ammoniaca.
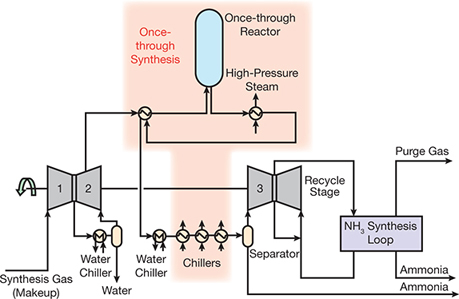
▲Figura 6., Il design del ciclo di sintesi a doppia pressione di ThyssenKrupp presenta un reattore una sola volta tra i compressori syngas.
ThyssenKrupp offre un impianto convenzionale (Figura 6) con un design reformer secondario unico, una caldaia proprietaria di calore di scarto, convertitori a flusso radiale e un ciclo di sintesi dell’ammoniaca a doppia pressione. Oggi è possibile ottenere una velocità di produzione di 3.300 m.t./giorno utilizzando il processo a doppia pressione TKIS.
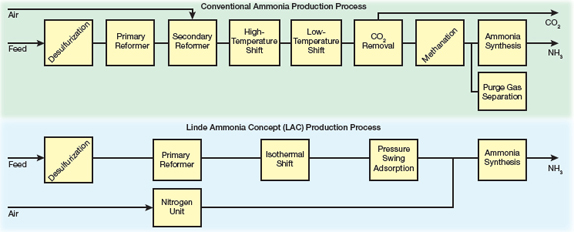
▲Figura 7., Il Linde Ammonia Concept (LAC) è dotato di un’unità di adsorbimento a pressione oscillante per la produzione di idrogeno ad alta purezza e di un’unità di separazione dell’aria per la produzione di azoto ad alta purezza.
Il Linde Ammonia Concept (LAC) è uno schema di processo tecnologico consolidato con oltre 25 anni di esperienza operativa in impianti con capacità da 200 m.t. / giorno a oltre 1.750 m.t. / giorno., La LAC schema di processo (Figura 7) sostituisce il costoso e complesso di front-end di un convenzionale impianto di ammoniaca con due ben collaudata, affidabile unità di processo:
- produzione di ultra-alta purezza dell’idrogeno da steam-metano riformatore con PSA purificazione
- produzione di ultra-alta purezza azoto da un criogenica dell’azoto unità di generazione, noto anche come unità di separazione dell’aria (ASU).
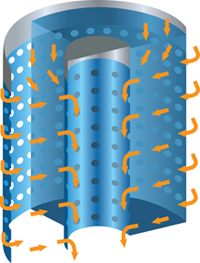
▲Figura 8., Il processo di ammoniaca Casale impiega un letto catalizzatore che sfrutta la tecnologia assiale-radiale, che ha una caduta di pressione inferiore e una maggiore efficienza rispetto ai letti catalizzatori standard.
L’impianto di Ammonia Casale ha una velocità di produzione di 2.000 m.t. / giorno. Una delle caratteristiche chiave di questo progetto è la tecnologia assiale-radiale nel letto catalizzatore (Figura 8). In un letto catalizzatore assiale-radiale, la maggior parte del gas di sintesi passa attraverso il letto catalizzatore in direzione radiale, creando una caduta di pressione molto bassa., Il resto del gas passa attraverso uno strato superiore di catalizzatore in direzione assiale, eliminando la necessità di un coperchio superiore sul letto del catalizzatore. La tecnologia a letto catalizzatore assiale-radiale di Casale è utilizzata sia nei convertitori a turni ad alta temperatura che a bassa temperatura, nonché nel convertitore di sintesi.
Altre tecnologie
Alcuni fornitori di tecnologia hanno offerto reformers riscaldati a gas (GHRS) per la produzione di ammoniaca in impianti di piccola capacità o per aumenti di capacità., A differenza degli impianti convenzionalmente progettati che utilizzano un reformer primario e un reformer secondario che operano in serie, gli impianti con GHRs utilizzano il gas di processo caldo dal reformer secondario per fornire calore al reformer primario. Ciò riduce le dimensioni del reformer primario ed elimina le emissioni di CO2 dallo stack del reformer primario, rendendo il processo più rispettoso dell’ambiente.,
Anche se alcuni produttori di ammoniaca sostengono la produzione distribuita di ammoniaca in piccoli impianti di ammoniaca, la maggior parte delle aziende preferisce costruire grandi impianti vicino a fonti di materie prime economiche e trasportare il prodotto via nave, ferrovia o conduttura ai consumatori.
Ammoniaca da carbone
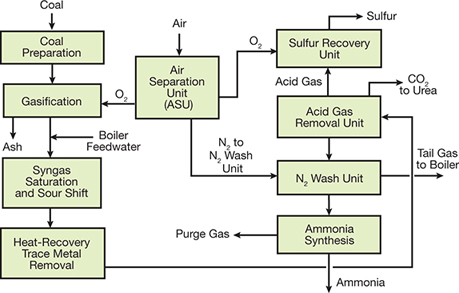
▲Figura 9. La Cina produce la maggior parte della sua ammoniaca dal carbone.
