amoniak ma kluczowe znaczenie w produkcji nawozów i jest jednym z największych syntetycznych chemikaliów produkowanych na świecie. W tym artykule omówiono ewolucję produkcji amoniaku i opisano obecne technologie wytwarzania.
większość ludzi kojarzy ostry zapach amoniaku (NH3) ze środkami czyszczącymi lub pachnącymi solami. Wykorzystanie amoniaku w tych dwóch produktach stanowi jednak jedynie niewielki ułamek całkowitej światowej produkcji amoniaku, która w 2014 r.wynosiła około 176 milionów ton metrycznych (1)., Aby docenić, gdzie obecnie znajduje się przemysł i technologia, najpierw przyjrzyjmy się, jak się tu znaleźliśmy.
amoniak jest znany od ponad 200 lat. Joseph Priestley – angielski chemik, pierwszy wyizolowany gazowy amoniak w 1774 roku. Jego skład odkrył francuski chemik Claude Louis Berthollet w 1785 roku., W 1898 roku Adolph Frank i Nikodem Caro odkryli, że N2 może być utrwalany przez Węglik wapnia w celu utworzenia cyjanamidu wapnia, który następnie może być hydrolizowany wodą w celu utworzenia amoniaku (2):
Cao + 3C ↔ CaC2 + CO
CaC2 + N2 ↔ CaCN2 + C
CaCN2 + 3H2O ↔ CaCO3 + 2nh3
produkcja znacznych ilości amoniaku przy użyciu procesu cyjanamidowego nie występuje do początku XX wieku. Ponieważ proces ten wymagał dużych ilości energii, naukowcy skoncentrowali swoje wysiłki na zmniejszeniu zapotrzebowania na energię.,
niemiecki chemik Fritz Haber wykonał jedne z najważniejszych prac w rozwoju nowoczesnego przemysłu amoniakalnego. Praca ze studentem Univ. w Karlsruhe zsyntetyzował amoniak w laboratorium z N2 i H2.
tymczasem Walther Nernst, profesor chemii fizycznej na Univ. w Berlinie opracowano proces wytwarzania amoniaku poprzez przepuszczenie mieszaniny N2 i H2 przez katalizator żelazny w temperaturze 1000°C i ciśnieniu 75 barg. Był w stanie wyprodukować większe ilości amoniaku pod tym ciśnieniem niż wcześniejsze eksperymenty Habera i innych pod ciśnieniem atmosferycznym., Nernst stwierdził jednak, że proces ten nie jest wykonalny, ponieważ produkcja dużych urządzeń zdolnych do pracy pod takim ciśnieniem była trudna lub prawie niemożliwa (w tamtym czasie).
niemniej jednak zarówno Haber, jak i Nernst kontynuowali drogę wysokociśnieniową do produkcji amoniaku nad katalizatorem. Haber ostatecznie opracował proces produkcji komercyjnych ilości amoniaku i w 1906 roku był w stanie osiągnąć 6% stężenie amoniaku w reaktorze załadowanym katalizatorem osmu., Jest to ogólnie uznawane za punkt zwrotny w rozwoju praktycznego procesu produkcji amoniaku w ilościach komercyjnych.
Haber zdał sobie sprawę, że ilość amoniaku powstającego w jednym przejściu przez konwerter była zbyt niska, aby mogła być przedmiotem zainteresowania handlowego. Aby wyprodukować więcej amoniaku z gazu do makijażu, zaproponował system recyklingu i otrzymał patent na tę koncepcję. Koncepcja recyklingu Habera zmieniła postrzeganie inżynierii procesowej jako statycznej na rzecz bardziej dynamicznego podejścia., Oprócz równowagi reakcji chemicznych, Haber uznał, że szybkość reakcji jest czynnikiem decydującym. Zamiast prostej wydajności w jednorazowym procesie, skoncentrował się na wydajności czasoprzestrzennej w systemie z recyklingiem.
