az ammónia kritikus fontosságú a műtrágyák gyártásában, és az egyik legnagyobb volumenű szintetikus vegyi anyag, amelyet a világon gyártanak. Ez a cikk az ammónia-termelés alakulását vizsgálja, és ismerteti a jelenlegi gyártási technológiákat.
A legtöbb ember az ammónia (NH3) csípős szagát tisztítószerekkel vagy szagú sókkal társítja. Az ammónia e két termékben történő felhasználása azonban csak a teljes globális ammónia-termelés kis részét teszi ki, amely 2014-ben körülbelül 176 millió metrikus tonna volt (1)., Annak érdekében, hogy értékeljük, hol vannak ma az ipar és a technológia, először nézzük meg, hogyan jutottunk ide.
az ammónia több mint 200 éve ismert. Joseph Priestley angol kémikus először 1774-ben izolálta a gáznemű ammóniát. Összetételét Claude Louis Berthollet francia kémikus állapította meg 1785-ben., 1898-ban Adolph Frank és Nikodem Caro úgy találták, hogy az N2-t kalcium-karbiddal kalcium-ciánamiddá lehet rögzíteni, amelyet ezután vízzel hidrolizálva ammóniát képezve (2):
cao + 3C ↔ CaC2 + CO
CaC2 + N2 ↔ CaCN2 + cacn2 + 3H2O ↔ CaCO3 + 2nh3
jelentős mennyiségű ammónia előállítása a ciánamid-eljárással a 20.század elejéig nem fordult elő. Mivel ez a folyamat nagy mennyiségű energiát igényelt, a tudósok erőfeszítéseiket az energiaszükséglet csökkentésére összpontosították.,
Fritz Haber német kémikus a modern ammóniaipar fejlődésének egyik legfontosabb munkáját végezte. Munka egy diák az Univ. Karlsruhe-ból ammóniát szintetizált a laboratóriumban az N2-ből és a H2-ből.
eközben Walther Nernst, az Univ fizikai kémiai professzora. Berlinben kifejlesztettek egy eljárást az ammónia előállítására azáltal, hogy az N2 és H2 keverékét 1000°C-on és 75 barg nyomáson átengedték egy vaskatalizátoron. Ezen a nyomáson nagyobb mennyiségű ammóniát tudott előállítani, mint a Haber és mások korábbi légköri nyomáson végzett kísérletei., A Nernst azonban arra a következtetésre jutott, hogy a folyamat nem valósítható meg, mivel nehéz vagy szinte lehetetlen volt (akkoriban) olyan nagy berendezéseket előállítani, amelyek képesek ilyen nyomáson működni.
Mindazonáltal mind Haber, mind Nernst folytatta a nagynyomású utat, hogy ammóniát állítson elő katalizátor felett. Haber végül kifejlesztett egy eljárást kereskedelmi mennyiségű ammónia előállítására, 1906-ban pedig 6% – os ammóniakoncentrációt tudott elérni egy ozmium katalizátorral töltött reaktorban., Ezt általában az ammónia kereskedelmi mennyiségben történő előállításának gyakorlati folyamatának kidolgozásának fordulópontjaként ismerik el.
Haber rájött, hogy a konverter egyetlen áthaladásakor képződött ammónia mennyisége túl alacsony ahhoz, hogy kereskedelmi érdekű legyen. A sminkgázból több ammónia előállításához újrahasznosítási rendszert javasolt, és szabadalmat kapott a koncepcióhoz. Haber újrahasznosítási ötlete megváltoztatta a folyamattechnika statikus felfogását a dinamikusabb megközelítés érdekében., A kémiai reakció egyensúlyán kívül Haber felismerte, hogy a reakciósebesség meghatározó tényező. Ahelyett, hogy egyszerű hozam egy egyszeri folyamat, ő koncentrált tér – idő hozam a rendszer újrahasznosítás.
