ammoniak är kritisk vid tillverkning av gödselmedel och är en av världens största syntetiska kemikalier. Denna artikel utforskar utvecklingen av ammoniakproduktionen och beskriver den nuvarande tillverkningstekniken.
de flesta människor associerar den skarpa lukten av ammoniak (NH3) med rengöringsmedel eller luktsalter. Användningen av ammoniak i dessa två produkter utgör emellertid bara en liten del av den totala globala ammoniakproduktionen, som var cirka 176 miljoner ton 2014 (1)., För att uppskatta var industrin och tekniken är idag, låt oss först ta en titt på hur vi kom hit.
ammoniak har varit känt i mer än 200 år. Joseph Priestley, en engelsk kemist, isolerade först gasformig ammoniak år 1774. Dess sammansättning fastställdes av den franska kemisten Claude Louis Berthollet 1785., År 1898 fann Adolph Frank och Nikodem Caro att N2 kunde fastställas med Kalciumkarbid för att bilda kalciumcyanamid, som sedan kunde hydrolyseras med vatten för att bilda ammoniak (2):
cao + 3C CaC2 + CO
CaC2 + N2 Cacn2 + c
cacn2 + 3H2O CaCo3 + 2NH3
produktionen av betydande mängder ammoniak med hjälp av cyanamidprocessen gjorde inte förekommer fram till början av 1900-talet. Eftersom denna process krävde stora mängder energi fokuserade forskarna sina ansträngningar på att minska energibehoven.,
tysk kemist Fritz Haber utförde några av de viktigaste arbetet i utvecklingen av den moderna ammoniakindustrin. Arbeta med en student på Univ. i Karlsruhe syntetiserade han ammoniak i laboratoriet från N2 och H2.
under Tiden, Walther Nernst, professor i fysikalisk kemi vid Univ. av Berlin, utvecklat en process för att göra ammoniak genom att passera en blandning av N2 och H2 över en järnkatalysator vid 1,000°C och 75 barg tryck. Han kunde producera större mängder ammoniak vid detta tryck än tidigare experiment av Haber och andra vid atmosfärstryck., Nernst drog dock slutsatsen att processen inte var genomförbar eftersom det var svårt eller nästan omöjligt (vid den tiden) att producera stor utrustning som kunde fungera vid det trycket.
trots detta fortsatte både Haber och Nernst högtrycksvägen för att producera ammoniak över en katalysator. Haber utvecklade slutligen en process för att producera kommersiella mängder ammoniak, och 1906 kunde han uppnå en 6% ammoniakkoncentration i en reaktor laddad med en osmiumkatalysator., Detta är allmänt erkänt som vändpunkten i utvecklingen av en praktisk process för produktion av ammoniak i kommersiella kvantiteter.
Haber insåg att mängden ammoniak som bildas i en enda passage genom en omvandlare var alldeles för låg för att vara av kommersiellt intresse. För att producera mer ammoniak från sminkgasen föreslog han ett återvinningssystem och fick ett patent för konceptet. Habers recycle-idé förändrade uppfattningen av processteknik som statisk till förmån för ett mer dynamiskt tillvägagångssätt., Förutom den kemiska reaktionsjämvikten erkände Haber att reaktionshastigheten var en avgörande faktor. I stället för enkel avkastning i en genomgångsprocess koncentrerade han sig på rymdtidsutbyte i ett system med återvinning.