BASF zakupił patenty Habera i rozpoczął rozwój procesu komercyjnego. Po przetestowaniu ponad 2500 różnych katalizatorów, Carl Bosch, Alvin Mittasch i inni chemicy BASF opracowali promowany katalizator żelaza do produkcji amoniaku w 1910 roku., Jeszcze trudniejszym zadaniem było opracowanie sprzętu, który mógłby wytrzymać niezbędne wysokie temperatury i ciśnienie. Wczesny reaktor ze stali miękkiej trwał tylko 80 godzin przed awarią z powodu dekarbonizacji. Wyłożenie reaktorów ze stali miękkiej miękkim żelazem (które nie było podatne na dekarbonizację) i dodanie rowków między dwoma wkładkami w celu uwolnienia wodoru, który rozproszył się przez miękką wkładkę żelazną rozwiązało ten problem., Inne poważne wyzwania obejmowały zaprojektowanie wymiennika ciepła, aby doprowadzić Gaz wlotowy do temperatury reakcji i schłodzić Gaz wylotowy, oraz opracowanie metody doprowadzenia katalizatora do temperatury reakcji.
pierwsza komercyjna instalacja amoniaku oparta na procesie Haber-Bosch została zbudowana przez BASF w Oppau w Niemczech. 2010-09-09 19: 00 9, 1913, o zdolności produkcyjnej 30 m. t. / dzień.
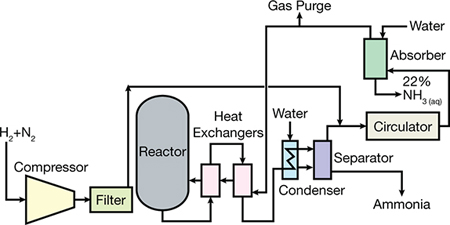
Jest to uproszczony arkusz przepływu pierwszej komercyjnej instalacji amoniaku firmy BASF.,
Rysunek 1 to arkusz przepływu pierwszej komercyjnej instalacji amoniaku. Reaktor oprócz tych pokazanych na schemacie zawierał wewnętrzny wymiennik ciepła.
Globalne wskaźniki produkcji
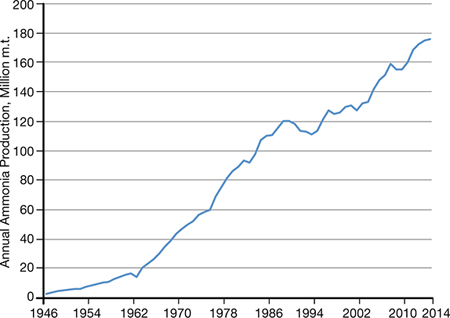
▲Rysunek 2. Światowa produkcja amoniaku stale rosła od 1946 do 2014 roku.
produkcja amoniaku stała się jedną z najważniejszych gałęzi przemysłu na świecie. Bez plonów, które byłyby możliwe dzięki nawozom i chemikaliom na bazie amoniaku, globalna populacja byłaby co najmniej o dwa do trzech miliardów mniej niż obecnie (3)., Produkcja amoniaku stale rośnie od 1946 roku (Rysunek 2) i szacuje się, że roczna produkcja amoniaku jest warta ponad 100 miliardów dolarów, a niektóre zakłady produkują ponad 3000 M.T./dzień NH3.
w 1983 r., z okazji 75. rocznicy założenia AIChE, panel wyróżniających się inżynierów chemicznych na niebieskiej wstążce nazwał to, co uważali za dziesięć największych osiągnięć inżynierii chemicznej na świecie [4]., Obejmując takie wyczyny, jak cudowne leki, włókna syntetyczne i energia atomowa, cytat zawierał również przełom, który pozwolił na produkcję dużych ilości amoniaku w kompaktowych, jednostkowych zakładach.
