amoniacul este esențial în fabricarea îngrășămintelor și este una dintre cele mai mari substanțe chimice sintetice produse în lume. Acest articol explorează evoluția producției de amoniac și descrie tehnologiile actuale de fabricație.majoritatea oamenilor asociază mirosul înțepător de amoniac (NH3) cu substanțe de curățare sau săruri mirositoare. Cu toate acestea, utilizarea amoniacului în aceste două produse reprezintă doar o mică parte din producția globală totală de amoniac, care a fost de aproximativ 176 de milioane de tone metrice în 2014 (1)., Pentru a aprecia în cazul în care industria și tehnologia sunt astăzi, să aruncăm mai întâi o privire la modul în care am ajuns aici.amoniacul este cunoscut de mai bine de 200 de ani. Joseph Priestley, un chimist englez, a izolat pentru prima dată amoniacul gazos în 1774. Compoziția sa a fost constatată de chimistul francez Claude Louis Berthollet în 1785., În 1898, Adolf Frank și Nikodem Caro a constatat că N2 ar putea fi fixate cu carbură de calciu pentru a forma cianamida de calciu, care ar putea fi apoi hidrolizat cu apă pentru a forma amoniac (2):
CaO + 3C ↔ CaC2 + CO
CaC2 + N2 ↔ CaCN2 + C
CaCN2 + 3H2O ↔ CaCO3 + 2NH3
producerea de cantități semnificative de amoniac folosind cianamida procesul nu a avut loc până la începutul secolului 20. Deoarece acest proces a necesitat cantități mari de energie, oamenii de știință și-au concentrat eforturile pe reducerea cerințelor energetice.,chimistul German Fritz Haber a efectuat unele dintre cele mai importante lucrări în dezvoltarea industriei moderne a amoniacului. Lucrul cu un student la Univ. din Karlsruhe, el a sintetizat amoniacul în laborator de la N2 și H2.între timp, Walther Nernst, profesor de chimie fizică la Univ. Berlin, a dezvoltat un proces pentru a face amoniac prin trecerea unui amestec de N2 și H2 peste un catalizator de fier la 1.000°C și 75 barg presiune. El a fost capabil să producă cantități mai mari de amoniac la această presiune decât experimentele anterioare ale lui Haber și ale altora la presiune atmosferică., Cu toate acestea, Nernst a concluzionat că procesul nu era fezabil, deoarece era dificil sau aproape imposibil (la acel moment) să se producă echipamente mari capabile să funcționeze la această presiune.cu toate acestea, atât Haber cât și Nernst au urmărit calea de înaltă presiune pentru a produce amoniac peste un catalizator. Haber a dezvoltat în cele din urmă un proces pentru producerea cantităților Comerciale de amoniac, iar în 1906 a reușit să obțină o concentrație de amoniac de 6% într-un reactor încărcat cu un catalizator de osmiu., Acest lucru este, în general, recunoscut ca punct de cotitură în dezvoltarea unui proces practic de producere a amoniacului în cantități comerciale.Haber și-a dat seama că cantitatea de amoniac formată într-o singură trecere printr-un convertor era mult prea mică pentru a fi de interes comercial. Pentru a produce mai mult amoniac din gazul de machiaj, el a propus un sistem de reciclare și a primit un brevet pentru concept. Ideea de reciclare a lui Haber a schimbat percepția ingineriei proceselor ca statică în favoarea unei abordări mai dinamice., În plus față de echilibrul reacției chimice, Haber a recunoscut că rata de reacție a fost un factor determinant. În loc de randament simplu într-un proces o singură dată, el sa concentrat pe randamentul spațiu-timp într-un sistem cu reciclare.BASF a achiziționat brevetele Haber și a început dezvoltarea unui proces comercial. După testarea a peste 2.500 de catalizatori diferiți, Carl Bosch, Alvin Mittasch și alți chimiști BASF au dezvoltat un catalizator de fier promovat pentru producerea amoniacului în 1910., Dezvoltarea echipamentelor care ar putea rezista temperaturilor și presiunii ridicate necesare a fost o sarcină și mai dificilă. Un reactor de oțel moale timpuriu a durat doar 80 de ore înainte de eșec din cauza decarbonizării. Căptușirea reactoarelor din oțel moale cu fier moale (care nu era vulnerabil la decarbonizare) și adăugarea de caneluri între cele două garnituri pentru a elibera hidrogenul care difuzase prin căptușeala de fier moale a rezolvat această problemă., Alte provocări majore au inclus proiectarea unui schimbător de căldură pentru a aduce gazul de intrare la temperaturile de reacție și a răci gazul de ieșire și a concepe o metodă pentru a aduce catalizatorul la temperatura de reacție.prima fabrică comercială de amoniac bazată pe procesul Haber-Bosch a fost construită de BASF la Oppau, Germania. Planta a mers pe flux pe Septembrie. 9, 1913, cu o capacitate de producție de 30 m.t./zi.