BASF köpte Habers patent och började utveckla en kommersiell process. Efter att ha testat mer än 2500 olika katalysatorer utvecklade Carl Bosch, Alvin Mittasch och andra BASF-kemister en främjad järnkatalysator för produktion av ammoniak 1910., Att utveckla utrustning som kunde motstå de nödvändiga höga temperaturerna och trycket var en ännu svårare uppgift. En tidig mild stålreaktor varade bara 80 timmar före misslyckande på grund av dekarbonisering. Foder milda stålreaktorer med mjukt järn (som inte var sårbart för dekarbonisering) och lägga spår mellan de två liners för att frigöra väte som hade spridit sig genom den mjuka järn liner löst detta problem., Andra stora utmaningar var att utforma en värmeväxlare för att få inloppsgasen till reaktionstemperaturer och kyla utloppsgasen och utforma en metod för att få katalysatorn till reaktionstemperaturen.
den första kommersiella ammoniakanläggningen baserad på Haber-Bosch-processen byggdes av BASF i Oppau, Tyskland. Växten gick på strömmen på Sept. 9, 1913, med en produktionskapacitet på 30 m. t. / dag.
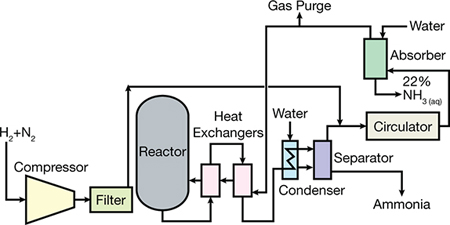
figur 1. Detta är ett förenklat flödesblad från BASF: s första kommersiella ammoniakanläggning.,
Figur 1 är ett flödesblad från den första kommersiella ammoniakanläggningen. Reaktorn innehöll en intern värmeväxlare utöver de som visas på schemat.
globala produktionsnivåer
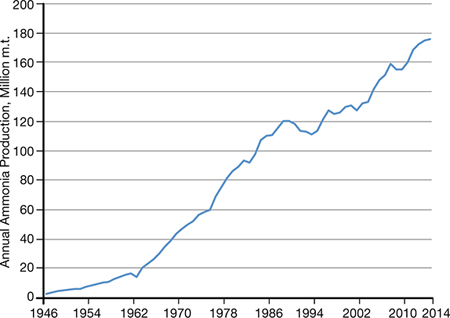
figur 2. Den globala ammoniakproduktionen har stadigt ökat från 1946 till 2014.
Ammoniakproduktionen har blivit en av världens viktigaste industrier. Utan skördeavkastningen som möjliggjorts av ammoniakbaserade gödningsmedel och kemikalier skulle den globala befolkningen vara minst två till tre miljarder mindre än idag (3)., Ammoniakproduktionen har ökat stadigt sedan 1946 (Figur 2), och det uppskattas att den årliga produktionen av ammoniak är värd mer än $100 miljarder, med vissa växter som producerar mer än 3000 m.t./dag NH3.
1983, i samband med 75-årsdagen av Aiches grundande, namngav en blå bandpanel av framstående kemiska ingenjörer vad de trodde var världens tio största kemitekniska prestationer (4)., Omfamna sådana bedrifter som wonder drugs, syntetfibrer, och atomenergi, citatet ingår också genombrott som tillät produktion av stora mängder ammoniak i kompakta, en enda enhet växter.
under de senaste decennierna har kemiska ingenjörer lyckats skapa processer som gör stora mängder ammoniak till relativt låga kostnader. Så sent som för 80 år sedan var den totala årliga produktionen av syntetiserad ammoniak drygt 300 000 m. t. tack vare kemiska tekniska genombrott kan en modern ammoniakanläggning producera mer än 750.000 m. t./yr.,
cirka 88% ammoniak som tillverkas årligen förbrukas vid tillverkning av gödselmedel. Merparten av resten går in i produktionen av formaldehyd. Kina producerade cirka 32,6% av den globala produktionen 2014, medan Ryssland, Indien och USA producerade 8,1%, 7,6% respektive 6,4% (1). Medan större delen av den globala produktionen av ammoniak är baserad på ångreformering av naturgas, produceras betydande kvantiteter genom kolförgasning.de flesta av förgasningsanläggningarna är belägna i Kina.,
moderna produktionsprocesser
den enorma ökningen av ammoniakefterfrågan från 1950 till 1980 krävde större, mer energieffektiva anläggningar. Dessa årtionden såg också en förändring i designfilosofi. Fram till den tiden betraktades en ammoniakanläggning som en sammansättning av orelaterade enheter, såsom gasberedning, gasrening, gaskompression och ammoniaksyntes. Nya innovationer och en integrerad design bundna processenheter tillsammans på de mest effektiva och effektiva sätt.