w ciągu ostatnich dziesięcioleci inżynierom chemicznym udało się stworzyć procesy, które wytwarzają ogromne ilości amoniaku przy stosunkowo niskich kosztach. Jeszcze 80 lat temu całkowita roczna produkcja syntetyzowanego amoniaku wyniosła nieco ponad 300 000 m.T. dzięki przełomom inżynierii chemicznej jedna nowoczesna instalacja amoniaku może wyprodukować ponad 750 000 m.t. / rok.,
około 88% amoniaku produkowanego rocznie zużywa się do produkcji nawozów. Większość pozostałej części przeznacza się na produkcję Formaldehydu. W 2014 r. Chiny wyprodukowały około 32,6% światowej produkcji, podczas gdy Rosja, Indie i USA wyprodukowały odpowiednio 8,1%, 7,6% i 6,4% (1). Podczas gdy większość światowej produkcji amoniaku opiera się na reformingu parowym gazu ziemnego, znaczne ilości są wytwarzane przez zgazowanie węgla; większość instalacji zgazowania znajduje się w Chinach.,
nowoczesne procesy produkcyjne
ogromny wzrost zapotrzebowania na amoniak w latach 1950-1980 wymagał większych, bardziej energooszczędnych instalacji. W tych dziesięcioleciach nastąpiła również zmiana w filozofii projektowania. Do tego czasu zakład amoniaku był uważany za zespół niepowiązanych jednostek, takich jak przygotowanie gazu, oczyszczanie gazu, sprężanie gazu i synteza amoniaku. Nowe innowacje i integralny projekt połączyły jednostki procesowe w najbardziej efektywny i wydajny sposób.
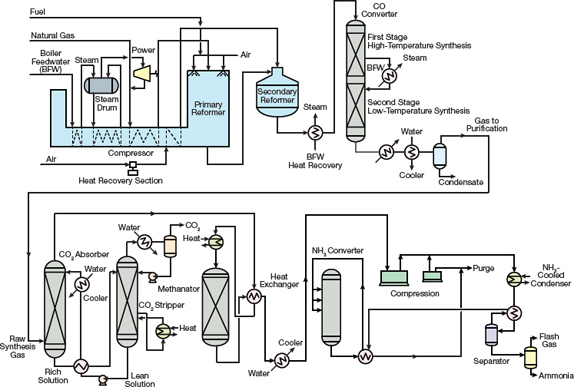
, KBR zaprojektował jedną z pierwszych jednotorowych instalacji amoniakalnych o dużej pojemności.
W połowie lat 60.XX wieku American Oil Co. zainstalowano jednoprzepływową instalację amoniaku zaprojektowaną przez M. W. Kellogga (MWK) w Texas City, TX, o wydajności 544 m.t./dobę. Koncepcja projektu pojedynczego pociągu (Rysunek 3) była tak rewolucyjna, że otrzymała Kirkpatrick Chemical Engineering Achievement Award w 1967 roku.,
w zakładzie zastosowano czterosuwową sprężarkę odśrodkową do sprężania gazu syntezowego do ciśnienia 152 bar, a końcowe sprężanie do ciśnienia roboczego 324 bar nastąpiło w sprężarce tłokowej. Wdrożono również sprężarki odśrodkowe dla pętli syntezy i usług chłodniczych, co zapewniło znaczne oszczędności.,
kluczowe różnice między procesem MWK a procesami stosowanymi w poprzednich instalacjach amoniaku obejmowały:
- wykorzystanie sprężarki odśrodkowej jako części sprężania gazu syntezowego
- maksymalizacja odzysku ciepła odpadowego z procesu
- wytwarzanie pary z ciepła odpadowego do wykorzystania w sterownikach turbin parowych
- wykorzystanie sprężarki chłodniczej do chłodzenia okresowego i atmosferycznego.