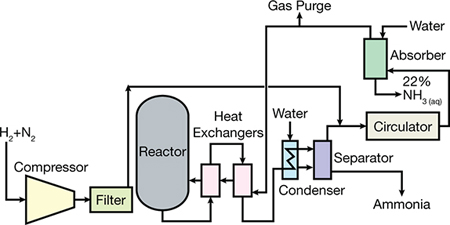
▲Figura 1. Aceasta este o foaie de flux simplificată a primei fabrici Comerciale de amoniac de către BASF.,figura 1 este o foaie de flux a primei instalații comerciale de amoniac. Reactorul conținea un schimbător de căldură intern în plus față de cele prezentate pe schemă.
ratele globale de producție
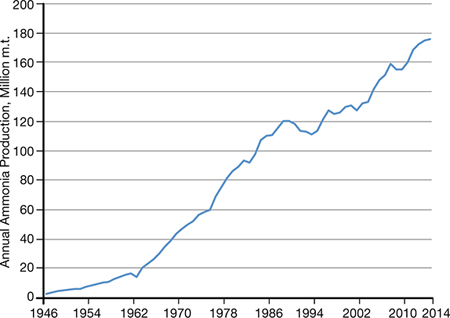
▲Figura 2. Producția mondială de amoniac a crescut constant din 1946 până în 2014.producția de amoniac a devenit una dintre cele mai importante industrii din lume. Fără randamentul culturilor posibil prin îngrășămintele și substanțele chimice pe bază de amoniac, populația globală ar fi cu cel puțin două-trei miliarde mai mică decât este în prezent (3)., Producția de amoniac a crescut constant din 1946 (Figura 2) și se estimează că producția anuală de amoniac este în valoare de peste 100 de miliarde de dolari, unele fabrici producând mai mult de 3.000 m.t./Zi de NH3.
În 1983, cu ocazia aniversării a 75 de ani de AIChE fondatori, o panglică albastră grup distins de ingineri chimice numit ceea ce credeau că lumea e mai mare de zece inginerie chimică realizări (4)., Cuprinzând astfel de fapte precum medicamentele minune, fibrele sintetice și energia atomică, citarea a inclus, de asemenea, descoperirea care a permis producerea unor cantități mari de amoniac în plante compacte, cu o singură unitate.în ultimele decenii, inginerii chimici au reușit să creeze procese care produc cantități mari de amoniac la costuri relativ scăzute. În urmă cu 80 de ani, producția anuală totală de amoniac sintetizat a fost de peste 300.000 m.t. datorită descoperirilor ingineriei chimice, o instalație modernă de amoniac poate produce mai mult de 750.000 m.t./an.,aproximativ 88% din amoniacul produs anual este consumat la fabricarea îngrășămintelor. Cea mai mare parte a restului intră în producția de formaldehidă. China a produs aproximativ 32,6% din producția globală în 2014, în timp ce Rusia, India și SUA au produs 8,1%, 7,6% și, respectiv, 6,4% (1). În timp ce cea mai mare parte a producției globale de amoniac se bazează pe reformarea cu abur a gazelor naturale, cantități semnificative sunt produse prin gazeificarea cărbunelui; majoritatea instalațiilor de gazeificare sunt situate în China.,
procese Moderne de producție
creșterea extraordinară în amoniac cererii din 1950 până în 1980 a necesitat mai mare, mai eficient energetic plante. Acele decenii au văzut, de asemenea, o schimbare în filosofia designului. Până în acel moment, o instalație de amoniac a fost considerată ca un ansamblu de unități independente, cum ar fi prepararea gazelor, Purificarea gazelor, compresia gazelor și sinteza amoniacului. Noile inovații și un design integral au legat unitățile de proces în cele mai eficiente și eficiente moduri.
