Ammoniakk er svært viktig i produksjon av gjødsel, og er en av de største volumet syntetiske kjemikalier som produseres i verden. Denne artikkelen utforsker utviklingen av ammoniakk produksjon og beskriver dagens produksjon teknologier.
de Fleste mennesker forbinder den stikkende lukten av ammoniakk (NH3) med rengjøringsmidler eller lukter salter. Men, bruk av ammoniakk i disse to produktene representerer bare en liten del av de totale globale ammoniakk produksjon, som var rundt 176 millioner tonn i 2014 (1)., Å sette pris på hvor industrien og teknologien er i dag, la oss først ta en titt på hvordan vi kom hit.
Ammoniakk har vært kjent i mer enn 200 år. Joseph Priestley, en engelsk kjemiker, først isolert i gassform ammoniakk i 1774. Komposisjonen ble konstatert av franske kjemiker Claude-Louis Berthollet i 1785., I 1898, Adolph Frank og Nikodem Caro fant at N2 kan bli løst av kalsium-karbid for å danne kalsium cyanamide, som kan deretter bli hydrolysert med vann og danner ammoniakk (2):
CaO + 3C ↔ CaC2 + CO
CaC2 + N2 ↔ CaCN2 + C
CaCN2 + 3H2O ↔ CaCO3 + 2NH3
produksjon av betydelige mengder ammoniakk ved hjelp av cyanamide prosessen ikke skje før tidlig i det 20. århundre. Fordi denne prosessen som kreves store mengder energi, forskere fokusert sin innsats på å redusere energibehovet.,
tysk kjemiker Fritz Haber utført noen av de viktigste arbeid i utviklingen av den moderne ammoniakk bransjen. Arbeider med en student ved Univ. i Karlsruhe, han syntetisert ammoniakk i laboratoriet fra N2 og H2.
i Mellomtiden, Walther Nernst, en professor i fysisk kjemi ved Univ. av Berlin, utviklet en prosess for å lage ammoniakk ved å sende en blanding av N2 og H2 over strykejern katalysator på 1,000°C og 75 barg press. Han var i stand til å produsere større mengder av ammoniakk på dette press enn tidligere eksperimenter ved Haber og andre ved atmosfærisk trykk., Imidlertid, Nernst konkluderte med at prosessen ikke var mulig fordi det var vanskelig eller nesten umulig (på den tiden) til å produsere store utstyr som er i stand til å operere på at press.
Likevel, både Haber og Nernst forfulgt høytrykks-ruten til å produsere ammoniakk over en katalysator. Haber endelig utviklet en prosess for produksjon av kommersielle mengder ammoniakk, og i 1906 ble han i stand til å oppnå en 6% ammoniakk konsentrasjon i en reaktor som er lagt med en osmium katalysator., Dette er generelt anerkjent som et vendepunkt i utviklingen av en praktisk prosess for produksjon av ammoniakk i kommersielle mengder.
Haber innså at mengden av ammoniakk dannes i en enkelt passere gjennom en omformer var altfor lav til å være av kommersiell interesse. For å produsere mer ammoniakk fra makeup gass, han foreslo en resirkulere system, og fikk patent på konseptet. Haber er resirkulere idé endret oppfatningen av prosessen engineering as statisk i favør av en mer dynamisk tilnærming., I tillegg til den kjemiske reaksjonen likevekt, Haber anerkjent som reaksjon pris var en avgjørende faktor. I stedet for enkle avkastning i en en-gang-gjennom prosessen, konsentrerte han seg på plass-tid avkastning i et system med resirkulering.