a BASF megvásárolta Haber szabadalmait és megkezdte egy kereskedelmi folyamat fejlesztését. Több mint 2500 különböző katalizátor tesztelése után Carl Bosch, Alvin Mittasch és más BASF vegyészek 1910-ben kifejlesztettek egy támogatott vaskatalizátort ammónia előállítására., Még nehezebb feladat volt olyan berendezések kifejlesztése, amelyek ellenálltak a szükséges magas hőmérsékletnek és nyomásnak. A korai enyhe acélreaktor csak 80 órával tartott a dekarbonizáció miatt bekövetkező meghibásodás előtt. Bélés enyhe acél reaktorok puha vas (ami nem volt sebezhető decarbonization), hozzátéve, barázdák között a két bélésű, hogy kiadja a hidrogén, hogy volt szórt végig a puha vas bélés megoldotta ezt a problémát., Más jelentős kihívások tartalmazza tervezése hőcserélő, hogy hozza a belépő gáz, hogy a reakció hőmérséklet, hűvös a kilépési gáz, kidolgoznak egy módszer, hogy a katalizátor a reakció hőmérsékletét.
A Haber-Bosch folyamaton alapuló első kereskedelmi ammóniagyárat a BASF építette a németországi Oppauban. Az üzem szeptembertől üzemelt. 9, 1913, termelési kapacitása 30 m.t./nap.
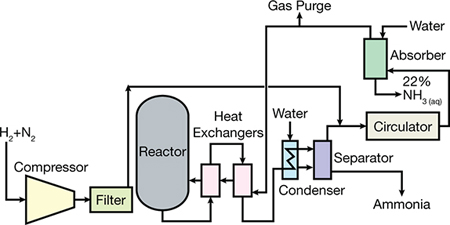
▲1.ábra. Ez a BASF első kereskedelmi ammóniaüzemének egyszerűsített áramlási lapja.,
az 1. ábra az első kereskedelmi ammónia növény áramlási lapja. A reaktor tartalmazott egy belső hőcserélő mellett látható a sematikus.
globális termelési arány
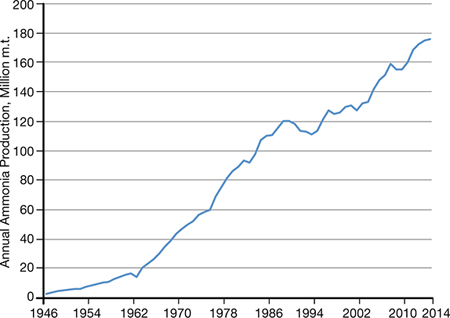
▲2.ábra. A világ ammóniatermelése 1946-tól 2014-ig folyamatosan nőtt.
Az ammónia-termelés a világ egyik legfontosabb iparágává vált. Az ammónia alapú műtrágyák és vegyi anyagok által lehetővé tett terméshozam nélkül a globális népesség legalább két-három milliárddal kevesebb lenne, mint ma (3)., Az ammónia termelése 1946 óta folyamatosan növekszik (2. ábra), és becslések szerint az ammónia éves termelése több mint 100 milliárd dollárt ér, egyes üzemek több mint 3000 m-t termelnek.t./nap NH3.
1983-ban, az AIChE alapításának 75. évfordulója alkalmából, a kiváló vegyészmérnökök kék szalagpanelje megnevezte azt, amit a világ tíz legnagyobb vegyipari mérnöki eredményének tartottak (4)., A Wonder drugs, a synthetic fibers és az atomic energy mellett a citation azt az áttörést is magában foglalta, amely lehetővé tette nagy mennyiségű ammónia előállítását kompakt, egy egységnyi üzemekben.
az elmúlt évtizedekben a vegyészmérnököknek sikerült olyan folyamatokat létrehozniuk, amelyek viszonylag alacsony költségek mellett hatalmas mennyiségű ammóniát hoznak létre. A közelmúltban, mint 80 évvel ezelőtt, a szintetizált ammónia teljes éves termelése alig több mint 300 000 m. t. a vegyészmérnöki áttöréseknek köszönhetően egy modern ammónia üzem több mint 750 000 m.t./év.,
az évente előállított ammónia körülbelül 88% – át a műtrágya gyártása során fogyasztják. A fennmaradó rész nagy része a formaldehid előállításába kerül. Kína 2014-ben a globális termelés mintegy 32,6% – át termelte, míg Oroszország, India és az Egyesült Államok 8,1% – ot, 7,6% – ot, illetve 6,4% – ot (1). Míg az ammónia globális termelésének nagy része a földgáz gőzreformációján alapul, jelentős mennyiségeket széngázosítással állítanak elő; a gázosító üzemek többsége Kínában található.,
Modern termelési folyamatok
az ammónia iránti kereslet 1950-től 1980-ig tartó óriási növekedése nagyobb, energiatakarékosabb üzemeket igényelt. Ezekben az évtizedekben a tervezési filozófia is megváltozott. Addig az időig egy ammóniagyárat nem kapcsolódó egységek, például gázkészítmények, Gáztisztítás, gázkompresszió és ammónia szintézis összeszerelésének tekintették. Az új innovációk és az integrált tervezési folyamategységek a leghatékonyabb és leghatékonyabb módon kapcsolódnak egymáshoz.
