El amoníaco es crítico en la fabricación de fertilizantes y es uno de los productos químicos sintéticos de mayor volumen producidos en el mundo. Este artículo explora la evolución de la producción de amoníaco y describe las tecnologías de fabricación actuales.
La mayoría de las personas asocian el olor acre del amoníaco (NH3) con limpiadores o sales aromáticas. Sin embargo, el uso de amoníaco en estos dos productos representa solo una pequeña fracción de la producción total mundial de amoníaco, que fue de alrededor de 176 millones de toneladas métricas en 2014 (1)., Para apreciar dónde están la industria y la tecnología hoy en día, primero echemos un vistazo a cómo llegamos aquí.
El amoníaco se conoce desde hace más de 200 años. Joseph Priestley, un químico inglés, aisló por primera vez amoníaco gaseoso en 1774. Su composición fue comprobada por el químico francés Claude Louis Berthollet en 1785., En 1898, Adolph Frank y Nikodem Caro encontraron que el N2 podía ser fijado por carburo de calcio para formar cianamida de calcio, que luego podría hidrolizarse con agua para formar amoníaco (2):
CaO + 3C ↔ CaC2 + CO
CaC2 + N2 ↔ CaCN2 + C
CaCN2 + 3H2O ↔ CaCO3 + 2NH3
la producción de cantidades significativas de amoníaco utilizando el proceso de cianamida no se producen hasta principios del siglo 20. Debido a que este proceso requería grandes cantidades de energía, los científicos centraron sus esfuerzos en reducir las necesidades de energía.,
el químico alemán Fritz Haber realizó algunos de los trabajos más importantes en el desarrollo de la industria moderna del amoníaco. Trabajando con un estudiante en la Univ. de Karlsruhe, sintetizó amoníaco en el laboratorio a partir de N2 y H2.
mientras tanto, Walther Nernst, profesor de Química Física en la Univ. de Berlín, desarrolló un proceso para hacer amoníaco pasando una mezcla de N2 y H2 A través de un catalizador de hierro a 1.000°C y 75 barg de presión. Fue capaz de producir mayores cantidades de amoníaco a esta presión que los experimentos anteriores de Haber y otros a presión atmosférica., Sin embargo, Nernst concluyó que el proceso no era factible porque era difícil o casi imposible (en ese momento) producir equipos grandes capaces de operar a esa presión.
Sin embargo, tanto Haber como Nernst siguieron la ruta de alta presión para producir amoníaco sobre un catalizador. Haber finalmente desarrolló un proceso para producir cantidades comerciales de amoníaco, y en 1906 fue capaz de lograr una concentración de amoníaco del 6% en un reactor cargado con un catalizador de osmio., Esto se reconoce generalmente como el punto de inflexión en el desarrollo de un proceso práctico para la producción de amoníaco en cantidades comerciales.
Haber se dio cuenta de que la cantidad de amoníaco formado en una sola pasada a través de un convertidor era demasiado baja para ser de interés comercial. Para producir más amoníaco a partir del gas de maquillaje, propuso un sistema de reciclaje, y recibió una patente para el concepto. La idea de reciclaje de Haber cambió la percepción de la ingeniería de procesos como estática en favor de un enfoque más dinámico., Además del equilibrio de reacción química, Haber reconoció que la velocidad de reacción era un factor determinante. En lugar de un simple rendimiento en un proceso de una sola vez, se concentró en el rendimiento espacio-tiempo en un sistema con reciclaje.