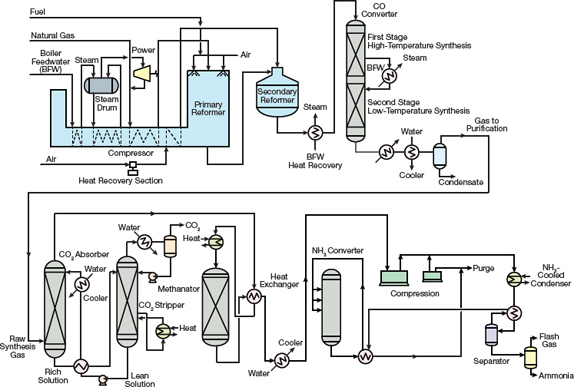
▲Figura 3., KBR a proiectat una dintre primele instalații de amoniac cu un singur tren, de mare capacitate.la mijlocul anilor 1960, American Oil Co. instalat cu un singur convertor instalație de amoniac proiectat de M. W. Kellogg (MWK) de la Texas City, TX, cu o capacitate de 544 m.t./zi. Conceptul de proiectare cu un singur tren (Figura 3) a fost atât de revoluționar încât a primit Premiul Kirkpatrick Chemical Engineering Achievement Award în 1967.,instalația a folosit un compresor centrifugal cu patru carcase pentru a comprima gazul de sinteză la o presiune de 152 bar, iar compresia finală la o presiune de funcționare de 324 bar a avut loc într-un compresor cu piston. De asemenea, au fost implementate compresoare centrifugale pentru bucla de sinteză și servicii de refrigerare, ceea ce a oferit economii semnificative de costuri.,
diferențele cheie între MWK proces și procesele utilizate în anii amoniac plante incluse:
- folosind un compresor centrifugal, ca parte a sintezei de comprimare gaze
- maximizarea recuperare a căldurii reziduale din procesul
- generatoare de abur de căldură reziduală pentru utilizarea în turbine cu abur drivere
- utilizarea refrigerare compresor pentru consultare și atmosferice de refrigerare.o schemă integrată care a echilibrat consumul de energie, producția de energie, dimensiunea echipamentelor și volumele de catalizator a fost încorporată în întreaga instalație.,majoritatea instalațiilor construite între 1963 și 1993 au avut proiecte mari cu un singur tren, cu producția de gaze de sinteză la 25-35 bar și sinteza amoniacului la 150-200 bar. O altă variantă a lui Braun (acum KBR) a oferit modificări ușoare designului de bază. Instalațiile de procesare a purificatorului Braun au utilizat un reformator primar sau tubular cu o temperatură scăzută de ieșire și o scurgere ridicată de metan pentru a reduce dimensiunea și costul reformatorului. Excesul de aer a fost adăugat la reformatorul secundar pentru a reduce conținutul de metan al fluxului de ieșire al reformatorului primar la 1-2%., Excesul de azot și alte impurități au fost îndepărtate în aval de metanator. Deoarece gazul de sinteză era în esență lipsit de impurități, au fost utilizați doi convertizori de amoniac cu flux axial pentru a obține o conversie ridicată a amoniacului.unele instalații recent construite au un sistem de generare a gazelor de sinteză cu un singur reformator (fără reformator secundar), un sistem de adsorbție sub presiune (PSA) pentru recuperarea H2 și o instalație de separare a aerului ca sursă de N2., Îmbunătățirile în proiectarea convertorului, cum ar fi paturile de catalizator radiale și orizontale, schimbătoarele de căldură interne și tratarea gazelor de sinteză, au contribuit la creșterea concentrațiilor de amoniac care ies din convertorul de sinteză de la aproximativ 12% la 19-21%. O conversie mai mare pe trecere, împreună cu turbine și compresoare mai eficiente, a redus și mai mult consumul de energie. Soluțiile mai eficiente de eliminare a CO2, cum ar fi carbonatul de potasiu și metildietanolamina (MDEA), au contribuit la îmbunătățirea eficienței energetice. Majoritatea plantelor moderne pot produce amoniac cu un consum de energie de 28 GJ / m. t.,pe lângă îmbunătățirile de proiectare, mecanice și metalurgice făcute în acest timp, presiunea de funcționare a buclei de sinteză a fost redusă semnificativ. Când prima fabrică cu un singur tren a fost construită în anii 1960, aceasta conținea o buclă de sinteză de înaltă presiune. În 1962, MWK a primit o anchetă de la Imperial Chemical Industries (ICI) pentru o propunere de a construi o instalație de 544 m.T./zi la site-ul lor Severnside. MWK a propus o buclă de sinteză de 152 de bare în loc de o buclă de 324 de bare.,deoarece dezvoltarea datelor cinetice pentru reacția amoniacului la 152 bar ar dura mai mult timp decât MWK a trebuit să răspundă anchetei ICI, au contactat Haldor Topsøe pentru a-și susține planurile. Topsøe a avut date care acoperă întreaga gamă de presiune de interes pentru MWK. În plus, aveau un program de calculator pentru calcularea cantității de catalizator care era necesară la presiunea de funcționare mai mică. Chiar dacă ICI a ales Bechtel pentru proiectarea fabricii, MWK a fost capabil să dezvolte un flux pentru un 544-m.t.,/ design de zi cu compresoare centrifugale și o buclă de sinteză de joasă presiune, pe care unii oameni o consideră cel mai important eveniment unic în dezvoltarea instalației de amoniac cu un singur tren.