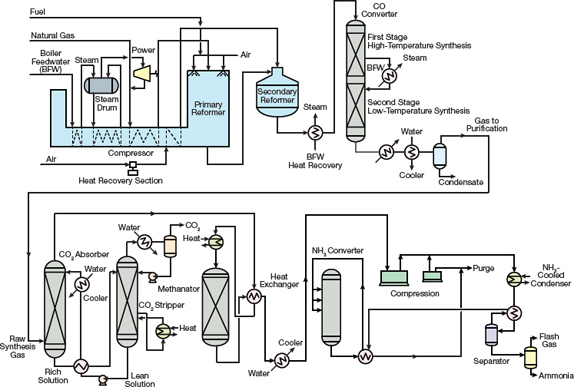
▲3.ábra., A KBR az egyik első egyvonatos, nagy kapacitású ammóniagyárat tervezte.
az 1960-as évek közepén az American Oil Co. az M. W. Kellogg (MWK) által tervezett egy átalakító ammónia üzemet a TX Texas Cityben, 544 m.t./nap kapacitással telepítették. Az egyvonatos tervezési koncepció (3. ábra) annyira forradalmi volt, hogy 1967-ben megkapta a Kirkpatrick Chemical Engineering Achievement Award Díjat.,
az üzem négyüléses centrifugális kompresszort használt a syngas 152 bar nyomásra történő összenyomásához, a végső tömörítés pedig 324 bar üzemi nyomásra történt egy dugattyús kompresszorban. A szintézis hurokhoz és a hűtési szolgáltatásokhoz centrifugális kompresszorokat is alkalmaztak, amelyek jelentős költségmegtakarítást nyújtottak.,
A főbb különbségek a MWK folyamat, az alkalmazott eljárások az előző ammónia a növények is:
- a centrifugális kompresszor részeként a szintézis gáz tömörítés
- maximalizálja a helyreállítási a hulladék hőt a folyamat
- generáló gőzt a hulladék hő felhasználásra gőzturbina vezetők
- használja a hűtő kompresszor lepusztult, illetve a légköri hűtés.
integrált rendszert építettek be, amely kiegyensúlyozott energiafogyasztást, energiatermelést, berendezésméretet és katalizátormennyiséget tartalmazott az üzem egész területén.,
az 1963 és 1993 között épült üzemek többsége nagy egyvonatos kivitelű volt, 25-35 bar szintézis gáztermeléssel, 150-200 bar ammónia szintézissel. A Braun (most KBR) egy másik változata enyhe módosításokat nyújtott az alaptervhez. A Braun tisztító üzemek egy primer vagy cső alakú reformert használtak alacsony kimeneti hőmérsékleten és magas metánszivárgással a reformer méretének és költségének csökkentése érdekében. A másodlagos reformátorhoz felesleges levegőt adtak, hogy az elsődleges reformátor kilépési áramának metántartalmát 1-2% – ra csökkentsék., A metanátor után a felesleges nitrogént és egyéb szennyeződéseket eltávolították. Mivel a szintézis gáz lényegében mentes volt a szennyeződésektől, két axiális áramlású ammónia átalakítót használtak a magas ammónia konverzió eléréséhez.