BASF compró las patentes de Haber y comenzó el desarrollo de un proceso comercial. Después de probar más de 2.500 catalizadores diferentes, Carl Bosch, Alvin Mittasch y otros químicos de BASF desarrollaron un catalizador de hierro promovido para la producción de amoníaco en 1910., El desarrollo de equipos que pudieran soportar las altas temperaturas y la presión necesarias era una tarea aún más difícil. Un primer reactor de acero dulce duró solo 80 horas antes de fallar debido a la descarbonización. El revestimiento de reactores de acero dulce con hierro blando (que no era vulnerable a la descarbonización) y la adición de ranuras entre los dos revestimientos para liberar hidrógeno que se había difundido a través del revestimiento de hierro blando resolvió este problema., Otros desafíos importantes incluyeron el diseño de un intercambiador de calor para llevar el gas de entrada a las temperaturas de reacción y enfriar el gas de salida, y la elaboración de un método para llevar el catalizador a la temperatura de reacción.
la primera planta comercial de amoníaco basada en el proceso Haber-Bosch fue construida por BASF en Oppau, Alemania. La planta se puso en marcha en septiembre. 9, 1913, con una capacidad de producción de 30 m. t. / día.
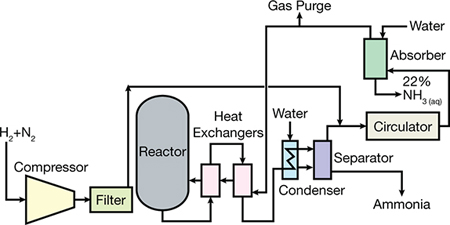
▲Figura 1. Este es un diagrama de flujo simplificado de la primera planta de amoníaco comercial de BASF.,
La Figura 1 es un diagrama de flujo de la primera planta comercial de amoníaco. El reactor contenía un intercambiador de calor interno además de los mostrados en el esquema.
tasas de producción Global
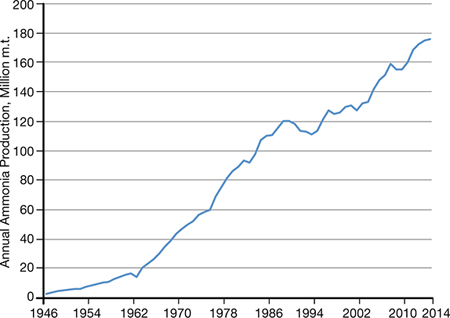
▲Figura 2. La producción mundial de amoníaco ha aumentado constantemente desde 1946 hasta 2014.
la producción de amoníaco se ha convertido en una de las industrias más importantes del mundo. Sin el rendimiento de los cultivos hecho posible por los fertilizantes y productos químicos a base de amoníaco, la población mundial sería al menos de dos a tres mil millones menos de lo que es hoy (3)., La producción de amoníaco ha aumentado constantemente desde 1946 (Figura 2), y se estima que la producción anual de amoníaco vale más de 1 100 mil millones, con algunas plantas que producen más de 3,000 m.t./día de NH3.
en 1983, con motivo del 75 aniversario de la fundación de AIChE, un panel de distinguidos ingenieros químicos nombró lo que creían que eran los diez mayores logros de ingeniería química del Mundo (4)., Abarcando hazañas como las drogas milagrosas, las fibras sintéticas y la energía atómica, la cita también incluyó el avance que permitió la producción de grandes cantidades de amoníaco en plantas compactas de una sola unidad.
en las últimas décadas, los ingenieros químicos han logrado crear procesos que producen grandes cantidades de amoníaco a costos relativamente bajos. Tan recientemente como hace 80 años, la producción anual total de amoníaco sintetizado fue de poco más de 300,000 M. t. gracias a los avances de Ingeniería Química, una planta moderna de amoníaco puede producir más de 750,000 m.t./año.,
aproximadamente el 88% del amoníaco producido anualmente se consume en la fabricación de fertilizantes. La mayor parte del resto se destina a la producción de formaldehído. China produjo alrededor del 32,6% de la producción mundial en 2014, mientras que Rusia, India y Estados Unidos produjeron el 8,1%, el 7,6% y el 6,4%, respectivamente (1). Si bien la mayor parte de la producción mundial de amoníaco se basa en el reformado con vapor de gas natural, cantidades significativas se producen mediante la gasificación del carbón; la mayoría de las plantas de gasificación se encuentran en China.,
procesos de producción modernos
El tremendo aumento de la demanda de amoníaco de 1950 a 1980 hizo necesarias plantas más grandes y eficientes energéticamente. Esas décadas también vieron un cambio en la filosofía del diseño. Hasta ese momento, una planta de amoníaco se consideraba un conjunto de unidades no relacionadas, como la preparación de gas, la purificación de gas, la compresión de gas y la síntesis de amoníaco. Las nuevas innovaciones y un diseño integral vincularon las unidades de proceso de la manera más efectiva y eficiente.