aproximativ de două ori mai mult catalizator a fost necesar la 152 bar decât la 324 bar, o creștere care părea fezabilă din punct de vedere economic. Deși convertorul ar avea nevoie de două ori volumul, presiunea de funcționare mai mică ar reduce grosimea necesară a carcasei de presiune. Ca urmare, greutatea metalului necesar convertorului plus catalizatorul a rămas aproximativ aceeași., Bucla de sinteză la presiune inferioară a permis, de asemenea, utilizarea compresoarelor centrifugale în locul compresoarelor cu piston. O altă îmbunătățire a fost recuperarea căldurii pentru a genera abur de înaltă presiune pentru acționările turbinelor cu abur.în primii ani ai secolului 21, s-au făcut multe îmbunătățiri în tehnologia instalațiilor de amoniac care permit instalațiilor existente să crească ratele de producție și să se construiască noi instalații cu capacități din ce în ce mai mari. Concurența dintre furnizorii de tehnologie este destul de acerbă., Trei tehnologia licențiatorii — KBR (Kellogg Brown și Rădăcină), Haldor Topsøe, și ThyssenKrupp Solutii Industriale (TKIS) — în prezent domină piața. Amoniacul Casale, care oferă un design axial-radial al patului catalizator, este lider de piață în modernizarea instalațiilor existente.
▲Figura 4. Instalațiile moderne de amoniac proiectate de KBR folosesc designul purificator propriu.,
de cele Mai multe fabrici de amoniac, recent proiectat de KBR utiliza său Purificator de proces (Figura 4), care combină scăzut de severitate reforma în principal reformator, un lichid N2 spălați-purificator în aval de methanator pentru a elimina impuritățile și de a regla H2:N2 raport, o proprietate a deșeurilor-cazan de căldură design, un unificate chiller, și o orizontală amoniac de sinteză converter.în funcție de configurația instalației, consumul de energie poate fi de până la 28 GJ/m.T. deoarece reformatorul secundar utilizează excesul de aer, reformatorul primar poate fi mai mic decât în proiectele convenționale., Purificatorul criogenic (prezentat în Figura 4 în verde deschis cu fundal portocaliu deschis), care constă dintr-un expandor, condensator, schimbător de alimentare/efluent și coloană de redresor, îndepărtează impuritățile cum ar fi CO, CH4 și argon din gazul de sinteză, reglând în același timp raportul H2:N2 al gazului de machiaj din bucla de amoniac la nivelul optim. Concentrația de amoniac care iese din convertorul orizontal de joasă presiune este de 20-21%, ceea ce reduce cerințele de energie pentru compresorul de reciclare., KBR oferă, de asemenea, o buclă de amoniac de joasă presiune care utilizează o combinație de catalizator de magnetită și catalizatorul său ruteniu proprietar.