BASF kjøpt Haber er patenter og startet utvikling av en kommersiell prosess. Etter å ha testet mer enn 2500 ulike katalysatorer, Carl Bosch, Alvin Mittasch, og andre BASF kjemikere utviklet en forfremmet strykejern katalysator for produksjon av ammoniakk i 1910., Å utvikle utstyr som kan tåle de nødvendige høye temperaturer og trykk, var en enda vanskeligere oppgave. En tidlig lakkert stål reaktoren varte bare 80 timer før feil på grunn av decarbonization. Fôr lakkert stål reaktorer med myk jern (som ikke var utsatt for decarbonization) og legge til spor mellom de to liners å frigjøre hydrogen som hadde spredt gjennom myk jern liner løst dette problemet., Andre store utfordringer er inkludert designe en varmeveksler for å bringe innløp gass til reaksjon temperaturer og kule avslutt gass, og å utarbeide en metode for å bringe katalysator til reaksjon temperatur.
Den første kommersielle ammoniakk anlegg basert på Haber-Bosch-prosessen ble bygget av BASF i Oppau, Tyskland. Anlegget gikk i produksjon i September. 9, 1913, med en produksjonskapasitet på 30 m.t./dagen.
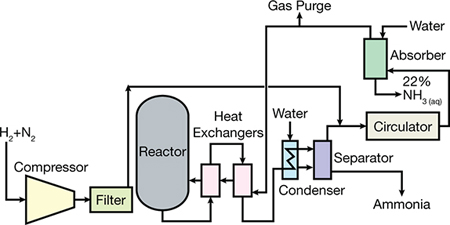
▲Figur 1. Dette er en forenklet flowsheet av de første kommersielle ammoniakk anlegg av BASF.,
Figur 1 er en flowsheet av de første kommersielle ammoniakk anlegg. Reaktoren inneholdt en intern varmeveksler i tillegg til de som er vist på illustrasjon.
Globale produksjonen priser
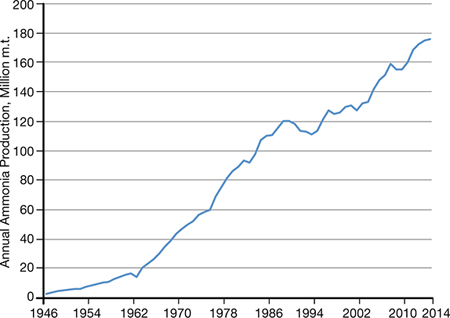
▲Figur 2. Over hele verden ammoniakk produksjon har stadig økt fra 1946 til 2014.
Ammoniakk produksjon har blitt en av de viktigste næringene i verden. Uten crop yield gjort mulig av ammoniakk-basert gjødsel og kjemikalier, den globale befolkningen ville være minst to til tre milliarder kroner mindre enn det er i dag (3)., Ammoniakk produksjon har økt jevnt siden 1946 (Figur 2), og det er anslått at den årlige produksjonen av ammoniakk er verdt mer enn $100 milliarder kroner, med noen planter som produserer mer enn 3000 meter.t./dag av NH3.
I 1983, i anledning 75-årsjubileet av AIChE grunnleggelsen, en blå sløyfe panel av anerkjente kjemiske ingeniører som heter hva de antas å være verdens ti største kjemisk prosessteknologi prestasjoner (4)., Omfavner slike bragder som lurer på medisiner, syntetiske fibre, og atomic energy, stevningen også inkludert gjennombruddet som er tillatt produksjon av store mengder ammoniakk i kompakt, enkel-enhet planter.
i Løpet av de siste tiårene, kjemiske ingeniører har lykkes i å skape prosesser som gjør store mengder ammoniakk ved relativt lave kostnader. Så nylig som for 80 år siden, den totale årlige produksjonen av syntetisk ammoniakk var like over 300 000 m.t. Takk for kjemisk prosessteknologi gjennombrudd, en moderne ammoniakk anlegget kan produsere mer enn 750,000 m.t./yr.,
Omtrent 88% av ammoniakk gjøres årlig forbrukes i produksjon av gjødsel. Mesteparten av resten går til produksjon av formaldehyd. Kina produserte om 32.6% av den globale produksjonen i 2014, mens Russland, India og USA produsert 8.1%, 7.6%, og 6.4%, henholdsvis (1). Mens det meste av den globale produksjonen av ammoniakk er basert på damp reformering av naturgass, betydelige mengder er produsert av kull gassifisering; de fleste av gassifisering planter er lokalisert i Kina.,
Moderne produksjonsprosesser
Den enorme økningen i ammoniakk etterspørsel fra 1950 til 1980 hadde behov for større, mer energieffektive anlegg. De tiårene har også sett en endring i design-filosofi. Inntil den tid, en ammoniakk anlegget ble ansett som en sammenstilling av ikke-relaterte enheter, for eksempel gass forberedelse, gass-rensing, gasskompresjon, og ammoniakk syntese. Nye innovasjoner og en integrert design knyttet prosessen enheter sammen på den mest effektive og effektive måter.
