L’ammoniac est essentiel à la fabrication d’engrais et est l’un des produits chimiques synthétiques les plus produits au monde. Cet article explore l’évolution de la production d’ammoniac et décrit les technologies de fabrication actuelles.
la plupart des gens associent l’odeur âcre de l’ammoniac (NH3) aux nettoyants ou aux sels odorants. Cependant, l’utilisation d’ammoniac dans ces deux produits ne représente qu’une petite fraction de la production mondiale totale d’ammoniac, qui était d’environ 176 millions de tonnes métriques en 2014 (1)., Pour apprécier où l’industrie et la technologie sont aujourd’hui, jetons d’abord un coup d’oeil à la façon dont nous sommes arrivés ici.
L’ammoniac est connu depuis plus de 200 ans. Joseph Priestley, un chimiste anglais, a isolé pour la première fois de l’ammoniac gazeux en 1774. Sa composition a été établie par le chimiste français Claude Louis Berthollet en 1785., En 1898, Adolph Frank et Nikodem Caro ont découvert que le N2 pouvait être fixé par du carbure de calcium pour former du cyanamide calcique, qui pourrait ensuite être hydrolysé avec de l’eau pour former de l’ammoniac (2):
CaO + 3C ↔ CaC2 + CO
CaC2 + N2 ↔ CaCN2 + C
CaCN2 + 3H2O ↔ CaCO3 + 2nh3
la production de quantités importantes d’ammoniac ne se produisent pas avant le début du 20ème siècle. Parce que ce processus nécessitait de grandes quantités d’énergie, les scientifiques ont concentré leurs efforts sur la réduction des besoins en énergie.,
le chimiste allemand Fritz Haber a réalisé certains des travaux les plus importants dans le développement de l’industrie moderne de l’ammoniac. Travailler avec un étudiant à l’Univ. de Karlsruhe, il a synthétisé l’ammoniac en laboratoire à partir de N2 et H2.
pendant ce temps, Walther Nernst, professeur de chimie physique à L’Univ. de Berlin, a mis au point un procédé pour fabriquer de l’ammoniac en faisant passer un mélange de N2 et de H2 à travers un catalyseur de fer à 1 000°C et à une pression de 75 barg. Il était capable de produire de plus grandes quantités d’ammoniac à cette pression que les expériences antérieures par Haber et d’autres à la pression atmosphérique., Cependant, Nernst a conclu que le processus n’était pas réalisable parce qu’il était difficile ou presque impossible (à l’époque) de produire de gros équipements capables de fonctionner à cette pression.
néanmoins, Haber et Nernst ont suivi la voie à haute pression pour produire de l’ammoniac au-dessus d’un catalyseur. Haber a finalement développé un procédé pour produire des quantités commerciales d’ammoniac et, en 1906, il a pu atteindre une concentration d’ammoniac de 6% dans un réacteur chargé d’un catalyseur à l’osmium., Ceci est généralement reconnu comme le tournant dans le développement d’un processus pratique pour la production d’ammoniac en quantités commerciales.
Haber s’est rendu compte que la quantité d’ammoniac formée en un seul passage dans un convertisseur était beaucoup trop faible pour présenter un intérêt commercial. Pour produire plus d’ammoniac à partir du gaz de maquillage, il a proposé un système de recyclage, et a reçu un brevet pour le concept. Haber, recycler idée changé la perception de l’ingénierie des processus statique en faveur d’une approche plus dynamique., En plus de l’équilibre de la réaction chimique, Haber a reconnu que la vitesse de réaction était un facteur déterminant. Au lieu d’un simple rendement dans un processus unique, il s’est concentré sur le rendement espace-temps dans un système avec recyclage.