zintegrowany system, który zrównoważył zużycie energii, produkcję energii, wielkość sprzętu i wolumeny katalizatora, został włączony w całym zakładzie.,
większość zakładów zbudowanych w latach 1963-1993 miała duże konstrukcje jednotorowe z produkcją gazu syntezowego na poziomie 25-35 barów i syntezą amoniaku na poziomie 150-200 barów. Kolejna odmiana firmy Braun (obecnie KBR) oferowała niewielkie modyfikacje podstawowej konstrukcji. W oczyszczalniach Braun zastosowano reformator pierwotny lub rurowy o niskiej temperaturze wylotowej i wysokiej wycieku metanu, aby zmniejszyć rozmiar i koszt reformatora. Nadmiar powietrza dodano do reformatora wtórnego, aby zmniejszyć zawartość metanu w strumieniu wyjściowym reformatora pierwotnego do 1-2%., Nadmiar azotu i inne zanieczyszczenia zostały usunięte za metanatorem. Ponieważ gaz syntezowy był zasadniczo wolny od zanieczyszczeń, w celu uzyskania wysokiej konwersji amoniaku zastosowano dwa konwertery amoniaku o przepływie osiowym.
niektóre niedawno wybudowane instalacje mają system wytwarzania gazu syntezowego z tylko jednym reformerem (bez reformera wtórnego), systemem adsorpcji zmiennociśnieniowej (PSA) do odzyskiwania H2 i instalacją separacji powietrza jako źródłem N2., Ulepszenia w konstrukcji konwertera, takie jak promieniowe i poziome łoże katalizatora, wewnętrzne wymienniki ciepła i obróbka gazu syntezowego, pomogły zwiększyć stężenie amoniaku wychodzącego z konwertera syntezy z około 12% do 19-21%. Większa konwersja na jeden przejazd, a także bardziej wydajne turbiny i sprężarki, dodatkowo zmniejszają zużycie energii. Bardziej wydajne rozwiązania usuwania CO2, takie jak węglan potasu i metylodietanoloamina (MDEA), przyczyniły się do poprawy efektywności energetycznej. Większość nowoczesnych instalacji może produkować amoniak o zużyciu energii 28 GJ / m.t.,
oprócz ulepszeń konstrukcyjnych, mechanicznych i metalurgicznych dokonanych w tym czasie, ciśnienie robocze pętli syntezy zostało znacznie zmniejszone. Kiedy w latach 60. zbudowano pierwszą jednotorową elektrownię, zawierała ona pętlę syntezy wysokociśnieniowej. W 1962 roku firma MWK otrzymała zapytanie od Imperial Chemical Industries (ICI) o propozycję budowy zakładu o mocy 544 m.T./dzień w ich zakładzie w Severnside. MWK zaproponował 152-barową pętlę syntezy zamiast 324-barowej pętli.,
ponieważ opracowanie danych kinetycznych reakcji amoniaku przy 152 bar zajęłoby więcej czasu niż MWK musiał odpowiedzieć na zapytanie ICI, skontaktowali się z Haldorem Topsøe, aby wesprzeć ich plany. Topsøe miał dane obejmujące cały zakres ciśnienia zainteresowania MWK. Ponadto mieli program komputerowy do obliczania ilości katalizatora, który był wymagany przy niższym ciśnieniu roboczym. Mimo że ICI wybrała Bechtel do zaprojektowania zakładu, MWK było w stanie opracować arkusz przepływowy dla 544 m.t.,/ projekt dzienny ze sprężarkami odśrodkowymi i niskociśnieniową pętlą syntezy, co niektórzy uważają za najważniejsze wydarzenie w rozwoju jednotorowej instalacji amoniaku.