Egy nemrég épült, a növények egy szintézis gáz generációs rendszer csak egy reformer (nincs másodlagos reformer), egy nyomás-swing adszorpció (PSA) rendszer H2 hasznosítás, valamint a légi szétválasztás növény, mint a forrás N2., A fejlesztéseket az átalakító design, mint például a radiális vagy vízszintes katalizátor ágy, belső hőcserélők, valamint a szintézis gáz kezelés segített növelni ammónia koncentráció kilépés a szintézis átalakító körülbelül 12% – os 19-21%. A nagyobb átállás, a hatékonyabb turbinák és kompresszorok mellett, tovább csökkentette az energiafogyasztást. A hatékonyabb CO2-eltávolító megoldások, mint például a kálium-karbonát és a metildietanol-amin (MDEA), hozzájárultak az energiahatékonyság javításához. A legtöbb modern növény ammóniát képes előállítani 28 GJ/m energiafogyasztással. t.,
amellett, hogy a tervezési, mechanikai, kohászati fejlesztések során ez idő alatt, az üzemi nyomás a szintézis hurok jelentősen csökkent. Amikor az első egyvonatos üzemet az 1960-as években építették, nagynyomású szintézis hurkot tartalmazott. 1962 – ben az MWK vizsgálatot kapott az Imperial Chemical Industries (ICI)-től, hogy javaslatot tegyen egy 544 m.t./nap üzem építésére a Severnside telephelyükön. Az MWK 324 Baros hurok helyett 152 bar szintézis hurkot javasolt.,
körülbelül kétszer annyi katalizátorra volt szükség 152 bar-nál, mint a 324 bar-nál, ami gazdaságilag megvalósíthatónak tűnt. Bár az átalakítónak a térfogat kétszeresére lenne szüksége, az alacsonyabb üzemi nyomás csökkentené a nyomáshéj kívánt vastagságát. Ennek eredményeként a konverterhez szükséges fém súlya plusz a katalizátor körülbelül azonos maradt., Az alacsonyabb nyomású szintézis hurok lehetővé tette centrifugális Kompresszorok használatát a dugattyús kompresszorok helyett. Egy másik javulás a hő visszanyerése volt, hogy nagynyomású gőzt generáljon a gőzturbina meghajtókhoz.
Növényi minták a 21. században
az első pár évben a 21-ik században, számos fejlesztést végeztek az ammónia üzem, technológia, amely lehetővé teszi a meglévő növények növelni a termelést az árak, új növények épült egyre nagyobb kapacitással. A technológiai beszállítók közötti verseny meglehetősen heves., Jelenleg három technológiai licencadó — A KBR (Kellogg Brown és Root), a Haldor Topsøe és a ThyssenKrupp Industrial Solutions (Tkis) – uralja a piacot. Az ammónia Casale, amely axiális-radiális katalizátorágyat kínál, piacvezető a meglévő növények átalakításában.
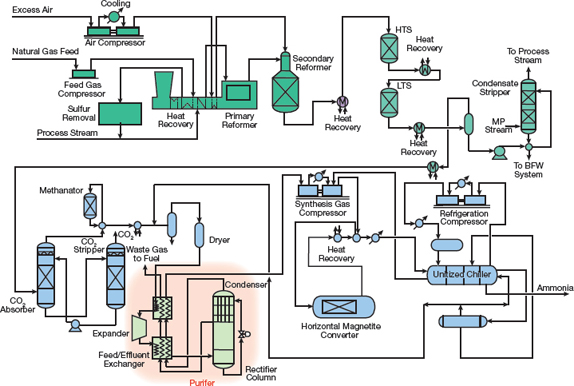
▲4.ábra. A KBR által tervezett modern ammóniaüzemek saját tisztító kialakítását alkalmazzák.,
a Legtöbb ammónia növények nemrég által tervezett KBR használja a Tisztító folyamat (4. Ábra), amely egyesíti alacsony-súlyos reformja az elsődleges reformer, folyékony N2 mossa büntetőt downstream a methanator, hogy távolítsa el a szennyeződéseket, majd állítsa be a H2:N2 arány, a saját hulladékhő kazán tervezési, egy unitized hűtő, mind horizontális ammónia szintézis converter.