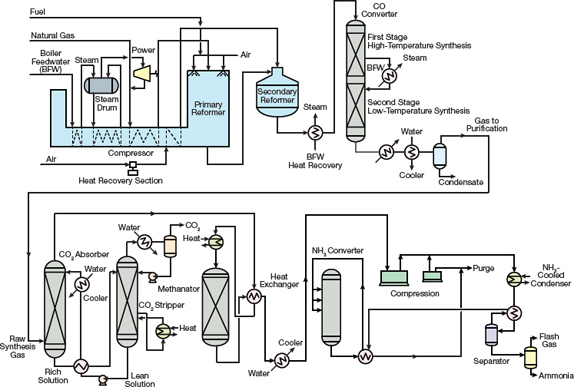
figur 3., KBR utformade en av de första enkeltåg, stor kapacitet ammoniak växter.
i mitten av 1960-talet, American Oil Co. installerade en enkelomvandlare ammoniakanläggning konstruerad av M. W. Kellogg (MWK) i Texas City, TX, med en kapacitet på 544 m.t./dag. Det enda tågdesignkonceptet (Figur 3) var så revolutionerande att det fick Kirkpatrick Chemical Engineering Achievement Award 1967.,
anläggningen använde en fyrfallscentrifugalkompressor för att komprimera syngasen till ett tryck på 152 bar, och slutlig kompression till ett arbetstryck på 324 bar inträffade i en fram-och återgående kompressor. Centrifugalkompressorer för syntesslinga-och kyltjänster genomfördes också, vilket gav betydande kostnadsbesparingar.,
de viktigaste skillnaderna mellan MWK-processen och de processer som används i tidigare ammoniakanläggningar inkluderade:
- med hjälp av en centrifugalkompressor som en del av syntesen gaskompression
- maximera återvinningen av spillvärme från processen
- generera ånga från spillvärme för användning i ångturbindrivrutiner
- med hjälp av kylkompressorn för rundown och atmosfärisk kylning.
ett integrerat system som balanserade energiförbrukning, energiproduktion, utrustningsstorlek och katalysatorvolymer införlivades i hela anläggningen.,
de flesta anläggningar som byggdes mellan 1963 och 1993 hade stora entågsdesigner med syntesgasproduktion vid 25-35 bar och ammoniaksyntes vid 150-200 bar. En annan variant av Braun (nu KBR) erbjöd små ändringar av den grundläggande designen. De Braun luftrenare processanläggningar utnyttjade en primär eller tubulär reformator med en låg utloppstemperatur och hög metan läckage för att minska storleken och kostnaden för reformatorn. Överskottsluft tillsattes till den sekundära reformatorn för att minska metanhalten i den primära reformatorutgången till 1-2%., Överskott av kväve och andra föroreningar avlägsnades nedströms metanatorn. Eftersom syntesgasen i huvudsak var fri från föroreningar, användes två axialflödes ammoniakomvandlare för att uppnå en hög ammoniakomvandling.