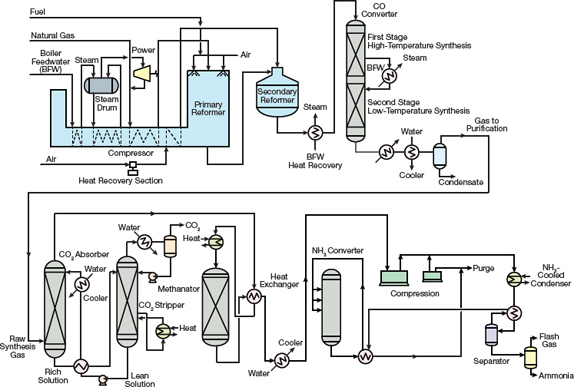
▲Figur 3., KBR utformet en av de første single-tog, stor kapasitet ammoniakk planter.
I midten av 1960-tallet, American Oil Co. installert en enkelt-converter ammoniakk anlegg konstruert av M. W. Kellogg (MWK) i Texas City, TX, med en kapasitet på 544 m.t./dagen. Single-tog design-konsept (Figur 3) var så revolusjonerende at det fikk Kirkpatrick Kjemisk prosessteknologi Achievement Award i 1967.,
anlegget brukes en fire-sak sentrifugal kompressor til å komprimere syngas til et trykk på 152 bar, og siste komprimering til et arbeidstrykk på 324 bar skjedde i en vekselvirkende kompressor. Sentrifugal kompressorer for syntese loop og kjøling tjenester ble også innført, som ga betydelige kostnadsbesparelser.,
Det viktige forskjeller mellom MWK prosessen og prosessene som brukes i forrige ammoniakk inkludert planter:
- ved hjelp av en sentrifugal kompressor som en del av syntese gass komprimering
- maksimere utvinning av overskuddsvarme fra process
- generere damp fra varme for bruk i dampturbin drivere
- ved hjelp av kjøle-kompressor for oversikt og atmosfæriske kjøling.
En integrert ordning som balansert energibruk, energiproduksjon, utstyr størrelse, og katalysator volumer ble stiftet i hele anlegget.,
de Fleste planter bygget mellom 1963 og 1993 hadde store enkelt-tog design med syntese gass produksjonen på 25-35 bar og ammoniakk syntese på 150-200 bar. En annen variant av Braun (nå KBR) tilbys små modifikasjoner til den grunnleggende design. Braun Purifier prosessen planter brukt en primær eller rørformet reformator med en lav outlet temperatur og høy metan lekkasje til å redusere størrelsen og prisen på reformatoren. Overflødig luft ble lagt til den sekundære reformer for å redusere metan innhold av primære reformator avslutt stream til 1-2%., Overflødig nitrogen og andre urenheter ble fjernet nedstrøms av methanator. Fordi syntese gass som i hovedsak var fri for urenheter, to axial flow ammoniakk omformere ble brukt til å oppnå en høy ammoniakk konvertering.