BASF a acheté les brevets de Haber et a commencé le développement d’un procédé commercial. Après avoir testé plus de 2 500 catalyseurs différents, Carl Bosch, Alvin Mittasch et D’autres chimistes de BASF ont développé un catalyseur de fer promu pour la production d’ammoniac en 1910., Développer un équipement capable de résister aux températures et à la pression élevées nécessaires était une tâche encore plus difficile. Un premier réacteur en acier doux n’a duré que 80 heures avant une défaillance due à la décarbonisation. Le revêtement des réacteurs en acier doux avec du fer doux (qui n’était pas vulnérable à la décarbonisation) et l’ajout de rainures entre les deux revêtements pour libérer l’hydrogène qui s’était diffusé à travers le revêtement en fer doux ont résolu ce problème., D’autres défis majeurs comprenaient la conception d’un échangeur de chaleur pour amener le gaz d’entrée aux températures de réaction et refroidir le gaz de sortie, et la conception d’une méthode pour amener le catalyseur à la température de réaction.
la première usine commerciale d’ammoniac basée sur le procédé Haber-Bosch a été construite par BASF à Oppau, en Allemagne. L’usine a été mise en service le Septembre. 9, 1913, avec une capacité de production de 30 M. T. / jour.
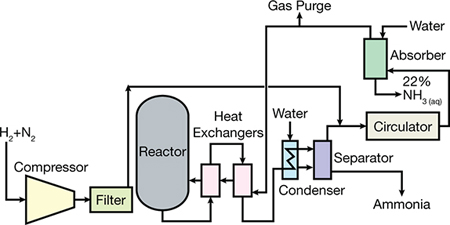
▲Figure 1. Il s’agit d’un organigramme simplifié de la première usine commerciale d’ammoniac de BASF.,
La Figure 1 est un organigramme de la première usine commerciale d’ammoniac. Le réacteur contenait un échangeur de chaleur interne en plus de ceux indiqués sur le schéma.
taux de production mondiaux
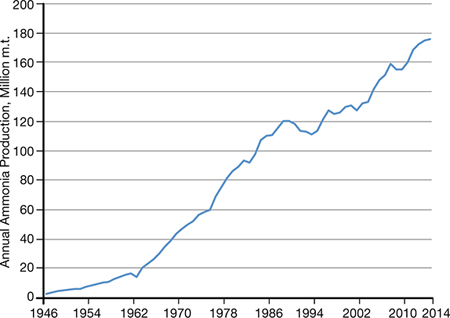
▲Figure 2. La production mondiale d’ammoniac n’a cessé d’augmenter de 1946 à 2014.
la production d’Ammoniac est devenue l’une des industries les plus importantes dans le monde. Sans le rendement des cultures rendu possible par les engrais et les produits chimiques à base d’ammoniac, la population mondiale serait d’au moins deux à trois milliards de moins qu’aujourd’hui (3)., La production d’ammoniac a augmenté régulièrement depuis 1946 (Figure 2), et on estime que la production annuelle d’ammoniac vaut plus de 100 milliards de dollars, certaines usines produisant plus de 3 000 m. T./jour de NH3.
en 1983, à l’occasion du 75e anniversaire de la fondation de L’AIChE, un groupe d’ingénieurs chimistes distingués a nommé ce qu’ils croyaient être les dix plus grandes réalisations en génie chimique au Monde (4)., Embrassant des exploits tels que les médicaments miracles, les fibres synthétiques et l’énergie atomique, la citation comprenait également la percée qui a permis la production de grandes quantités d’ammoniac dans des usines compactes à unité unique.
Au cours des dernières décennies, les ingénieurs chimistes ont réussi à créer des processus qui produisent de grandes quantités d’ammoniac à des coûts relativement bas. Aussi récemment qu’il y a 80 ans, la production annuelle totale d’ammoniac synthétisé était d’un peu plus de 300 000 m. T. Grâce aux percées du génie chimique, une usine d’ammoniac moderne peut produire plus de 750 000 m. T./an.,
environ 88% de l’ammoniac produit annuellement est consommé dans la fabrication d’engrais. Le reste va dans la production de formaldéhyde. La Chine a produit environ 32,6% de la production mondiale en 2014, tandis que la Russie, l’Inde et les États-Unis ont produit respectivement 8,1%, 7,6% et 6,4% (1). Alors que la majeure partie de la production mondiale d’ammoniac est basée sur le reformage à la vapeur du gaz naturel, des quantités importantes sont produites par la gazéification du charbon; la plupart des usines de gazéification sont situées en Chine.,
processus de production modernes
L’augmentation considérable de la demande d’ammoniac de 1950 à 1980 a nécessité des usines plus grandes et plus économes en énergie. Ces décennies ont également vu un changement dans la philosophie de conception. Jusque-là, une usine d’ammoniac était considérée comme un assemblage d’unités indépendantes, telles que la préparation de gaz, la purification de gaz, la compression de gaz et la synthèse d’ammoniac. De nouvelles innovations et une conception intégrale liaient les unités de processus de la manière la plus efficace et la plus efficiente.