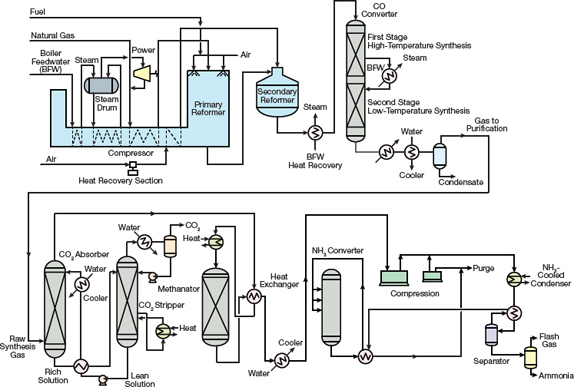
▲Figura 3., KBR diseñó una de las primeras plantas de amoníaco de un solo tren y gran capacidad.
a mediados de la década de 1960, la American Oil Co. se instaló una planta de amoníaco de un solo convertidor diseñada por M. W. Kellogg (MWK) en Texas City, TX, con una capacidad de 544 m.t./día. El concepto de diseño de tren único (Figura 3) fue tan revolucionario que recibió el Premio Kirkpatrick Chemical Engineering Achievement Award en 1967.,
la planta utilizó un compresor centrífugo de cuatro cajas para comprimir el gas de síntesis a una presión de 152 bar, y la compresión final a una presión de funcionamiento de 324 bar se produjo en un compresor alternativo. También se implementaron compresores centrífugos para el bucle de síntesis y los servicios de refrigeración, lo que proporcionó un importante ahorro de costos.,
las diferencias clave entre el proceso MWK y los procesos utilizados en plantas de amoníaco anteriores incluyeron:
- utilizando un compresor centrífugo como parte de la compresión de gas de síntesis
- maximizando la recuperación de calor residual del proceso
- generando vapor a partir del calor residual para su uso en controladores de turbinas de vapor
- utilizando el compresor de refrigeración para el deterioro y la refrigeración atmosférica.
se incorporó un esquema integrado que equilibraba el consumo de energía, la producción de energía, el tamaño del equipo y los volúmenes de catalizador en toda la planta.,
La mayoría de las plantas construidas entre 1963 y 1993 tenían grandes diseños de un solo tren con producción de gas de síntesis a 25-35 bar y síntesis de amoníaco a 150-200 bar. Otra variación de Braun (ahora KBR) ofreció ligeras modificaciones al diseño básico. Las plantas de proceso del purificador de Braun utilizaron un reformador primario o tubular con una temperatura de salida baja y una fuga de metano alta para reducir el tamaño y el costo del reformador. El exceso de aire se añadió al reformador secundario para reducir el contenido de metano de la corriente de salida del reformador primario a 1-2%., El exceso de nitrógeno y otras impurezas se eliminaron aguas abajo del metanador. Debido a que el gas de síntesis estaba esencialmente libre de impurezas, se utilizaron dos convertidores de amoníaco de flujo axial para lograr una alta conversión de amoníaco.