około dwa razy więcej katalizatora wymagano przy 152 barach niż przy 324 barach, co wydawało się ekonomicznie wykonalne. Chociaż konwerter wymagałby dwukrotnie większej objętości, niższe ciśnienie robocze zmniejszyłoby wymaganą grubość powłoki ciśnieniowej. W rezultacie masa metalu wymaganego dla konwertera i katalizatora pozostała mniej więcej taka sama., Pętla syntezy niższego ciśnienia pozwoliła również na zastosowanie sprężarek odśrodkowych zamiast sprężarek tłokowych. Kolejnym usprawnieniem było odzyskiwanie ciepła do wytwarzania pary wysokociśnieniowej dla napędów turbin parowych.
projekty instalacji w XXI wieku
w ciągu pierwszych kilku lat XXI wieku wprowadzono wiele ulepszeń w technologii instalacji amoniaku, które pozwalają istniejącym zakładom zwiększyć tempo produkcji i budować nowe instalacje o coraz większych możliwościach. Konkurencja między dostawcami technologii jest dość zacięta., Na rynku dominują obecnie trzej licencjodawcy technologii — KBR (Kellogg Brown i Root), Haldor Topsøe oraz Thyssenkrupp Industrial Solutions (TKIS). Amoniak Casale, który oferuje osiowo-promieniowe łoże katalizatora, jest liderem na rynku modernizacji istniejących instalacji.
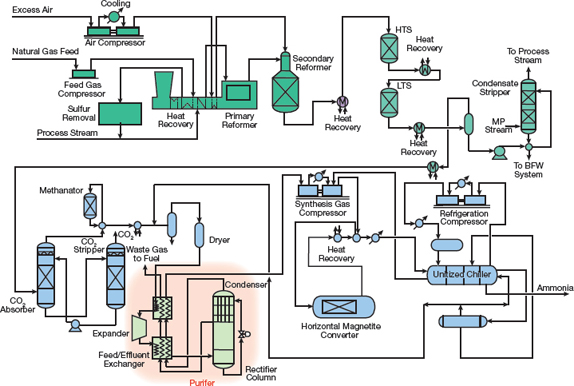
Nowoczesne instalacje amoniakalne zaprojektowane przez KBR wykorzystują swój własny projekt oczyszczacza.,
większość instalacji amoniakalnych zaprojektowanych niedawno przez KBR wykorzystuje proces oczyszczania (Rysunek 4), który łączy reforming o niskiej ciężkości w reformatorze pierwotnym, Oczyszczacz cieczy N2 za metanatorem w celu usunięcia zanieczyszczeń i regulacji stosunku H2:N2, zastrzeżoną konstrukcję kotła na ciepło odpadowe, jednostkowy agregat chłodniczy i poziomy konwerter syntezy amoniaku.
w zależności od konfiguracji instalacji zużycie energii może wynosić nawet 28 GJ / m.t. ponieważ reformator wtórny wykorzystuje nadmiar powietrza, reformator pierwotny może być mniejszy niż w konwencjonalnych konstrukcjach., Oczyszczacz kriogeniczny (pokazany na rysunku 4 w kolorze jasnozielonym z jasnopomarańczowym tłem), który składa się z ekspandera, skraplacza, wymiennika paszy/ścieków i kolumny prostowniczej, usuwa zanieczyszczenia, takie jak CO, CH4 i argon z gazu syntezowego, dostosowując stosunek H2:N2 gazu składowego w pętli amoniaku do optymalnego poziomu. Stężenie amoniaku wychodzącego z poziomego konwertera o niskim spadku ciśnienia wynosi 20-21%, co zmniejsza zapotrzebowanie na energię sprężarki z recyklingu., KBR oferuje również niskociśnieniową pętlę amoniaku, która wykorzystuje kombinację katalizatora magnetytowego i zastrzeżonego katalizatora rutenowego.