Noen nylig bygget planter har en syntese gass generasjons system med bare en reformator (ingen sekundær reformatoren), en trykk-swing adsorption (PSA) system for H2 utvinning, og en luft-separasjon anlegg som kilde til N2., Forbedringer i converter design, som for eksempel radial og horisontal katalysator senger, interne varmevekslere, og syntese gass behandling, bidro til å øke ammoniakk-konsentrasjoner spennende syntese converter fra ca 12% til 19-21%. En høyere konvertering per pass, sammen med mer effektive turbiner og kompressorer, ytterligere redusert energiforbruk. Mer effektiv CO2-fjerning løsninger, som for eksempel kalium karbonat og methyldiethanolamine (MDEA), har bidratt til bedre energi-effektivitet. Mest moderne anlegg kan produsere ammoniakk med et energiforbruk på 28 GJ/m.t.,
I tillegg til design, mekanisk, og metallurgiske forbedringer som er gjort i løpet av denne tiden, arbeidstrykket til syntese løkken ble betydelig redusert. Når den første single-tog anlegget ble bygget i 1960-årene, det finnes et høyt trykk syntese loop. I 1962, MWK mottatt en henvendelse fra Imperial Chemical Industries (ICI) for et forslag om å bygge et 544-m.t./dag-anlegget på deres Severnside nettstedet. MWK foreslått en 152-bar syntese løkke i stedet for en 324-bar-løkke.,
Fordi utvikling av kinetiske data for ammoniakk reaksjon på 152 bar ville ta mer tid enn MWK hadde å svare på ICI henvendelse, de kontaktet Haldor Topsøe til støtte for sine planer. Topsøe hadde data som dekker hele trykkområdet av interesse for MWK. I tillegg hadde de et dataprogram for beregning av mengde katalysator som var nødvendig i den nedre driftstrykk. Selv om ICI valgte Bechtel å utforme anlegget, MWK var i stand til å utvikle en flowsheet for en 544-m.t.,/dag design med sentrifugal kompressorer og et lavt trykk syntese loop, som noen mennesker vurdere den viktigste begivenheten i utviklingen av single-tog ammoniakk anlegg.
Omtrent dobbelt så mye catalyst var nødvendig på 152 bar som på 324 bar, en økning som var økonomisk mulig. Selv om det converter trenger du to ganger på volum, lavere driftstrykk ville redusere den nødvendige tykkelsen av trykket shell. Som et resultat, vekten av metall som kreves for converter plus katalysator vært omtrent den samme., Nedre-press-syntese loop også tillates bruk av sentrifugal kompressorer i stedet for frem-og tilbakegående kompressorer. En annen forbedring var utvinne varme for å generere høytrykks damp for dampturbin-stasjoner.
Plant design i det 21. århundre
i Løpet av de første årene av det 21. århundre, mange forbedringer ble gjort i ammoniakk plante-teknologi som tillater eksisterende anlegg for å øke produksjonen priser og nye anlegg bygges med større og større kapasitet. Konkurranse mellom teknologi leverandører er ganske hard., Tre-teknologi lisensgivere — KBR (Kellogg Brown og Rot), Haldor Topsøe, og ThyssenKrupp Industrielle Løsninger (TKIS) — som i dag dominerer markedet. Ammoniakk Casale, som tilbyr en aksial-radial katalysator bed design, er en markedsleder i revamps av eksisterende anlegg.
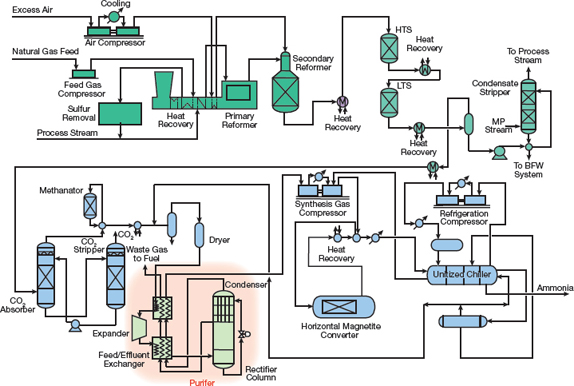
▲Figur 4. Moderne ammoniakk planter designet av KBR ansette sin proprietære Purifier design.,
de Fleste av ammoniakk planter nylig designet av KBR utnytte sin Purifier prosessen (Figur 4), som kombinerer lav alvorlighetsgrad fornyelse i den primære reformator, en flytende N2 vask purifier nedstrøms av methanator for å fjerne urenheter og justere H2:N2 forholdet, en proprietær avfall-varme kjelen design, en unitized chiller, og en horisontal ammoniakk syntese converter.