vissa nybyggda anläggningar har ett syntesgasproduktionssystem med endast en reformator (ingen sekundär reformator), ett system för adsorption av tryck swing (PSA) för återvinning av H2 och en anläggning för luftseparation som källa till N2., Förbättringar i omvandlardesign, såsom radiella och horisontella katalysatorbäddar, interna värmeväxlare och syntesgasbehandling, bidrog till att öka ammoniakkoncentrationerna som lämnar syntesomvandlaren från cirka 12% till 19-21%. En högre omvandling per pass, tillsammans med mer effektiva turbiner och kompressorer, ytterligare minskad energiförbrukning. Effektivare lösningar för KOLDIOXIDAVLÄGSNANDE, såsom kaliumkarbonat och metyldietanolamin (MDEA), har bidragit till förbättrad energieffektivitet. De flesta moderna växter kan producera ammoniak med en energiförbrukning på 28 gj / m.t.,
förutom de konstruktions -, mekaniska och metallurgiska förbättringar som gjorts under denna tid reducerades arbetstrycket i syntesslingan signifikant. När den första entågsanläggningen byggdes på 1960-talet innehöll den en högtryckssyntesslinga. 1962, MYR fick en förfrågan från Imperial Chemical Industries (ICI) för ett förslag om att bygga en 544-m.t./dag anläggningen på deras Severnside webbplats. MWK föreslog en 152-bar syntesslinga istället för en 324-bar slinga.,
eftersom utvecklingen av kinetiska data för ammoniakreaktionen vid 152 bar skulle ta mer tid än MWK var tvungen att svara på ICI-undersökningen kontaktade de Haldor Topsøe för att stödja sina planer. Topsøe hade uppgifter som täcker hela tryckområdet av intresse för MWK. Dessutom hade de ett datorprogram för beräkning av mängden katalysator som krävdes vid det lägre driftstrycket. Även om ici valde Bechtel för att designa anläggningen kunde MWK utveckla ett flödesblad för en 544-m. t.,/ dag design med centrifugalkompressorer och en lågtrycks syntesslinga, som vissa människor anser den enskilt viktigaste händelsen i utvecklingen av enkeltågs ammoniakanläggning.
ungefär dubbelt så mycket katalysator krävdes vid 152 bar som vid 324 bar, en ökning som verkade ekonomiskt genomförbar. Även om omvandlaren skulle behöva två gånger volymen, skulle det lägre arbetstrycket minska den erforderliga tjockleken på tryckskalet. Som ett resultat förblev vikten av metall som krävs för omvandlaren plus katalysatorn ungefär densamma., Den lägre trycksyntesslingan möjliggjorde också användning av centrifugalkompressorer istället för fram-och återgående kompressorer. En annan förbättring var att återhämta värme för att generera högtrycksånga för ångturbinenheter.
plant designs in the 21st century
under de första åren av 2000-talet gjordes många förbättringar inom ammoniakfabriksteknik som gör det möjligt för befintliga anläggningar att öka produktionstakten och nya anläggningar att byggas med större och större kapacitet. Konkurrensen mellan teknikleverantörer är ganska hård., Tre teknik licensgivare — KBR (Kellogg Brown och Rot), Haldor Topsøe, och ThyssenKrupp Industriella Lösningar (TKIS) — för närvarande dominerar marknaden. Ammoniak Casale, som erbjuder en axiell-radiell katalysator säng design, är marknadsledande inom ombyggnader av befintliga anläggningar.
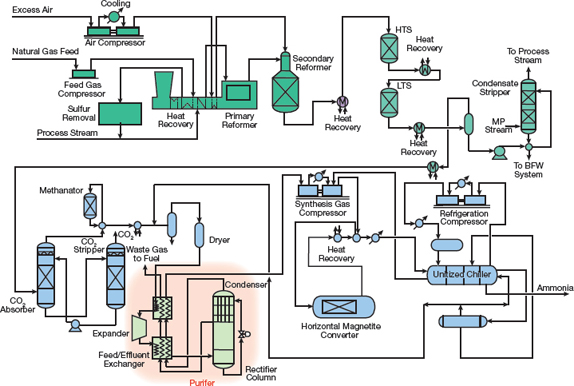
figur 4. Moderna ammoniakanläggningar designade av KBR använder sin egenutvecklade luftrenare design.,
de flesta av ammoniakanläggningarna som nyligen konstruerats av KBR använder sin reningsprocess (Figur 4), som kombinerar låggradig reformering i den primära reformatorn, en flytande N2-tvättrenare nedströms metanatorn för att avlägsna föroreningar och justera H2:N2-förhållandet, en proprietär spillvärmepannadesign, en unitiserad kylaggregat och en horisontell ammoniaksyntesomvandlare.