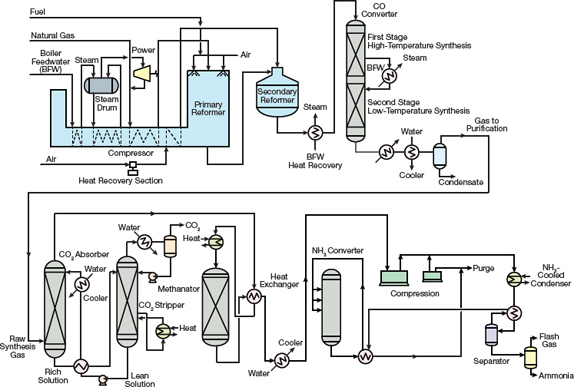
▲Figure 3., KBR a conçu l’une des premières usines d’ammoniac de grande capacité à train unique.
au milieu des années 1960, l’American Oil Co. installation d’une usine d’ammoniac à convertisseur unique conçue par M. W. Kellogg (MWK) à Texas City, au Texas, avec une capacité de 544 M. T./jour. Le concept de conception à train unique (Figure 3) était si révolutionnaire qu’il a reçu le prix Kirkpatrick Chemical Engineering Achievement Award en 1967.,
l’usine a utilisé un compresseur centrifuge à quatre caisses pour comprimer le gaz de synthèse à une pression de 152 bars, et la compression finale à une pression de fonctionnement de 324 bars s’est produite dans un compresseur alternatif. Des compresseurs centrifuges pour la boucle de synthèse et les services de réfrigération ont également été mis en œuvre, ce qui a permis de réaliser d’importantes économies.,
Les principales différences entre le procédé MWK et les procédés utilisés dans les usines d’ammoniac précédentes comprenaient:
- utilisation d’un compresseur centrifuge dans le cadre de la compression du gaz de synthèse
- maximisation de la récupération de la chaleur résiduelle du procédé
- génération de vapeur à partir de la chaleur résiduelle pour une utilisation dans les conducteurs de turbines à vapeur
- utilisation du compresseur frigorifique pour la réfrigération à vide et atmosphérique.
un schéma intégré qui équilibrait la consommation d’énergie, la production d’énergie, la taille de l’équipement et les volumes de catalyseurs a été intégré dans toute l’usine.,
la plupart des usines construites entre 1963 et 1993 avaient de grandes conceptions à train unique avec une production de gaz de synthèse à 25-35 bar et une synthèse d’ammoniac à 150-200 bar. Une autre variante par Braun (maintenant KBR) a offert de légères modifications à la conception de base. Les usines de traitement des purificateurs Braun ont utilisé un reformeur primaire ou tubulaire avec une basse température de sortie et une fuite de méthane élevée pour réduire la taille et le coût du reformeur. L’excès d’air a été ajouté au reformeur secondaire pour réduire la teneur en méthane du flux de sortie du reformeur primaire à 1-2%., L’excès d’azote et d’autres impuretés ont été éliminés en aval du méthanateur. Comme le gaz de synthèse était essentiellement exempt d’impuretés, deux convertisseurs d’ammoniac à flux axial ont été utilisés pour obtenir une conversion élevée de l’ammoniac.