algunas plantas de reciente construcción tienen un sistema de generación de gas de síntesis con un solo reformador (sin reformador secundario), un sistema de adsorción por oscilación de presión (PSA) para la recuperación de H2 y una planta de separación de aire como fuente de N2., Las mejoras en el diseño del convertidor, como las camas catalíticas radiales y horizontales, los intercambiadores de calor internos y el tratamiento de gas de síntesis, ayudaron a aumentar las concentraciones de amoníaco que salen del convertidor de síntesis de aproximadamente 12% a 19-21%. Una mayor conversión por pasada, junto con turbinas y compresores más eficientes, redujo aún más el consumo de energía. Las soluciones de eliminación de CO2 más eficientes, como el carbonato de potasio y la metildietanolamina (MDEA), han contribuido a mejorar la eficiencia energética. La mayoría de las plantas modernas pueden producir amoníaco con un consumo de energía de 28 GJ / M. t.,
además de las mejoras de diseño, Mecánicas y metalúrgicas realizadas durante este tiempo, la presión de funcionamiento del bucle de síntesis se redujo significativamente. Cuando se construyó la primera planta de un solo tren en la década de 1960, contenía un bucle de síntesis de alta presión. En 1962, MWK recibió una solicitud de Imperial Chemical Industries (Imperial) para una propuesta para construir una planta de 544 m.t./día en su sitio Severnside. MWK propuso un bucle de síntesis de 152 bar en lugar de un bucle de 324 bar.,
debido a que el desarrollo de datos cinéticos para la reacción de amoníaco a 152 bar tomaría más tiempo del que MWK tuvo para responder a la consulta de I, se pusieron en contacto con Haldor Topsøe para apoyar sus planes. Topsøe tenía datos que cubrían todo el rango de presión de interés para MWK. Además, tenían un programa informático para calcular la cantidad de catalizador que se requería a la presión de funcionamiento más baja. A pesar de que MW eligió a Bechtel para diseñar la planta, MWK fue capaz de desarrollar un diagrama de flujo para un 544-m.t.,/ diseño de día con compresores centrífugos y un bucle de síntesis de baja presión, que algunas personas consideran el evento más importante en el desarrollo de la planta de amoníaco de un solo tren.
se requirió aproximadamente el doble de catalizador a 152 bar que a 324 bar, un aumento que parecía económicamente viable. Aunque el convertidor necesitaría el doble del volumen, la presión de funcionamiento más baja reduciría el grosor requerido de la carcasa de presión. Como resultado, el peso del metal requerido para el convertidor más el catalizador se mantuvo aproximadamente igual., El bucle de síntesis de baja presión también permitió el uso de compresores centrífugos en lugar de compresores alternativos. Otra mejora fue la recuperación de calor para generar vapor de alta presión para motores de turbinas de vapor.
diseños de plantas en el siglo XXI
durante los primeros años del siglo XXI, se realizaron muchas mejoras en la tecnología de plantas de amoníaco que permiten que las plantas existentes aumenten las tasas de producción y que se construyan nuevas plantas con capacidades cada vez mayores. La competencia entre los proveedores de tecnología es bastante feroz., Tres licenciantes de tecnología — KBR (Kellogg Brown y Root), Haldor Topsøe y ThyssenKrupp Industrial Solutions (TKIS) – dominan actualmente el mercado. Amoniaco Casale, que ofrece un diseño de lecho catalizador axial-radial, es líder del mercado en renovaciones de plantas existentes.
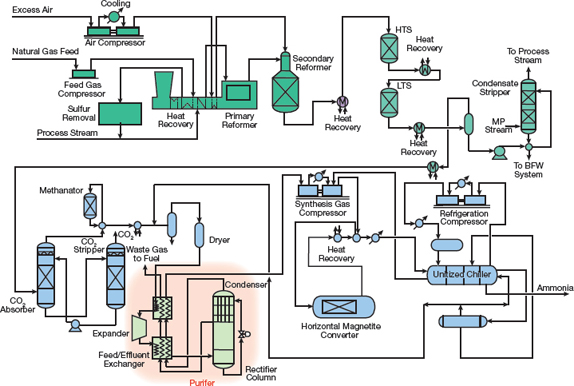
▲Figura 4. Las plantas modernas de amoníaco diseñadas por KBR emplean su diseño purificador patentado.,
La mayoría de las plantas de amoníaco recientemente diseñadas por KBR utilizan su proceso de purificador (Figura 4), que combina el reformado de baja gravedad en el reformador primario, un purificador de lavado líquido n2 aguas abajo del metanador para eliminar impurezas y ajustar la relación H2:N2, un diseño patentado de caldera de calor residual, un enfriador unificado y un convertidor horizontal de síntesis de amoníaco.