Avhengig av konfigurasjonen av anlegget, energiforbruk kan være så lav som 28 GJ/m.t. Fordi det sekundære reformator bruker overflødig luft, er den primære reformator kan være mindre enn i konvensjonell design., Den kryogeniske purifier (vist i Figur 4 i lys grønn med en lys oransje bakgrunn), som består av en expander, kondensator, feed/avløpsvann varmeveksler, og likeretter-kolonnen, fjerner urenheter, slik som CO, CH4, og argon fra syntese gass mens du justere H2:N2 forholdet mellom makeup gass i ammoniakk-løkke til det optimale nivå. Den ammoniakk konsentrasjon spennende lav-press-slipp-horizontal converter er 20-21%, noe som reduserer energibehovet for resirkulering av kompressoren., KBR har også en lav-trykk ammoniakk sløyfe som benytter en kombinasjon av magnetitt katalysator og sin proprietære ruthenium katalysator.
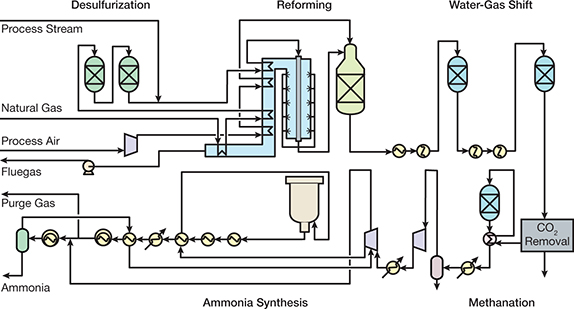
▲Figur 5. Haldor Topsøe tilbyr en ammoniakk plant design som har en egen side-avfyrt reformator i hvilken strålende brennere leverer varme for å reformere reaksjon.
syngas generasjon delen (eller front end) av en Haldor Topsøe-designet plante (Figur 5) er ganske tradisjonell med unntak av sin proprietære side avfyrt reformator, som bruker strålende brennere til å levere varme for å reformere reaksjon., Haldor Topsøe tilbyr også en proprietær jern-basert katalysator syntese, radial-flow-omformere som består av ett, to eller tre senger, og en proprietær bajonett-tube-avfall-varme kjelen. Nyere utviklingen omfatter S-300 og S-350 converter design. S-300 converter er en tre-seng radial-flow konfigurasjon med interne varmevekslere, mens S-350 design kombinerer en S-300 converter med en S-50 med enkeltseng design med avfall-varmegjenvinning mellom omformere for å maksimere ammoniakk konvertering.
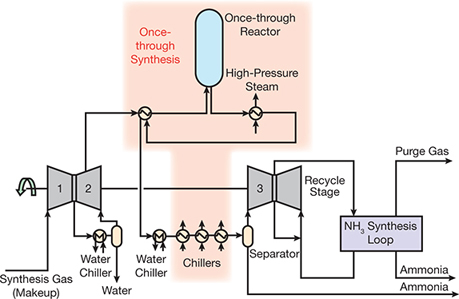
▲Figur 6., ThyssenKrupp dual-press-syntese loop design har en en-gang-gjennom reaktoren mellom syngas kompressorer.
ThyssenKrupp tilbyr en vanlig plante (Figur 6) med en unik videregående reformator design, en proprietær avfall-varme kjelen, radial-flow omformere, og en dual-press ammoniakk syntese loop. I dag, en produksjonsrate på 3,300 m.t./dagen kan oppnås ved hjelp av den TKIS dual-press-prosessen.