certaines usines récemment construites ont un système de génération de gaz de synthèse avec un seul reformeur (pas de reformeur secondaire), un système D’adsorption modulée en pression (PSA) pour la récupération de H2 et une usine de séparation de l’air comme source de N2., Les améliorations apportées à la conception du convertisseur, telles que les lits de catalyseurs radiaux et horizontaux, les échangeurs de chaleur internes et le traitement des gaz de synthèse, ont contribué à augmenter les concentrations d’ammoniac à la sortie du convertisseur de synthèse d’environ 12% à 19-21%. Une conversion plus élevée par passage, associée à des turbines et des compresseurs plus efficaces, réduit encore la consommation d’énergie. Des solutions D’élimination du CO2 plus efficaces, telles que le carbonate de potassium et la méthyldiéthanolamine (MDEA), ont contribué à améliorer l’efficacité énergétique. La plupart des usines modernes peuvent produire de l’ammoniac avec une consommation d’énergie de 28 GJ/M. T.,
en plus des améliorations de conception, mécaniques et métallurgiques apportées pendant cette période, la pression de fonctionnement de la boucle de synthèse a été considérablement réduite. Lorsque la première usine à train unique a été construite dans les années 1960, elle contenait une boucle de synthèse à haute pression. En 1962, MWK a reçu une demande D’Imperial Chemical Industries (ICI) pour une proposition de construction d’une usine de 544 M. T./jour sur leur site de Severnside. MWK a proposé une boucle de synthèse de 152 bars au lieu d’une boucle de 324 bars.,
étant donné que l’élaboration de données cinétiques pour la réaction d’ammoniac à 152 bars prendrait plus de temps que MWK ne devait répondre à L’enquête ICI, ils ont contacté Haldor Topsøe pour appuyer leurs plans. Topsøe disposait de données couvrant toute la plage de pression intéressant MWK. En outre, ils avaient un programme informatique pour calculer la quantité de catalyseur nécessaire à la pression de service inférieure. Même si ICI a choisi Bechtel pour concevoir l’usine, MWK a pu développer un organigramme pour un 544-M. T.,/ conception de jour avec des compresseurs centrifuges et une boucle de synthèse à basse pression, que certaines personnes considèrent comme l’événement le plus important dans le développement de l’usine d’ammoniac à train unique.
Il fallait environ deux fois plus de catalyseur à 152 bar qu’à 324 bar, une augmentation qui semblait économiquement réalisable. Bien que le convertisseur aurait besoin de deux fois le volume, la pression de fonctionnement inférieure réduirait l’épaisseur requise de la coque de pression. En conséquence, le poids de métal requis pour le convertisseur plus le catalyseur est resté à peu près le même., La boucle de synthèse à basse pression a également permis l’utilisation de compresseurs centrifuges au lieu de compresseurs alternatifs. Une autre amélioration a été la récupération de la chaleur pour générer de la vapeur à haute pression pour les entraînements de turbines à vapeur.
conception des usines au 21e siècle
Au cours des premières années du 21e siècle, de nombreuses améliorations ont été apportées à la technologie des usines d’ammoniac qui permettent aux usines existantes d’augmenter leurs taux de production et à de nouvelles usines d’être construites avec des capacités de plus en plus grandes. La concurrence entre les fournisseurs de technologie est assez féroce., Trois concédants de licence technologique — KBR (Kellogg Brown and Root), Haldor Topsøe et ThyssenKrupp Industrial Solutions (TKIS) – dominent actuellement le marché. Ammoniac Casale, qui offre une conception de lit de catalyseur axial-radial, est un leader du marché dans les remaniements d’usines existantes.
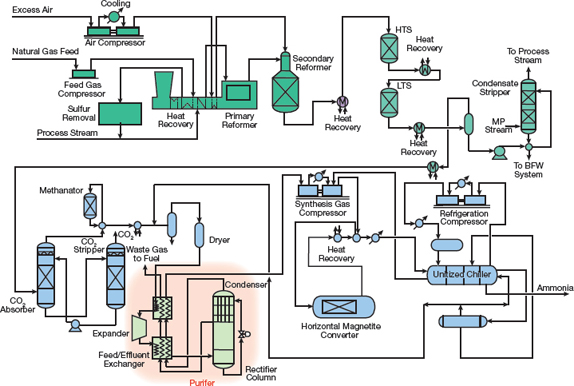
▲Figure 4. Les usines d’ammoniac modernes conçues par KBR utilisent sa conception de purificateur propriétaire.,
la plupart des usines d’ammoniac récemment conçues par KBR utilisent son procédé de purification (Figure 4), qui combine un reformage à faible gravité dans le reformeur primaire, un purificateur de lavage n2 liquide en aval du méthanateur pour éliminer les impuretés et ajuster le rapport H2:N2, une conception exclusive de chaudière à chaleur résiduelle, un
selon la configuration de l’installation, la consommation d’énergie peut être aussi faible que 28 GJ/M. T. Comme le reformeur secondaire utilise un excès d’air, le reformeur primaire peut être plus petit que dans les conceptions conventionnelles., Le purificateur cryogénique (représenté sur la Figure 4 en vert clair avec un fond orange clair), qui se compose d’un extenseur, d’un condenseur, d’un échangeur d’alimentation/effluent et d’une colonne redresseuse, élimine les impuretés telles que le CO, le CH4 et l’argon du gaz de synthèse tout en ajustant le rapport H2:N2 du La concentration d’ammoniac sortant du convertisseur horizontal à faible chute de pression est de 20 à 21%, ce qui réduit les besoins en énergie du compresseur de recyclage., KBR propose également une boucle d’ammoniac basse pression qui utilise une combinaison de catalyseur à magnétite et de son catalyseur au ruthénium exclusif.