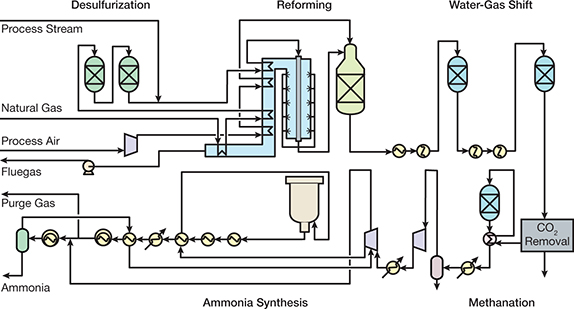
Haldor Topsøe oferuje konstrukcję instalacji amoniaku, która ma opatentowany reformator boczny, w którym palniki promiennikowe dostarczają ciepło do reakcji reformingu.
sekcja wytwarzania gazu syntezowego (lub przednia część) instalacji Haldor Topsøe (Rysunek 5) jest dość tradycyjna, z wyjątkiem własnego reformatora opalanego bocznie, który wykorzystuje palniki promieniujące do dostarczania ciepła do reakcji reformingu., Haldor Topsøe oferuje również opatentowany katalizator syntezy na bazie żelaza, Konwertery o przepływie promieniowym składające się z jednego, dwóch lub trzech łóżek oraz zastrzeżony kocioł na odpady z rur bagnetowych. Nowsze rozwiązania obejmują konstrukcje konwerterów S-300 i S-350. Konwerter S-300 jest konfiguracją trójpokładową z przepływem promieniowym z wewnętrznymi wymiennikami ciepła, podczas gdy konstrukcja S-350 łączy konwerter S-300 z jednokomorową konstrukcją s-50 z odzyskiem ciepła odpadowego między konwerterami, aby zmaksymalizować konwersję amoniaku.
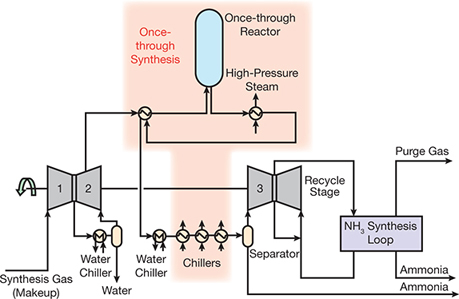
, Konstrukcja podwójnej pętli syntezy ThyssenKrupp obejmuje reaktor jednorazowy między sprężarkami gazu syntezowego.
ThyssenKrupp oferuje konwencjonalną instalację (Rysunek 6) z unikalną konstrukcją wtórnego reformatora, zastrzeżonym kotłem na ciepło odpadowe, konwerterami promieniowymi i pętlą syntezy amoniaku pod podwójnym ciśnieniem. Obecnie tempo produkcji 3300 m. t. / dzień można osiągnąć za pomocą procesu podwójnego ciśnienia TKIS.
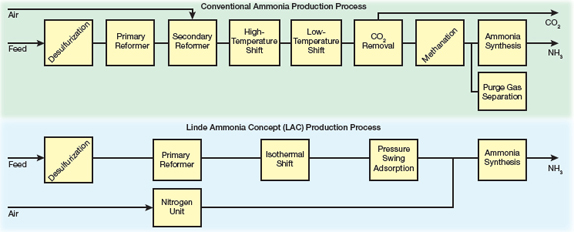
, Koncepcja amoniaku Linde (Lac) obejmuje adsorpcję zmiennociśnieniową do produkcji wodoru o wysokiej czystości oraz separację powietrza do produkcji azotu o wysokiej czystości.
Linde Ammonia Concept (Lac) to uznany system procesów technologicznych z ponad 25-letnim doświadczeniem w pracy w zakładach o wydajności od 200 M.T. / dobę do ponad 1750 M.T. / dobę., Schemat procesu LAC (Rysunek 7) zastępuje kosztowny i skomplikowany front end konwencjonalnej instalacji amoniakalnej dwoma sprawdzonymi, niezawodnymi jednostkami procesowymi:
- produkcja wodoru o bardzo wysokiej czystości z reformatora parowo-metanowego z oczyszczaniem PSA
- produkcja azotu o bardzo wysokiej czystości przez kriogeniczną jednostkę wytwarzania azotu, znaną również jako jednostka separacji powietrza (Asu).