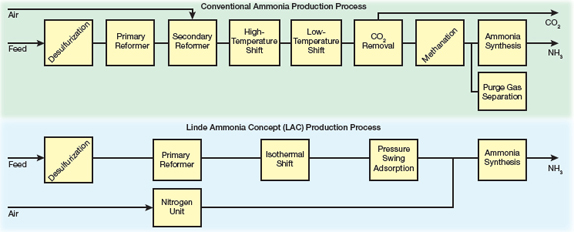
▲Figur 7., Det Linde Ammoniakk-Konseptet (LAC) har en trykk-swing adsorption enhet for høy renhet hydrogen produksjon og en luft-separasjon enhet for høy renhet nitrogen produksjon.
The Linde Ammoniakk-Konseptet (LAC) er en etablert teknologi prosessen ordningen med over 25 års drift erfaring i anlegg med kapasitet fra 200 m.t./dag til over 1,750 m.t./dagen., Den LAC prosessen ordningen (Figur 7) erstatter den kostbare og komplekse fremre enden av en konvensjonell ammoniakk anlegg med to velprøvde, pålitelige prosessen enheter:
- produksjon av ultra-høy renhet hydrogen fra en steam-metan reformator med PSA rensing
- produksjon av ultra-høy renhet nitrogen ved en kryogeniske nitrogen generasjon enhet, også kjent som en luft-separasjon enhet (ASU).
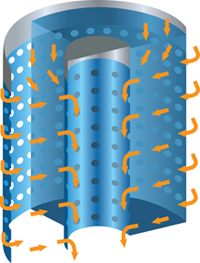
▲Figur 8., Ammoniakk Casale prosess benytter en katalysator seng som utnytter aksial-radial-teknologi, som har en lavere trykkfall og høyere effektivitet enn standard katalysator senger.
Ammoniakk Casale anlegg design har en produksjonsrate på 2000 meter.t./dagen. En av de viktigste funksjonene i denne design er aksial-radial teknologi i katalysatoren seng (Figur 8). I en aksial-radial katalysator seng, de fleste av syntese gass passerer gjennom katalysator seng i radiell retning, og skaper et svært lavt trykkfall., Resten av gassen som går ned gjennom et øvre lag av katalysator i en aksial retning, noe som eliminerer behovet for en toppdekselet på katalysatoren seng. Casale er aksial-radial katalysator bed-teknologi brukes i både høy temperatur og lav temperatur skift omformere, samt i syntese converter.
Andre teknologier
Noen-teknologi leverandører har tilbudt gass-oppvarmet reformatorene (GHRs) for produksjon av ammoniakk i liten kapasitet planter eller for kapasitet øker., I motsetning til konvensjonelt konstruert planter som bruker en primær reformator og videregående reformator som opererer i serien, planter med GHRs bruk varmt behandle gass fra videregående reformatoren til å levere varme til den primære reformator. Dette reduserer størrelsen på den primære reformator og reduserer CO2-utslipp fra den primære reformator stabel, noe som gjør prosessen mer miljøvennlig.,
Selv om noen ammoniakk produsenter talsmann for distribuert produksjon av ammoniakk i små ammoniakk planter, de fleste bedrifter foretrekker å bygge store anlegg i nærheten billige råvarer kilder og transport produktet av skip, jernbane, eller rørledning til forbrukerne.
Ammoniakk fra kull
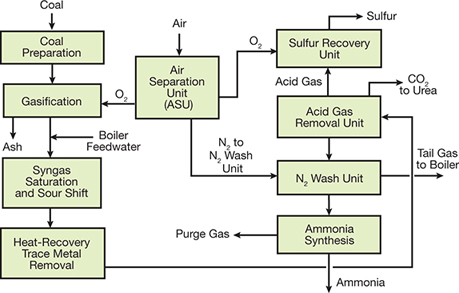
▲Figur 9. Kina produserer de fleste av sine ammoniakk fra kull.