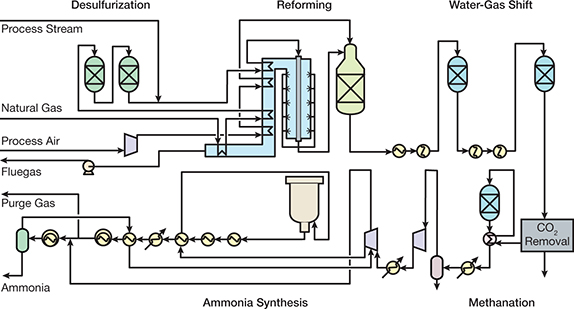
▲Figure 5. Haldor Topsøe propose une conception d’usine d’ammoniac dotée d’un reformeur à cuisson latérale exclusif dans lequel des brûleurs rayonnants fournissent de la chaleur pour la réaction de reformage.
la section de génération de gaz de synthèse (ou frontal) d’une usine conçue par Haldor Topsøe (Figure 5) est assez traditionnelle, à l’exception de son reformeur à feu latéral exclusif, qui utilise des brûleurs rayonnants pour fournir de la chaleur pour la réaction de reformage., Haldor Topsøe propose également un catalyseur de synthèse à base de fer exclusif, des convertisseurs à flux radial composés d’un, deux ou trois lits et une chaudière à chaleur résiduelle à tube à baïonnette exclusive. Les développements plus récents incluent les conceptions de convertisseurs S-300 et S-350. Le convertisseur S-300 est une configuration à flux radial à trois lits avec échangeurs de chaleur internes, tandis que la conception S-350 combine un convertisseur S-300 avec une conception à lit unique S-50 avec récupération de chaleur résiduelle entre les convertisseurs pour maximiser la conversion de l’ammoniac.
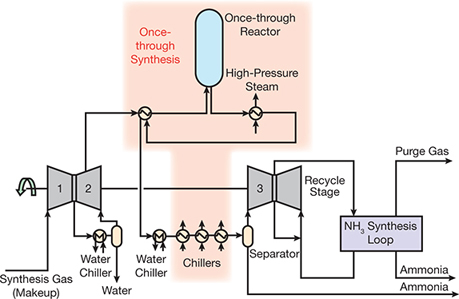
▲Figure 6., La conception de boucle de synthèse à double pression de ThyssenKrupp comporte un réacteur à passage unique entre les compresseurs de gaz de synthèse.
ThyssenKrupp propose une installation conventionnelle (Figure 6) avec une conception unique de reformeur secondaire, Une chaudière de chaleur résiduelle exclusive, des convertisseurs à flux radial et une boucle de synthèse d’ammoniac à double pression. Aujourd’hui, un taux de production de 3 300 M. T./jour peut être atteint en utilisant le procédé à double pression TKIS.
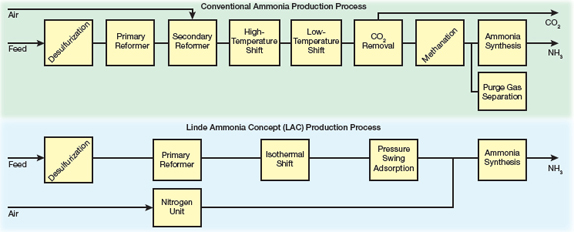
▲Figure 7., Le Linde ammoniac concept (LAC) comprend une unité d’adsorption modulée en pression pour la production d’hydrogène de haute pureté et une unité de séparation de l’air pour la production d’azote de haute pureté.