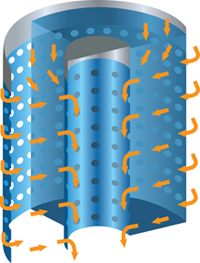
, Proces amoniaku Casale wykorzystuje łoże katalizatora, które wykorzystuje technologię osiowo-promieniową, która ma niższy spadek ciśnienia i wyższą wydajność niż standardowe łoże katalizatora.
projekt instalacji amoniaku Casale ma wydajność produkcji 2000 M.T. / dzień. Jedną z kluczowych cech tej konstrukcji jest technologia osiowo-promieniowa w złożu katalizatora (Rysunek 8). W osiowo-promieniowym łożu katalizatora większość gazu syntezowego przechodzi przez łoże katalizatora w kierunku promieniowym, tworząc bardzo niski spadek ciśnienia., Reszta gazu przechodzi przez górną warstwę katalizatora w kierunku osiowym, eliminując potrzebę stosowania górnej pokrywy na łożu katalizatora. Technologia osiowo-promieniowego łoża katalizatora Casale jest stosowana zarówno w przetwornikach wysokotemperaturowych, jak i niskotemperaturowych, a także w konwerterze syntezy.
inne technologie
niektórzy dostawcy technologii oferują Reformatory ogrzewane gazem (GHRs) do produkcji amoniaku w zakładach o małej mocy lub do zwiększania mocy., W przeciwieństwie do konwencjonalnie zaprojektowanych instalacji, które używają reformatora pierwotnego i reformatora wtórnego działającego szeregowo, instalacje z GHRs wykorzystują gorący gaz procesowy z reformatora wtórnego do dostarczania ciepła do reformatora pierwotnego. Zmniejsza to Rozmiar reformatora pierwotnego i eliminuje emisje CO2 ze stosu reformatora pierwotnego, dzięki czemu proces jest bardziej przyjazny dla środowiska.,
chociaż niektórzy producenci amoniaku opowiadają się za rozproszoną produkcją amoniaku w małych zakładach amoniaku, większość firm woli budować duże obiekty w pobliżu tanich źródeł surowców i transportować produkt statkiem, koleją lub rurociągiem do konsumentów.
amoniak z węgla
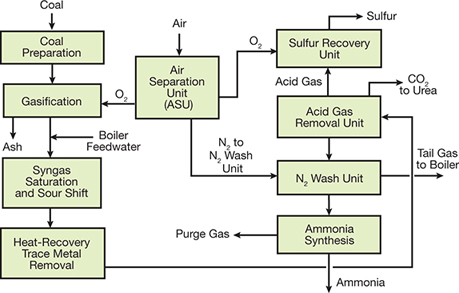
Figure Rysunek 9. Chiny produkują większość amoniaku z węgla.
Chiny produkują więcej amoniaku niż jakikolwiek inny kraj, a większość amoniaku produkuje z węgla (Rysunek 9).,
podstawowymi jednostkami przetwarzania w instalacji amoniaku na bazie węgla są ASU do oddzielania O2 i N2 od powietrza, zgazowacz, Jednostka przesunięcia kwaśnego gazu (SGS), Jednostka usuwania kwaśnego gazu (AGRU) i jednostka syntezy amoniaku. Tlen z ASU jest podawany do gazyfikatora w celu przekształcenia węgla w gaz syntezowy (H2, CO, CO2) i CH4. Istnieje wiele konstrukcji zgazowaczy, ale większość nowoczesnych zgazowaczy opiera się na złożach fluidalnych, które działają powyżej ciśnienia atmosferycznego i mają możliwość wykorzystania różnych źródeł węgla. W zależności od projektu można wytwarzać poziomy CO 30-60% objętościowo.,
Po zgazowaniu wszelkie cząstki stałe w gazie syntezowym są usuwane, a para jest dodawana do urządzenia SGS. W procesie SGS zazwyczaj wykorzystuje się katalizator kobaltu i molibdenu (CoMo) specjalnie zaprojektowany do pracy w środowisku siarkowym.