beroende på anläggningens konfiguration kan energiförbrukningen vara så låg som 28 GJ/m.t. eftersom den sekundära reformatorn använder överskottsluft kan den primära reformatorn vara mindre än i konventionella konstruktioner., Den kryogena luftrenaren (visas i Figur 4 i ljusgrön med en ljusorange bakgrund), som består av en expanderare, kondensor, foder/effluentväxlare och likriktarkolonn, avlägsnar föroreningar som CO, CH4 och argon från syntesgasen medan du justerar H2:N2-förhållandet mellan sminkgasen i ammoniakslingan till optimal nivå. Ammoniakkoncentrationen som lämnar lågtrycksdroppets horisontella omvandlare är 20-21%, vilket minskar energikraven för återvinningskompressorn., KBR erbjuder också en lågtrycks ammoniakslinga som använder en kombination av magnetitkatalysator och dess proprietära rutenium-katalysator.
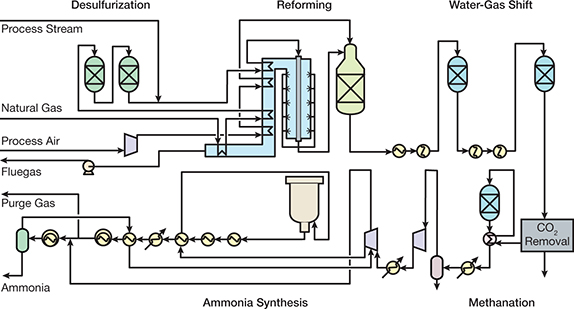
figur 5. Haldor Topsøe erbjuder en ammoniakfabrik design som har en egenutvecklad sidodriven reformator där strålningsbrännare levererar värme för reformeringsreaktionen.
syngasgenerationssektionen (eller främre änden) av en Haldor Topsøe-konstruerad anläggning (Figur 5) är ganska traditionell med undantag för dess proprietära sidodrivna reformator, som använder strålningsbrännare för att leverera värme för reformeringsreaktionen., Haldor Topsøe erbjuder också en egen järnbaserad synteskatalysator, radialflödesomvandlare bestående av en, två eller tre bäddar, och en egen bajonett-rör spillvärmepanna. Den senaste utvecklingen inkluderar S-300 och S-350 converter design. S-300-omvandlaren är en trebädds radialflödeskonfiguration med interna värmeväxlare, medan S-350-designen kombinerar en S-300-omvandlare med en S-50-enkelbäddsdesign med avfallsvärmeåtervinning mellan omvandlare för att maximera ammoniakkonvertering.
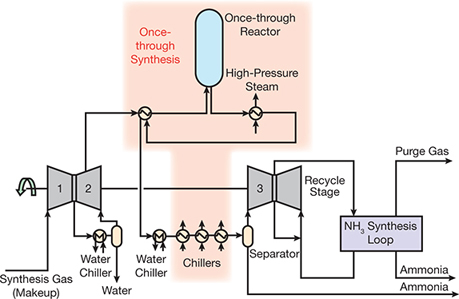
figur 6., Thyssenkrupps design av syntesslinga med dubbla tryck har en genomgående reaktor mellan syngaskompressorer.
ThyssenKrupp erbjuder en konventionell anläggning (Figur 6) med en unik sekundär reformator design, en proprietär spillvärmepanna, radialflödesomvandlare och en dubbeltrycks ammoniaksyntesslinga. Idag kan en produktionshastighet på 3,300 m.t./dag uppnås med hjälp av TKIs dual-pressure-processen.