az üzem konfigurációjától függően az energiafogyasztás akár 28 GJ/m.t. mivel a másodlagos reformer felesleges levegőt használ, az elsődleges reformer kisebb lehet, mint a hagyományos kivitelekben., A kriogén büntetőt (a 4. Ábrán a fény, zöld fény, narancssárga háttér), amely egy bővítő, kondenzátor, takarmány/elfolyó víz hőcserélő, valamint egyenirányító oszlop, eltávolítja a szennyeződéseket, mint például a CO, CH4, argon, a szintézis gáz beállítása közben a H2:N2 aránya a smink gáz az ammónia hurok az optimális szintre. Az alacsony nyomású vízszintes átalakítóból kilépő ammónia-koncentráció 20-21%, ami csökkenti az újrahasznosító kompresszor energiaigényét., A KBR egy alacsony nyomású ammóniahurokot is kínál, amely a magnetit katalizátor és a szabadalmaztatott ruténium katalizátor kombinációját alkalmazza.
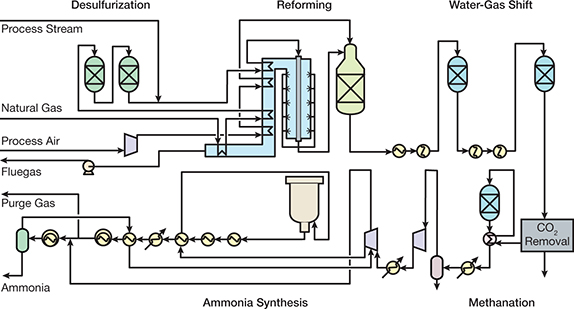
▲5.ábra. Haldor Topsøe kínál ammónia növény design, amely egy szabadalmaztatott oldalsó tüzelésű reformer, amelyben sugárzó égők hőt a reformáló reakció.
A létrehozására generációs § (vagy front-end), a Haldor Topsøe tervezett növény (5. Ábra) elég hagyományos, kivéve a saját oldalán-ki reformer, amely sugárzó égők, hogy a kínálat hatására reformálási reakcióban., A Haldor Topsøe saját fejlesztésű vas alapú szintézis katalizátort, egy, két vagy három ágyból álló radiális áramlású konvertereket, valamint egy szabadalmaztatott bajonettcsöves hulladékhő kazánt is kínál. A legújabb fejlesztések közé tartozik az S-300 és az S-350 átalakító. Az S-300 átalakító egy háromágyas radiális áramlású konfiguráció belső hőcserélőkkel, míg az S-350 kialakítás egy S-300 átalakítót kombinál egy S-50 egyágyas kialakítással, a konverterek közötti hulladékhő-visszanyeréssel az ammónia konverzió maximalizálása érdekében.
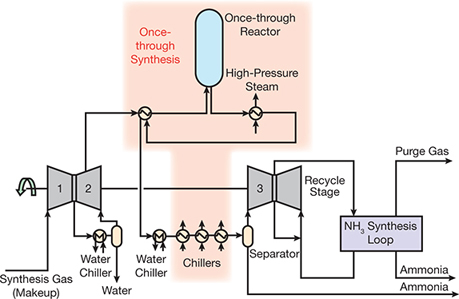
▲6.ábra., A ThyssenKrupp dual-pressure synthesis loop konstrukciója egy egyszeri reaktort tartalmaz a syngas Kompresszorok között.
a ThyssenKrupp hagyományos üzemet (6. ábra) kínál egyedi másodlagos reformer kialakítással, saját hulladékhő kazánnal, sugárirányú áramlású átalakítókkal és kettős nyomású ammónia szintézis hurokkal. Ma 3300 m/nap gyártási sebesség érhető el a TKIS kettős nyomású eljárással.
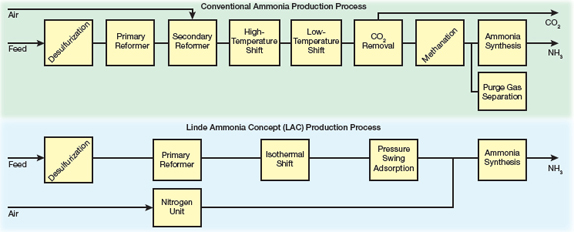
▲7.ábra., A Linde ammónia Concept (LAC) egy nagy tisztaságú hidrogén előállítására szolgáló nyomás-lengő adszorpciós egységet, valamint egy nagy tisztaságú nitrogéntermelésre szolgáló légszétválasztó egységet tartalmaz.