Kina produserer mer ammoniakk enn noe annet land, og produserer de fleste av sine ammoniakk fra kull (Figur 9).,
Den grunnleggende behandlingen enheter i et kull-basert ammoniakk anlegget er det ASU for separasjon av O2 og N2 fra luften, gasifier, den sure gass-skift (SGS) enhet, syre gass fjerning enhet (AGRU) og ammoniakk syntese enhet. Oksygen fra ASU er matet til gasifier å konvertere kull i syntese gass (H2, CO, CO2) og CH4. Det er mange gasifier design, men de fleste moderne gasifiers er basert på fluidized senger som opererer over atmosfærisk trykk og evne til å benytte ulike kull-feeder. Avhengig av design, CO-nivåer av 30-60% av volumet kan være produsert.,
Etter gassifisering, noe svevestøv i syntese gass er fjernet og vanndamp er lagt til SGS enhet. SGS prosessen vanligvis benytter en kobolt og molybden (CoMo) katalysator som er spesielt utformet for bruk i en svovel miljø.
Etter å redusere CO-konsentrasjonen i syntese gass til mindre enn 1 vol%, er det syngas er matet til en AGRU, hvor en kald metanol skrubbe løsning (f.eks., Rectisol) fjerner CO2 og svovel fra syntese gass. CO2-overhead er enten luftet eller gitt til en urea-anlegg. Svovel outlet stream er matet til en svovel gjenopprette unit (SRU).,
Syngas som passerer gjennom AGRU er vanligvis renset ved en av to metoder:
- en nitrogen vask enheten for å fjerne rester av CO og CH4 fra syngas før det ledes til syntese loop
- en PSA-system for CO og CH4 fjerning.
Avsluttende tanker
i Løpet av de siste 60 år, ammoniakk prosessen teknologi har forbedret seg drastisk. Anlegget oppsett utviklet seg fra multi-tog design, ofte med forskjellige antall tog i fronten og syntese loop, for å enkelt-tog design., Syntese gass forberedelse i forkant av anlegget økt fra atmosfærisk trykk for å 30-50 barg press. Økt kapasitet fra 100 m.t./dag til så mye som 3,300 m.t./dagen i et enkelt tog.
Energi-effektiviteten har økt så godt fra forbruket til godt over 60 GJ/m.t. av ammoniakk i cola-anlegg basert på å 40-50 GJ/m.t. i den første naturlige-gass-anlegg basert på å 30-40 GJ/m.t. i den første single-tog planter. Moderne anlegg har lagt til varmegjenvinning av dampproduksjon på presset så høyt som 125 barg i både syngas forberedelse delen og syntese loop.,
I form av prosess utstyr, det har vært et skifte fra vekselvirkende kompressorer til sentrifugal kompressorer. En intern varmeveksler har blitt implementert i syntese converter for å øke konvertering av H2 og N2 å NH3. Designere har banket inn hydrogen utvinning fra purge gass (i enheter, for eksempel PSA-systemer) for å øke produksjonen eller redusere anlegget energiforbruk. Designerne har også implementert varmt fôr gass desulfurization systemer. Det har vært betydelige forbedringer i katalysatorer brukt i å reformere, skift konvertering, methanation, og ammoniakk syntese.,
for Å forbedre prosessen kontroll og sikkerhet, distribuert kontroll systemer (DCSs) for avansert prosesskontroll, samt sikkerhet-instrumenterte systemer (SISs), er nå standard i ammoniakk planter. Før prosessen går online, hazard og anvendbarhet (HAZOP) studier og lag av beskyttelse analyser (LOPAs) er utført. Fremskritt simulatorer i opplæring og utdanning, praksis sikre at operatører og ingeniører kan utføre sine oppgaver på en sikker og effektiv måte.,
Dette er bare noen av de tusenvis av forbedringer i teknologi og sikkerhet som har vært iverksatt for å gjøre ammoniakk industrien en av de mest produktive og trygt industriene i verden.
Erkjennelsene
forfatterne erkjenner hjelp av KBR, ThyssenKrupp Industrielle Løsninger, Haldor Topsøe, Linde, og Casale for å gi teknisk litteratur på sine respektive prosess teknologier.