Le Linde ammoniac concept (LAC) est un système de processus technologique établi avec plus de 25 ans d’expérience d’exploitation dans des usines avec des capacités de 200 M. T. / jour à plus de 1,750 M. T. / jour., Le schéma de traitement de LAC (Figure 7) remplace l’extrémité avant coûteuse et complexe d’une usine d’ammoniac classique par deux unités de traitement fiables et éprouvées:
- production d’hydrogène ultra-pur à partir d’un reformeur vapeur-méthane avec purification de PSA
- production d’azote ultra-pur par une unité de génération d’azote cryogénique, également appelée Unité de séparation de l’air (ASU).
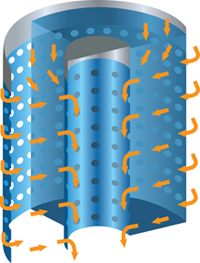
▲Figure 8., Ammoniac le processus de Casale utilise un lit de catalyseur qui exploite la technologie axiale-radiale, qui a une chute de pression plus faible et un rendement plus élevé que les lits de catalyseur standard.
La conception de L’usine D’ammoniac Casale a un taux de production de 2 000 m. T. / jour. L’une des principales caractéristiques de cette conception est la technologie axiale-radiale dans le lit de catalyseur (Figure 8). Dans un lit de catalyseur axial-radial, la majeure partie du gaz de synthèse traverse le lit de catalyseur dans une direction radiale, créant une chute de pression très faible., Le reste du gaz passe à travers une couche de catalyseur dans la direction axiale, éliminant le besoin d’un couvercle sur le lit de catalyseur. La technologie de lit de catalyseur axial-radial de Casale est utilisée dans les convertisseurs de décalage à haute température et à basse température, ainsi que dans le convertisseur de synthèse.
autres technologies
certains fournisseurs de technologie ont offert des reformeurs chauffés au gaz (GHR) pour la production d’ammoniac dans des usines de petite capacité ou pour l’augmentation de la capacité., Contrairement aux usines de conception conventionnelle qui utilisent un reformeur primaire et un reformeur secondaire fonctionnant en série, les usines avec GHR utilisent le gaz de procédé chaud du reformeur secondaire pour fournir de la chaleur au reformeur primaire. Cela réduit la taille du reformeur primaire et élimine les émissions de CO2 de la pile du reformeur primaire, ce qui rend le processus plus respectueux de l’environnement.,
même si certains producteurs d’ammoniac plaident pour une production distribuée d’ammoniac dans de petites usines d’ammoniac, la plupart des entreprises préfèrent construire de grandes installations à proximité de sources de matières premières bon marché et transporter le produit par bateau, rail ou pipeline vers les consommateurs.
l’Ammoniac à partir de charbon
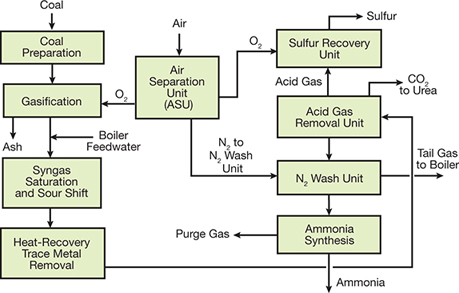
▲Figure 9. La Chine produit la majeure partie de son ammoniac à partir du charbon.
La Chine produit plus d’ammoniac que tout autre pays et produit la majorité de son ammoniac à partir du charbon (Figure 9).,
Les unités de traitement de base dans une usine d’ammoniac à base de charbon sont L’ASU pour la séparation de L’O2 et du N2 de l’air, le gazéificateur, l’Unité de déplacement de gaz acide (SGS), L’unité D’élimination des gaz acides (AGRU) et l’Unité de synthèse d’ammoniac. L’oxygène de L’ASU est introduit dans le gazéificateur pour convertir le charbon en gaz de synthèse (H2, CO, CO2) et CH4. Il existe de nombreux modèles de gazéificateurs, mais la plupart des gazéificateurs modernes sont basés sur des lits fluidisés qui fonctionnent au-dessus de la pression atmosphérique et ont la capacité d’utiliser différents flux de charbon. Selon la conception, des niveaux de CO de 30 à 60% en volume peuvent être produits.,
Après la gazéification, toute matière particulaire dans le gaz de synthèse est éliminée et de la vapeur est ajoutée à l’unité SGS. Le procédé SGS utilise généralement un catalyseur au cobalt et au molybdène (CoMo) spécialement conçu pour fonctionner dans un environnement soufré.