A Linde ammónia koncepció (Lac) egy megalapozott technológiai folyamatrendszer, amely több mint 25 éves működési tapasztalattal rendelkezik a 200 m.t./nap kapacitással rendelkező üzemekben, több mint 1750 m.t./nap., A LAC folyamat rendszer (7. Ábra) helyettesíti a költséges, bonyolult eleje egy hagyományos ammónia növény két jól bevált, megbízható folyamat egység:
- a termelés, az ultra-nagy tisztaságú hidrogént a gőz-metán reformer a PSA tisztítás
- a termelés, az ultra-nagy tisztaságú nitrogén által kriogén nitrogén generációs egység, is ismert, mint egy levegő elválasztó egység (ASU).
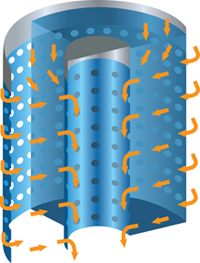
▲8.ábra., Az ammónia Casale eljárása olyan katalizátorágyat alkalmaz, amely axiális-radiális technológiát alkalmaz, amely alacsonyabb nyomáscsökkenéssel és nagyobb hatékonysággal rendelkezik, mint a standard katalizátorágyak.
Az ammónia Casale üzemének kialakítása 2000 m/nap gyártási sebességgel rendelkezik. Ennek a kialakításnak az egyik legfontosabb jellemzője az axiális-radiális technológia a katalizátorágyban (8.ábra). Axiális-radiális katalizátorágyban a szintézisgáz nagy része sugárirányban halad át a katalizátorágyon, ami nagyon alacsony nyomásesést eredményez., A gáz többi része axiális irányban halad át a katalizátor felső rétegén, így nincs szükség a katalizátorágy felső burkolatára. A Casale axiális-radiális katalizátorágy technológiáját mind a magas hőmérsékletű, mind az alacsony hőmérsékletű váltóátalakítókban, valamint a szintézis átalakítóban használják.
egyéb technológiák
egyes technológiai beszállítók gázfűtéses reformereket (GHRs) kínáltak kis kapacitású üzemekben ammónia előállítására vagy kapacitásnövelésre., Ellentétben a hagyományos tervezésű üzemek, amelyek egy elsődleges reformer és másodlagos reformer működő sorozat, növények GHRs használja a forró folyamat gáz a másodlagos reformer, hogy a kínálat a hő az elsődleges reformer. Ez csökkenti az elsődleges reformer méretét, és kiküszöböli az elsődleges reformer stack CO2-kibocsátását, így a folyamat környezetbarátabbá válik.,
annak ellenére, hogy egyes ammóniagyártók támogatják az ammónia kis ammóniaüzemekben történő elosztását, a legtöbb vállalat inkább nagy létesítményeket épít olcsó nyersanyagforrások közelében, és a terméket hajóval, vasúton vagy csővezetékkel szállítja a fogyasztóknak.
szénből származó ammónia
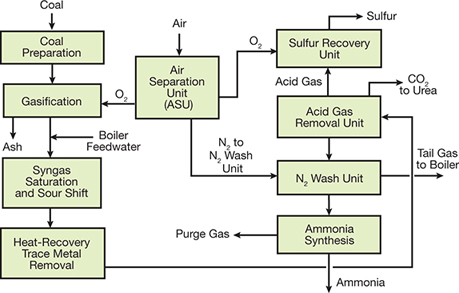
▲9.ábra. Kína ammóniájának nagy részét szénből állítja elő.