dependiendo de la configuración de la planta, el consumo de energía puede ser tan bajo como 28 GJ/M.t. debido a que el reformador secundario utiliza exceso de aire, el reformador primario puede ser más pequeño que en diseños convencionales., El purificador criogénico (que se muestra en la Figura 4 en verde claro con un fondo naranja claro), que consiste en un expansor, condensador, intercambiador de alimentación/efluente y columna rectificadora, elimina impurezas como CO, CH4 y argón del gas de síntesis mientras ajusta la relación H2:N2 del gas de maquillaje en el bucle de amoníaco al nivel óptimo. La concentración de amoníaco que sale del convertidor horizontal de baja caída de presión es del 20-21%, lo que reduce los requisitos de energía para el compresor de reciclaje., KBR también ofrece un bucle de amoníaco de baja presión que emplea una combinación de catalizador de magnetita y su catalizador de rutenio patentado.
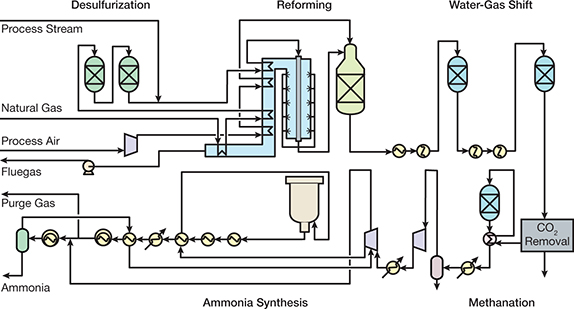
▲Figura 5. Haldor Topsøe ofrece un diseño de planta de amoníaco que tiene un reformador de combustión lateral patentado en el que los quemadores radiantes suministran calor para la reacción de reforma.
la sección de generación de gas de síntesis (o front end) de una planta diseñada por Haldor Topsøe (Figura 5) es bastante tradicional, con la excepción de su reformador de combustión lateral patentado, que utiliza quemadores radiantes para suministrar calor para la reacción de reformado., Haldor Topsøe también ofrece un catalizador de síntesis a base de hierro patentado, convertidores de flujo radial que consisten en una, dos o tres camas, y una caldera de calor residual de tubo de bayoneta patentada. Los desarrollos más recientes incluyen los diseños de los convertidores S-300 y S-350. El convertidor S-300 es una configuración de flujo radial de tres camas con intercambiadores de calor internos, mientras que el diseño S-350 combina un convertidor S-300 con un diseño S-50 de una cama con recuperación de calor residual entre convertidores para maximizar la conversión de amoníaco.
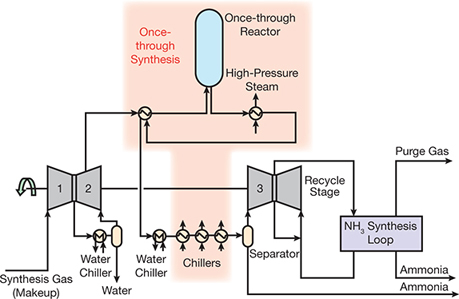
▲Figura 6., El diseño de bucle de síntesis de doble presión de ThyssenKrupp cuenta con un reactor de una sola vez entre los compresores de gas de síntesis.
ThyssenKrupp ofrece una planta convencional (Figura 6) con un diseño único de reformador secundario, una caldera de calor residual patentada, convertidores de flujo radial y un bucle de síntesis de amoníaco de doble presión. Hoy en día, se puede lograr una tasa de producción de 3.300 m.t./día utilizando el proceso de doble presión TKIS.
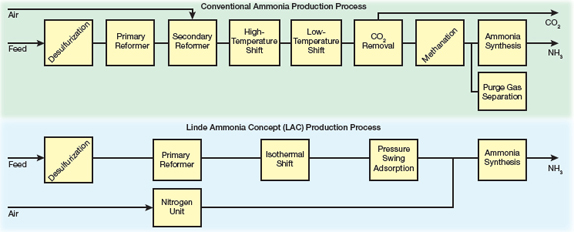
▲Figura 7., El linde Ammonia Concept (Lac) cuenta con una unidad de adsorción de oscilación de presión para la producción de hidrógeno de alta pureza y una unidad de separación de aire para la producción de nitrógeno de alta pureza.