▲Figura 5. Haldor topsøe oferă un design al instalației de amoniac care are un reformator cu ardere laterală, în care arzătoarele radiante furnizează căldură pentru reacția de reformare.
syngas generație secțiune (sau front-end) de un Haldor Topsøe-proiectat de plante (Figura 5) este destul de tradițional, cu excepția său de proprietate laterală-a tras reformator, care utilizează radiant arzătoare de a furniza căldură pentru reacția de reformare., Haldor topsøe oferă, de asemenea, un catalizator de sinteză pe bază de fier, convertoare de flux radial constând dintr-unul, două sau trei paturi și un cazan de căldură uzată cu baionetă. Evoluțiile mai recente includ modelele convertoarelor S-300 și S-350. Convertorul S-300 este o configurație cu flux radial cu trei paturi, cu schimbătoare de căldură interne, în timp ce designul S-350 combină un convertor S-300 cu un design S-50 cu un singur pat, cu recuperarea căldurii reziduale între convertoare pentru a maximiza conversia amoniacului.
▲Figura 6., Proiectarea buclei de sinteză cu dublă presiune ThyssenKrupp prezintă un reactor o singură dată între compresoarele de syngas.ThyssenKrupp oferă o instalație convențională (Figura 6) cu un design unic reformator secundar, un cazan de căldură uzată, convertoare de debit radial și o buclă de sinteză a amoniacului cu dublă presiune. Astăzi, o rată de producție de 3.300 m.t./zi poate fi realizată folosind procesul tkis cu dublă presiune.
▲Figura 7., Linde amoniacul Concept (LAC) dispune de o unitate de adsorbție oscilantă sub presiune pentru producția de hidrogen de înaltă puritate și o unitate de separare a aerului pentru producția de azot de înaltă puritate.
Linde Amoniac Concept (ALC) este o tehnologie stabilit procesul schema cu peste 25 de ani de experiență de operare în centrale cu o capacitate de 200 de m.t./zi la peste 1.750 m.t./zi., LAC procesul de schemă (Figura 7) înlocuiește costisitoare și complexe front-end a unui convenționale instalație de amoniac cu două bine-dovedit, de încredere unitățile de proces:
- producția de ultra-înaltă puritate hidrogen dintr-un abur-gaz metan reformator cu PSA purificare
- producția de ultra-înaltă puritate azot de un criogenic cu azot unitatea de generare, de asemenea, cunoscut ca o unitate de separare a aerului (ASU).
▲figura 8., Amoniacul Casale are un pat de catalizator care utilizează tehnologia axial-radială, care are o cădere de presiune mai mică și o eficiență mai mare decât paturile standard de catalizator.proiectarea fabricii de amoniac Casale are o rată de producție de 2.000 m.t./zi. Una dintre caracteristicile cheie ale acestui design este tehnologia axial-radială în patul catalizatorului (figura 8). Într-un pat de catalizator axial-radial, cea mai mare parte a gazului de sinteză trece prin patul de catalizator într-o direcție radială, creând o cădere de presiune foarte scăzută., Restul gazului trece printr-un strat superior de catalizator într-o direcție axială, eliminând necesitatea unui capac superior pe patul catalizatorului. Tehnologia axial-radială a catalizatorului Casale este utilizată atât în convertoarele de schimbare a temperaturii înalte și joase, cât și în convertorul de sinteză.
Alte tehnologii
Unii furnizori de tehnologie au oferit incalzite cu gaz reformatori (GHRs) pentru producția de amoniac în mici instalații de capacitate sau pentru creșterea capacității., Spre deosebire de instalațiile proiectate convențional care utilizează un reformator primar și un reformator secundar care funcționează în serie, instalațiile cu GHR utilizează gazul de proces fierbinte de la reformatorul secundar pentru a furniza căldură reformatorului primar. Acest lucru reduce dimensiunea reformatorului primar și elimină emisiile de CO2 din stiva reformatorului primar, făcând procesul mai ecologic.,chiar dacă unii producători de amoniac pledează pentru producția distribuită de amoniac în fabricile mici de amoniac, majoritatea companiilor preferă să construiască instalații mari în apropierea surselor de materii prime ieftine și să transporte produsul pe navă, pe calea ferată sau pe conducte către consumatori.