Kína több ammóniát termel, mint bármely más ország, és ammóniájának nagy részét szénből állítja elő (9.ábra).,
a szénalapú ammóniaüzem alapfeldolgozó egységei az O2 és N2 levegőtől való elválasztására szolgáló ASU, a gázosító, a savanyú gázeltolódás (SGS) egység, a savas gázeltávolító egység (AGRU) és az ammónia szintézis egység. Az ASU-ból származó oxigént a gázosítóba táplálják, hogy a szén szintézisgázt (H2, CO, CO2) és CH4-t alakítson ki. Sok gázosító tervek, de a legtöbb modern gázosítók alapulnak fluidizált ágyak, amelyek működnek a légköri nyomás felett, és képesek hasznosítani a különböző szén takarmányok. A tervezéstől függően 30-60 térfogatszázalék CO-szint állítható elő.,
gázosítás után a szintézis gázban lévő részecskéket eltávolítják, és gőzt adnak az SGS egységhez. Az SGS-eljárás jellemzően kobalt-és molibdén (CoMo) katalizátort használ, amelyet kifejezetten kénes környezetben történő működésre terveztek.
Miután csökkenti a CO-koncentráció a szintézis gáz, hogy kevesebb, mint 1 vol%, a létrehozására táplálja, hogy egy AGRU, ahol egy hűtött metanol mosó oldatot (pl., Rectisol) eltávolítja a CO2-kén a szintézis gáz. A CO2 felső részét vagy szellőztetik, vagy egy karbamidüzembe táplálják. A kén kimeneti áramát egy kénvisszahúzó egységbe (SRU) táplálják.,
Létrehozására, amely áthalad a AGRU általában tisztított által két módszerek:
- a nitrogén mossa egység távolítsa el a maradék CO, CH4 a létrehozására, mielőtt táplálja, hogy a szintézis loop
- a PSA rendszer CO, CH4 eltávolítása.
záró gondolatok
az elmúlt 60 évben az ammónia-folyamat technológiája drasztikusan javult. A növényi elrendezések a többvonatos kivitelekből, gyakran különböző számú vonatból alakultak ki az elülső és a szintézis hurokban, az egyvonatos tervekhez., A szintézis gázkészítmény a növény elülső végén a légköri nyomásról 30-50 barg nyomásra nőtt. A kapacitások napi 100 m-ről napi 3300 m-re nőttek egyetlen vonaton.
az energiahatékonyság is javult — a koksz alapú üzemekben az ammónia fogyasztása jóval 60 GJ/m t felett 40-50 GJ/m.t. az első földgáz alapú üzemekben az 30-40 GJ/m.t. az első egyvonatos üzemekben. A Modern növények mind a syngas előkészítő szakaszban, mind a szintézis hurokban akár 125 barg nyomáson is hozzáadták a gőztermelés hővisszanyerését.,
a feldolgozó berendezések tekintetében elmozdulás történt a dugattyús kompresszorokról a centrifugális kompresszorokra. A szintézis átalakítóban belső hőcserélőt alkalmaztak a H2 és N2 NH3-ra történő átalakításának növelése érdekében. A tervezők a hidrogén visszanyerését a tisztító gázból (olyan egységekben, mint például a PSA rendszerek) a termelés fokozása vagy a növény energiafogyasztásának csökkentése érdekében. A tervezők is végre forró takarmány gáz kéntelenítő rendszerek. Jelentős fejlesztések történtek a reformáláshoz, a váltáshoz, a metanációhoz és az ammónia szintéziséhez használt katalizátorokban.,
a folyamatirányítás és a biztonság javítása érdekében a fejlett folyamatvezérléshez használt elosztott vezérlőrendszerek (DCSS), valamint a biztonsági műszerekkel ellátott rendszerek (SISs) már szabványosak az ammóniagyárakban. Mielőtt bármilyen folyamat elindulna az interneten, veszélyességi és működőképességi (HAZOP) vizsgálatokat és védelmi elemzéseket (LOPAs) végeznek. A szimulátorok és oktatási gyakorlatok terén elért eredmények biztosítják, hogy az üzemeltetők és a mérnökök biztonságosan és hatékonyan tudják ellátni feladataikat.,
ez csak néhány a több ezer fejlesztések a technológia, valamint biztonsági hajtották végre, hogy az ammónia ipari egyik legtermékenyebb biztonságban iparágak a világon.
Köszönetnyilvánítás
a szerzők elismerik a KBR, a ThyssenKrupp Industrial Solutions, A Haldor Topsøe, a Linde és a Casale segítségét a saját technológiai technológiáikkal kapcsolatos műszaki szakirodalom biztosításához.