Après avoir réduit la concentration de CO dans le gaz de synthèse à moins de 1% vol, le gaz de synthèse est introduit dans un AGRU, où une solution réfrigérée de lavage au méthanol (par exemple, le Rectisol) élimine le CO2 et le soufre du gaz de synthèse. Le CO2 au-dessus est soit évacué, soit acheminé vers une usine d’urée. Le flux de sortie de soufre est envoyé à une unité de récupération de soufre (SRU).,
Le gaz de synthèse qui traverse L’AGRU est généralement purifié par l’une des deux méthodes suivantes:
- Une unité de lavage à l’azote pour éliminer le co et le CH4 résiduels du gaz de synthèse avant qu’il ne soit introduit dans la boucle de synthèse
- Un système PSA pour l’élimination du CO et du CH4.
réflexions finales
Au cours des 60 dernières années, la technologie de traitement de l’ammoniac s’est considérablement améliorée. Les plans d’installation ont évolué de la conception de plusieurs trains, souvent avec un nombre différent de trains dans la boucle avant et la boucle de synthèse, à la conception d’un seul train., La préparation des gaz de synthèse à l’avant de l’usine est passée de la pression atmosphérique à une pression de 30 à 50 barg. Les capacités sont passées de 100 M. T./jour à 3 300 m. t./jour dans un seul train.
l’efficacité énergétique s’est également améliorée, passant de consommations bien supérieures à 60 GJ/M. T. d’ammoniac dans les usines à base de coke à 40-50 GJ/M. T. dans les premières usines à base de gaz naturel à 30-40 GJ/M. T. dans les premières usines à train unique. Les usines modernes ont ajouté la récupération de chaleur par la production de vapeur à des pressions aussi élevées que 125 barg dans la section de préparation du gaz de synthèse et la boucle de synthèse.,
en ce qui concerne l’équipement de traitement, il y a eu un passage des compresseurs alternatifs aux compresseurs centrifuges. Un échangeur de chaleur interne a été mis en œuvre dans le convertisseur de synthèse pour augmenter la conversion de H2 et de N2 en NH3. Les concepteurs ont exploité la récupération d’hydrogène à partir de gaz de purge (dans des unités telles que les systèmes PSA) pour améliorer la production ou réduire la consommation d’énergie de l’usine. Les concepteurs ont également mis en œuvre des systèmes de désulfuration des gaz d’alimentation à chaud. Il y a eu des améliorations significatives dans les catalyseurs utilisés dans le reformage, la conversion par déplacement, la méthanation et la synthèse de l’ammoniac.,
pour améliorer le contrôle et la sécurité des processus, les systèmes de contrôle distribué (DCSs) pour le contrôle avancé des processus, ainsi que les systèmes instrumentés pour la sécurité (SISs), sont maintenant standard dans les usines d’ammoniac. Avant la mise en ligne de tout processus, des études de danger et d’opérabilité (HAZOP) et des analyses de couche de protection (LOPAs) sont effectuées. Les progrès réalisés dans les simulateurs de formation et les pratiques d’éducation garantissent que les opérateurs et les ingénieurs peuvent s’acquitter de leurs tâches de manière sûre et efficace.,
Ce ne sont là que quelques-unes des milliers d’améliorations technologiques et de sécurité qui ont été mises en œuvre pour faire de l’industrie de l’ammoniac l’une des industries les plus productives et les plus sûres au monde.
Remerciements
Les auteurs reconnaissent L’assistance de KBR, ThyssenKrupp Industrial Solutions, Haldor Topsøe, Linde et Casale pour leur documentation technique sur leurs technologies de procédé respectives.