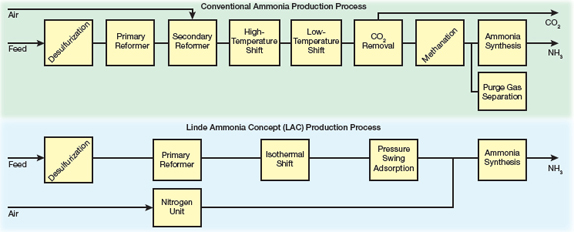
figur 7., Linde Ammonia Concept (LAC) har en adsorptionsenhet för högrenhetsväteproduktion och en luftsepareringsenhet för kväveproduktion med hög renhet.
Linde Ammonia Concept (LAC) är ett etablerat teknikprocesssystem med över 25 års driftserfarenhet i anläggningar med kapacitet från 200 m.t./dag till över 1,750 m.t./dag., LAC-processchemat (Figur 7) ersätter den kostsamma och komplexa främre änden av en konventionell ammoniakanläggning med två väl beprövade, tillförlitliga processenheter:
- produktion av ultrahög renhetsväte från en ångmetanreformer med PSA-rening
- produktion av extremt hög renhetskväve med en kryogen kvävegenereringsenhet, även känd som en luftsepareringsenhet (ASU).
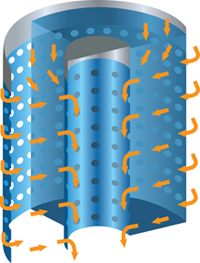
figur 8., Ammoniak Casale process använder en katalysator säng som utnyttjar axiell-radiell teknik, som har en lägre tryckfall och högre effektivitet än standard katalysator sängar.
Ammonia Casale s plant design har en produktionshastighet på 2,000 m.t. / dag. En av de viktigaste funktionerna i denna design är axiell-radiell teknik i katalysatorbädden (figur 8). I en axiell-radiell katalysatorbädd passerar det mesta av syntesgasen genom katalysatorbädden i radiell riktning, vilket skapar ett mycket lågt tryckfall., Resten av gasen passerar ner genom ett övre lager av katalysator i axiell riktning, vilket eliminerar behovet av ett topplock på katalysatorbädden. Casale axial-radial catalyst säng teknik används i både hög temperatur och låg temperatur Skift omvandlare, liksom i syntesomvandlaren.
annan teknik
vissa teknikleverantörer har erbjudit gasuppvärmda reformatorer (ghr) för produktion av ammoniak i småkapacitetsanläggningar eller för kapacitetsökningar., Till skillnad från konventionellt utformade växter som använder en primär reformator och sekundär reformator som arbetar i Serie, använder växter med GHRs den heta processgasen från den sekundära reformatorn för att leverera värme till den primära reformatorn. Detta minskar storleken på den primära reformatorn och eliminerar koldioxidutsläppen från den primära reformatorstapeln, vilket gör processen mer miljövänlig.,
även om vissa ammoniakproducenter förespråkar distribuerad produktion av ammoniak i små ammoniakanläggningar, föredrar de flesta företag att bygga stora anläggningar nära billiga råvaror och transportera produkten med fartyg, järnväg eller rörledning till konsumenterna.
ammoniak från kol
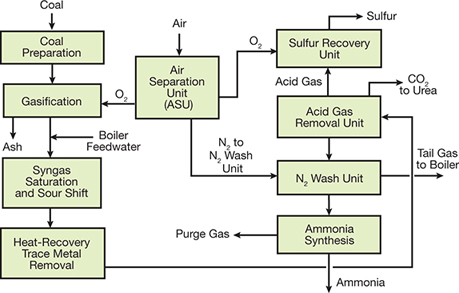
figur 9. Kina producerar det mesta av sin ammoniak från kol.