El Linde Ammonia Concept (LAC) es un esquema de proceso tecnológico establecido con más de 25 años de experiencia operativa en plantas con capacidades desde 200 m.t./día hasta más de 1.750 m.t./día., El esquema de proceso LAC (Figura 7) reemplaza el costoso y complejo extremo frontal de una planta de amoníaco convencional con dos unidades de proceso confiables y bien probadas:
- Producción de hidrógeno de ultra alta pureza a partir de un reformador de vapor y metano con purificación PSA
- Producción de nitrógeno de ultra alta pureza por una unidad de generación de nitrógeno criogénico, también conocida como unidad de separación de aire (ASU).
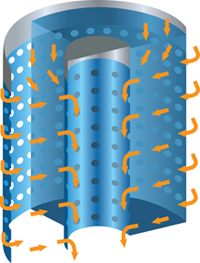
▲Figura 8., El proceso de amoniaco Casale emplea un lecho catalítico que aprovecha la tecnología axial-radial, que tiene una menor caída de presión y una mayor eficiencia que los lechos catalíticos estándar.
El diseño de la planta de Ammonia Casale tiene una tasa de producción de 2.000 m. t./día. Una de las características clave de este diseño es la tecnología axial-radial en el lecho catalítico (Figura 8). En un lecho catalizador axial-radial, la mayor parte del gas de síntesis pasa a través del lecho catalizador en una dirección radial, creando una caída de presión muy baja., El resto del gas pasa hacia abajo a través de una capa superior del catalizador en una dirección axial, eliminando la necesidad de una cubierta superior en el lecho del catalizador. La tecnología de lecho catalítico axial-radial de Casale se utiliza tanto en convertidores de cambio de alta temperatura como de baja temperatura, así como en el convertidor de síntesis.
otras tecnologías
algunos proveedores de tecnología han ofrecido reformadores calentados a gas (GHR) para la producción de amoníaco en plantas de pequeña capacidad o para aumentos de capacidad., A diferencia de las plantas de diseño convencional que utilizan un reformador primario y un reformador secundario que operan en serie, las plantas con GHR utilizan el gas de proceso caliente del reformador secundario para suministrar calor al reformador primario. Esto reduce el tamaño del reformador primario y elimina las emisiones de CO2 de la pila del reformador primario, haciendo que el proceso sea más respetuoso con el medio ambiente.,
aunque algunos productores de amoníaco abogan por la producción distribuida de amoníaco en pequeñas plantas de amoníaco, la mayoría de las empresas prefieren construir grandes instalaciones cerca de fuentes de materias primas baratas y transportar el producto por barco, ferrocarril o tubería a los consumidores.
amoníaco de carbón
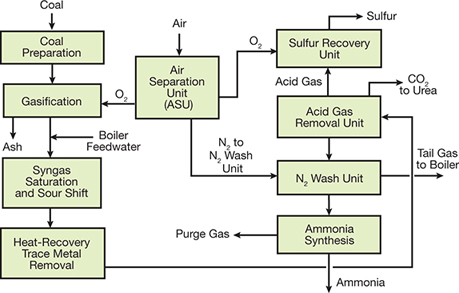
▲Figura 9. China produce la mayor parte de su amoníaco a partir del carbón.