La Cina produce più ammoniaca di qualsiasi altro paese e produce la maggior parte della sua ammoniaca dal carbone (Figura 9).,
Le unità di elaborazione di base in un impianto di ammoniaca a base di carbone sono l’ASU per la separazione di O2 e N2 dall’aria, il gassificatore, l’unità sour gas shift (SGS), l’unità di rimozione del gas acido (AGRU) e l’unità di sintesi dell’ammoniaca. L’ossigeno dell’ASU viene alimentato al gassificatore per convertire il carbone in gas di sintesi (H2, CO, CO2) e CH4. Ci sono molti disegni gassificatore, ma la maggior parte dei gassificatori moderni si basano su letti fluidizzati che operano al di sopra della pressione atmosferica e hanno la capacità di utilizzare diversi alimentazioni di carbone. A seconda del progetto, possono essere prodotti livelli di CO del 30-60% in volume.,
Dopo la gassificazione, qualsiasi particolato nel gas di sintesi viene rimosso e il vapore viene aggiunto all’unità SGS. Il processo SGS utilizza tipicamente un catalizzatore di cobalto e molibdeno (CoMo) appositamente progettato per il funzionamento in un ambiente di zolfo.
Dopo aver ridotto la concentrazione di CO nel gas di sintesi a meno di 1 vol%, il syngas viene alimentato in un AGRU, dove una soluzione di lavaggio a metanolo refrigerata (ad esempio, Rectisol) rimuove CO2 e zolfo dal gas di sintesi. Il sovraccarico di CO2 viene scaricato o alimentato a un impianto di urea. Il flusso di uscita dello zolfo viene alimentato a un’unità di recupero dello zolfo (SRU).,
Il syngas che passa attraverso l’AGRU viene tipicamente purificato con uno dei due metodi:
- un’unità di lavaggio dell’azoto per rimuovere CO e CH4 residui dal syngas prima che venga alimentato al ciclo di sintesi
- un sistema PSA per la rimozione di CO e CH4.
Pensieri di chiusura
Negli ultimi 60 anni, la tecnologia di processo dell’ammoniaca è migliorata drasticamente. I layout dell’impianto si sono evoluti da progetti multi-treno, spesso con un numero diverso di treni nel front-end e nel ciclo di sintesi, a progetti a treno singolo., La preparazione del gas di sintesi nella parte anteriore dell’impianto è aumentata dalla pressione atmosferica alla pressione di 30-50 barg. Le capacità sono aumentate da 100 m. t. / giorno fino a 3.300 m. t. / giorno in un solo treno.
Sono migliorate anche le efficienze energetiche, dai consumi ben superiori ai 60 GJ/m.t. di ammoniaca negli impianti a base di coke ai 40-50 GJ/m.t. nei primi impianti a gas naturale ai 30-40 GJ / m.t. nei primi impianti a treno singolo. Gli impianti moderni hanno aggiunto il recupero di calore mediante produzione di vapore a pressioni fino a 125 barg sia nella sezione di preparazione del syngas che nel ciclo di sintesi.,
In termini di apparecchiature di processo, c’è stato un passaggio da compressori alternativi a compressori centrifughi. Uno scambiatore di calore interno è stato implementato nel convertitore di sintesi per aumentare la conversione di H2 e N2 in NH3. I progettisti hanno sfruttato il recupero dell’idrogeno dal gas di spurgo (in unità come i sistemi PSA) per migliorare la produzione o ridurre il consumo energetico dell’impianto. I progettisti hanno anche implementato sistemi di desolforazione del gas di alimentazione calda. Ci sono stati miglioramenti significativi nei catalizzatori utilizzati nel reforming, nella conversione di spostamento, nella metanazione e nella sintesi dell’ammoniaca.,
Per migliorare il controllo e la sicurezza dei processi, i sistemi di controllo distribuito (DCSS) per il controllo avanzato dei processi, così come i sistemi di sicurezza strumentati (SISS), sono ora standard negli impianti di ammoniaca. Prima che qualsiasi processo vada online, vengono eseguiti studi di pericolosità e operabilità (HAZOP) e analisi del livello di protezione (LOPAs). I progressi nei simulatori di formazione e nelle pratiche educative garantiscono che gli operatori e gli ingegneri possano svolgere le loro funzioni in modo sicuro ed efficace.,
Questi sono solo alcuni dei migliaia di miglioramenti nella tecnologia e nella sicurezza che sono stati implementati per rendere l’industria dell’ammoniaca una delle industrie più produttive e sicure al mondo.
Riconoscimenti
Gli autori riconoscono l’assistenza di KBR, ThyssenKrupp Industrial Solutions, Haldor Topsøe, Linde e Casale per fornire letteratura tecnica sulle rispettive tecnologie di processo.