Po zmniejszeniu stężenia CO w gazie syntezowym do mniej niż 1% obj., gaz syntezowy jest podawany do AGRU, gdzie schłodzony roztwór do płukania metanolu (np. Rectisol) usuwa CO2 i siarkę z gazu syntezowego. Napowietrzny CO2 jest odpowietrzany lub podawany do instalacji mocznikowej. Strumień wylotu siarki jest podawany do jednostki odzysku siarki (SRU).,
gaz syntezowy przechodzący przez AGRU jest zwykle oczyszczany jedną z dwóch metod:
- zespół płuczący azotem do usuwania resztek CO i CH4 z gazu syntezowego przed doprowadzeniem go do pętli syntezy
- system PSA do usuwania CO i CH4.
myśli zamykające
w ciągu ostatnich 60 lat technologia procesu amoniaku uległa drastycznej poprawie. Układy roślin ewoluowały od projektów wielozadaniowych, często z różną liczbą pociągów w przednim końcu i pętli syntezy, do projektów jednozadaniowych., Przygotowanie gazu syntezowego w przedniej części instalacji wzrosło z ciśnienia atmosferycznego do ciśnienia 30-50 barg. Przepustowość wzrosła z 100 m.T./dzień do nawet 3300 m.t./dzień w jednym pociągu.
poprawiła się również wydajność energetyczna — od zużycia znacznie powyżej 60 GJ/m.t. amoniaku w zakładach na bazie koksu do 40-50 GJ/m.T. w pierwszych zakładach na bazie gazu ziemnego do 30-40 GJ / m.T. w pierwszych zakładach jednotorowych. Nowoczesne instalacje dodały odzysk ciepła przez produkcję pary przy ciśnieniu do 125 barg zarówno w sekcji przygotowania gazu syntezowego, jak i w pętli syntezy.,
jeśli chodzi o urządzenia procesowe, nastąpiła zmiana ze sprężarek tłokowych na sprężarki odśrodkowe. W konwerterze syntezy zastosowano wewnętrzny wymiennik ciepła w celu zwiększenia konwersji H2 i N2 do NH3. Projektanci wykorzystali odzyskiwanie wodoru z gazu oczyszczającego (w jednostkach takich jak systemy PSA) w celu zwiększenia produkcji lub zmniejszenia zużycia energii w zakładzie. Projektanci wdrożyli również systemy odsiarczania gorącego gazu zasilającego. Nastąpiła znaczna poprawa katalizatorów stosowanych w reformingu, konwersji przesunięć, metanacji i syntezie amoniaku.,
aby poprawić sterowanie procesem i bezpieczeństwo, rozproszone systemy sterowania (DCSS) do zaawansowanego sterowania procesem, a także systemy oprzyrządowania bezpieczeństwa (Siss), są obecnie standardem w instalacjach amoniaku. Przed uruchomieniem każdego procesu wykonywane są badania zagrożeń i operacyjności (HAZOP) oraz analizy warstwy ochrony (LOPAs). Postępy w zakresie symulatorów szkoleniowych i praktyk edukacyjnych zapewniają, że operatorzy i inżynierowie mogą bezpiecznie i skutecznie wykonywać swoje obowiązki.,
to tylko kilka z tysięcy ulepszeń technologicznych i bezpieczeństwa, które zostały wdrożone, aby przemysł amoniaku stał się jedną z najbardziej produktywnych i bezpiecznych branż na świecie.
podziękowania
autorzy potwierdzają pomoc KBR, ThyssenKrupp Industrial Solutions, Haldor Topsøe, Linde i Casale w dostarczaniu literatury technicznej dotyczącej odpowiednich technologii procesowych.