China produce más amoníaco que cualquier otro país, y produce la mayoría de su amoníaco a partir del carbón (Figura 9).,
Las unidades de procesamiento básicas en una planta de amoníaco a base de carbón son la ASU para la separación de O2 y N2 del aire, el gasificador, la unidad de cambio de gas ácido (SGS), la unidad de eliminación de gas ácido (AGRU) y la unidad de síntesis de amoníaco. El oxígeno del ASU se alimenta al gasificador para convertir el carbón en gas de síntesis (H2, CO, CO2) y CH4. Hay muchos diseños de gasificadores, pero la mayoría de los gasificadores modernos se basan en lechos fluidizados que funcionan por encima de la presión atmosférica y tienen la capacidad de utilizar diferentes alimentaciones de carbón. Dependiendo del diseño, se pueden producir niveles de CO del 30-60% en volumen.,
después de la gasificación, se elimina cualquier partícula en el gas de síntesis y se agrega vapor a la unidad SGS. El proceso SGS normalmente utiliza un catalizador de cobalto y molibdeno (CoMo) especialmente diseñado para operar en un entorno de azufre.
después de reducir la concentración de CO en el gas de síntesis a menos de 1 vol%, el gas de síntesis se alimenta a una AGRU, donde una solución de lavado de metanol refrigerada (por ejemplo, Rectisol) elimina el CO2 y el azufre del gas de síntesis. La sobrecarga de CO2 se ventila o se alimenta a una planta de urea. La corriente de salida de azufre se alimenta a una unidad de recuperación de azufre (SRU).,
El gas de síntesis que pasa a través de la AGRU se purifica típicamente mediante uno de dos métodos:
- Una unidad de lavado de nitrógeno para eliminar el co y el CH4 residuales del gas de síntesis antes de que se alimente al bucle de síntesis
- Un sistema PSA para la eliminación de CO y CH4.
Pensamientos finales
durante los últimos 60 años, la tecnología de proceso de amoníaco ha mejorado drásticamente. Los diseños de plantas evolucionaron desde diseños de trenes múltiples, a menudo con diferentes números de trenes en el extremo frontal y el bucle de síntesis, hasta diseños de trenes individuales., La preparación del gas de síntesis en la parte frontal de la planta aumentó de la presión atmosférica a la presión de 30-50 barg. Las capacidades aumentaron de 100 m. t./día a hasta 3.300 m. t./día en un solo tren.
la eficiencia energética también ha mejorado, desde consumos muy superiores a 60 GJ/m.t. de amoníaco en plantas a base de coque a 40-50 GJ/M.t. en las primeras plantas a base de gas natural a 30-40 GJ / M.t. en las primeras plantas de un solo tren. Las plantas modernas han agregado recuperación de calor mediante la producción de vapor a presiones de hasta 125 barg tanto en la sección de preparación de gas de síntesis como en el bucle de síntesis.,
en términos de equipos de proceso, ha habido un cambio de compresores alternativos a Compresores Centrífugos. Se ha implementado un intercambiador de calor interno en el convertidor de síntesis para aumentar la conversión de H2 y N2 a NH3. Los diseñadores han aprovechado la recuperación de hidrógeno del gas de purga (en unidades como los sistemas PSA) para mejorar la producción o reducir el consumo de energía de la planta. Los diseñadores también han implementado sistemas de desulfuración de gas de alimentación caliente. Ha habido mejoras significativas en los catalizadores utilizados en el reformado, la conversión por turnos, la metanación y la síntesis de amoníaco.,
para mejorar el control y la seguridad de los procesos, los sistemas de control distribuido (DCSs) para el control avanzado de procesos, así como los sistemas instrumentados de seguridad (Siss), ahora son estándar en las plantas de amoníaco. Antes de que cualquier proceso se ponga en línea, se realizan estudios de peligro y operabilidad (HAZOP) y análisis de capa de protección (LOPAs). Los avances en simuladores de capacitación y prácticas educativas garantizan que los operadores e ingenieros puedan realizar sus tareas de manera segura y efectiva.,
estas son solo algunas de las miles de mejoras en tecnología y seguridad que se han implementado para hacer de la industria del amoníaco una de las industrias más productivas y seguras del mundo.
agradecimientos
los autores agradecen la asistencia de KBR, Thyssenkrupp Industrial Solutions, Haldor Topsøe, Linde y Casale para proporcionar literatura técnica sobre sus respectivas tecnologías de proceso.