amoniac din cărbune
▲Figura 9. China produce cea mai mare parte a amoniacului din cărbune.China produce mai mult amoniac decât orice altă țară și produce majoritatea amoniacului său din cărbune (Figura 9).,unitățile de procesare de bază dintr-o instalație de amoniac pe bază de cărbune sunt ASU pentru separarea O2 și N2 de aer, gazificatorul, unitatea de schimbare a gazului acru (SGS), unitatea de eliminare a gazului acid (AGRU) și unitatea de sinteză a amoniacului. Oxigenul din ASU este alimentat la gazificator pentru a transforma cărbunele în gaz de sinteză (H2, CO, CO2) și CH4. Există multe gazeificare modele, dar cele mai moderne gasifiers se bazează pe fluidizat paturi care operează peste presiunea atmosferică și au capacitatea de a utiliza diferite cărbune feed-uri. În funcție de proiectare, pot fi produse niveluri de CO de 30-60% în volum.,după gazificare, orice particule din gazul de sinteză sunt îndepărtate și aburul este adăugat la unitatea SGS. Procesul SGS utilizează de obicei un catalizator de cobalt și molibden (CoMo) special conceput pentru funcționarea într-un mediu cu sulf.după reducerea concentrației de CO în gazul de sinteză la mai puțin de 1% vol, gazul de sinteză este alimentat într-un AGRU, unde o soluție răcită de spălare a metanolului (de exemplu, Rectisol) elimină CO2 și sulful din gazul de sinteză. CO2 deasupra capului este fie ventilat sau alimentat la o instalație de uree. Fluxul de evacuare a sulfului este alimentat la o unitate de recuperare a sulfului (SRU).,
Syngas care trece prin AGRU este de obicei purificat prin una dintre cele două metode:
- o unitate de spălare cu azot pentru a îndepărta Co și CH4 reziduale din syngas înainte de a fi alimentat în bucla de sinteză
- un sistem PSA pentru îndepărtarea CO și CH4.
gânduri de închidere
în ultimii 60 de ani, tehnologia procesului de amoniac sa îmbunătățit drastic. Planurile de plante au evoluat de la modele cu mai multe trenuri, adesea cu un număr diferit de trenuri în bucla frontală și sinteză, la modele cu un singur tren., Pregătirea gazului de sinteză în capătul frontal al instalației a crescut de la presiunea atmosferică la presiunea 30-50 barg. Capacitățile au crescut de la 100 m.t./zi la 3.300 m.t./zi într-un singur tren.
eficiența Energetică s-au îmbunătățit, precum și — la consumuri de peste 60 GJ/m.t. de amoniac în coca-cola pe bază de plante la 40-50 GJ/m.t. în primul gaze naturale pe bază de plante la 30-40 GJ/m.t. în primele single-tren plante. Instalațiile moderne au adăugat recuperarea căldurii prin producerea de abur la presiuni de până la 125 barg atât în secțiunea de preparare a gazelor de sinteză, cât și în bucla de sinteză.,în ceea ce privește echipamentele de proces, a existat o trecere de la Compresoare cu piston la compresoare centrifugale. Un schimbător de căldură intern a fost implementat în convertorul de sinteză pentru a crește conversia H2 și N2 la NH3. Proiectanții au apelat la recuperarea hidrogenului din gazul de purjare (în unități precum sistemele PSA) pentru a spori producția sau a reduce consumul de energie al plantelor. Designerii au implementat, de asemenea, sisteme de desulfurare a gazelor de alimentare la cald. S-au înregistrat îmbunătățiri semnificative ale catalizatorilor utilizați în reformare, conversie schimbare, metanare, și sinteza amoniacului.,pentru a îmbunătăți controlul și siguranța proceselor, sistemele de control distribuit (DCSS) pentru controlul avansat al proceselor, precum și sistemele instrumentate de siguranță (siss) sunt acum standard în instalațiile de amoniac. Înainte de orice proces merge on-line, hazard și operabilitate (HAZOP) studii și strat de protecție analize (LOPAs) sunt efectuate. Progresele în simulatoarele de formare și practicile educaționale asigură că operatorii și inginerii își pot îndeplini sarcinile în siguranță și eficient.,acestea sunt doar câteva dintre miile de îmbunătățiri ale tehnologiei și siguranței care au fost implementate pentru a face din industria amoniacului una dintre cele mai productive și mai sigure industrii din lume.autorii recunosc asistența oferită de KBR, ThyssenKrupp Industrial Solutions, Haldor Topsøe, Linde și Casale pentru furnizarea de literatură tehnică privind tehnologiile de proces respective.