Kina producerar mer ammoniak än något annat land och producerar merparten av sin ammoniak från kol (Figur 9).,
de grundläggande bearbetningsenheterna i en kolbaserad ammoniakanläggning är ASU för separation av O2 och N2 från luft, förgasaren, sour gas shift-enheten (SGS), acid gas removal unit (AGRU) och ammoniaksyntesenheten. Syre från ASU matas till förgasaren för att omvandla kol till syntesgas (H2, CO, CO2) och CH4. Det finns många förgasare mönster, men de flesta moderna förgasare är baserade på fluidiserade sängar som fungerar över atmosfärstryck och har förmågan att utnyttja olika kol foder. Beroende på designen kan CO-nivåer på 30-60 volymprocent produceras.,
efter förgasning avlägsnas partiklar i syntesgasen och ånga tillsätts till SGS-enheten. SGS-processen använder typiskt en kobolt och molybden (CoMo) katalysator speciellt utformad för drift i en svavelmiljö.
efter en minskning av co-koncentrationen i syntesgasen till mindre än 1 vol% matas syngasen till en AGRU, där en kyld metanolskrubbningslösning (t.ex. Rektisol) avlägsnar CO2 och svavel från syntesgasen. CO2 overhead antingen ventileras eller matas till en urea anläggning. Svavelutloppsströmmen matas till en svavelåtervinningsenhet (SRU).,
Syngas som passerar genom AGRU renas vanligtvis med en av två metoder:
- en kvävetvättenhet för att avlägsna kvarvarande CO och CH4 från syngasen innan den matas till syntesslingan
- ett PSA-system för CO och CH4-borttagning.
avslutande tankar
under de senaste 60 åren har ammoniakprocesstekniken förbättrats drastiskt. Plant layouter utvecklats från Multi-train mönster, ofta med olika antal tåg i den främre änden och syntes slinga, till entåg mönster., Syntesgasberedning i växtens främre ände ökade från atmosfärstryck till 30-50 bargtryck. Kapaciteten ökade från 100 m. t. / dag till så mycket som 3,300 m. t. / dag i ett enda tåg.
energieffektiviteten har också förbättrats – från förbrukning långt över 60 gj / m. t. av ammoniak i koks-baserade anläggningar till 40-50 gj / m.t. i de första naturgasbaserade anläggningarna till 30-40 gj / m.t. i de första enkeltågsanläggningarna. Moderna anläggningar har tillsatt Värmeåtervinning genom ångproduktion vid tryck så högt som 125 barg i både syngasberedningssektionen och syntesslingan.,
När det gäller processutrustning har det skett en övergång från kolvkompressorer till centrifugalkompressorer. En intern värmeväxlare har implementerats i syntesomvandlaren för att öka omvandlingen av H2 och N2 till NH3. Designers har utnyttjat vätgasåtervinning från utrensningsgas (i enheter som PSA-system) för att öka produktionen eller minska anläggningens energiförbrukning. Designers har också genomfört varmt foder gas avsvavling system. Det har skett betydande förbättringar i katalysatorerna som används vid reformering, skiftomvandling, metanering och ammoniaksyntes.,
för att förbättra processkontroll och säkerhet är distribuerade styrsystem (DCSs) för avancerad processkontroll, samt säkerhetsinstrumenterade system (SISs), nu standard i ammoniakanläggningar. Innan någon process går online utförs hazard and operability (HAZOP) studier och layer of protection analyses (LOPAs). Framsteg i utbildningssimulatorer och utbildningspraxis säkerställer att operatörer och ingenjörer kan utföra sina uppgifter på ett säkert och effektivt sätt.,
det här är bara några av de tusentals förbättringar inom teknik och säkerhet som har genomförts för att göra ammoniakindustrin till en av världens mest produktiva och säkra industrier.
bekräftelser
författarna erkänner hjälp av KBR, ThyssenKrupp industriella lösningar, Haldor Topsøe, Linde och Casale för att tillhandahålla teknisk litteratur om deras respektive processteknik.