アンモニアは肥料の製造において重要であり、世界最大の合成化学物質の一つである。 この記事では、アンモニア生産の進化を探り、現在の製造技術について説明します。
ほとんどの人は、アンモニア(NH3)の刺激臭を洗剤または臭いのある塩と関連付けます。 しかし、これら二つの製品におけるアンモニアの使用は、世界のアンモニア生産量のほんの一部に過ぎず、約176万トンであった2014年(1)。, 産業と技術が今日どこにあるかを理解するために、まずここに来た方法を見てみましょう。
アンモニアは200年以上にわたって知られています。 イギリスの化学者ジョセフ-プリーストリーが1774年に初めて気体状アンモニアを単離した。 その組成は1785年にフランスの化学者Claude Louis Bertholletによって確認されました。, 1898年、アドルフ-フランクとニコデム-カロは、N2を炭化カルシウムによって固定してシアナミドカルシウムを形成し、水で加水分解してアンモニアを形成することができることを発見した(2):
CaO+3C≤CaC2+CO
CaC2+N2≤CaCN2+C
CaCN2+3H2O≤CaCO3+2NH3
シアナミドプロセスを用いた大量のアンモニアの生成は20世紀初頭まで起こらなかった。 このプロセスは大量のエネルギーを必要とするため、科学者はエネルギー要件の削減に取り組んだ。,
ドイツの化学者Fritz Haberは、現代のアンモニア産業の発展において最も重要な仕事のいくつかを行った。 大学の学生と一緒に働いています。 カールスルーエのうち、彼はN2とH2から実験室でアンモニアを合成した。
一方、ヴァルターネルンスト、大学の物理化学の教授。 ベルリンの、N2およびH2の混合物を1,000°Cおよび75barg圧力で鉄の触媒を渡すことによってアンモニアを作るプロセスを開発しました。 彼は、大気圧でハーバーと他の人による以前の実験よりも、この圧力で大量のアンモニアを生成することができました。, しかし、ネルンストは、その圧力で動作できる大型機器を製造することは(当時)困難またはほとんど不可能であったため、プロセスは実現不可能であると結論付けました。
それにもかかわらず、ハーバーとネルンストの両方が触媒を介してアンモニアを生成するための高圧ルートを追求しました。 ハーバーは最終的に市販の量のアンモニアを製造するプロセスを開発し、1906年にオスミウム触媒を搭載した反応器で6%のアンモニア濃度を達成することができた。, これは一般に商業量のアンモニアの生産のための実用的なプロセスの開発の転換点として確認されます。
Haberは、コンバータを通過する単一パスで形成されるアンモニアの量が商業的に関心を持つにはあまりにも低いことに気付きました。 をアンモニアからの化粧ガス、その提案を有効活用するためのリサイクルシステム特許取得など、コンセプトです。 Haberのリサイクルアイデアは、より動的なアプローチを支持して静的としてプロセス工学の認識を変えました。, 化学反応平衡に加えて、ハーバーは反応速度が決定要因であることを認識した。 ワンスループロセスでの単純な歩留まりの代わりに、彼はリサイクルを持つシステムでの時空の収量に集中しました。
BASFはHaberの特許を購入し、商業プロセスの開発を開始しました。 2,500以上の異なる触媒を試験した後、Carl Bosch、Alvin Mittasch、および他のBASF化学者は、1910年にアンモニア製造のための促進鉄触媒を開発した。, 必要な高温高圧に耐える装置を開発することはさらに困難な作業でした。 初期の軟鋼原子炉は、脱炭素化による故障のわずか80時間前に続いた。 軟鋼反応器を軟鉄(脱炭素化に弱い)で覆い、軟鉄ライナーを通して拡散した水素を放出するために両ライナーの間に溝を追加することで、この問題を解決, その他の大きな課題としては、入口ガスを反応温度にして出口ガスを冷却する熱交換器の設計、触媒を反応温度にする方法の考案などがありました。
Haber-Boschプロセスに基づく最初の商業用アンモニアプラントは、ドイツのOppauにBASFによって建設されました。 この工場は月にオンストリームに行きました。 9、1913、30m.t./日の生産能力を持つ。
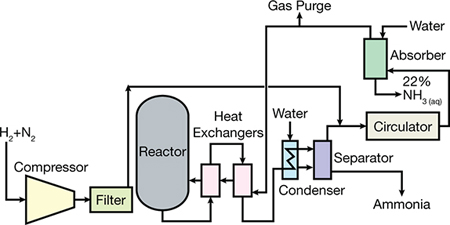
↑図1. これはBASFによる最初の商業アンモニア植物の簡単だったフローシートである。,
図1は、最初の市販アンモニアプラントのフローシートです。 反応器には回路図に示されているものに加えて内部熱交換器が含まれていました。
グローバル生産率
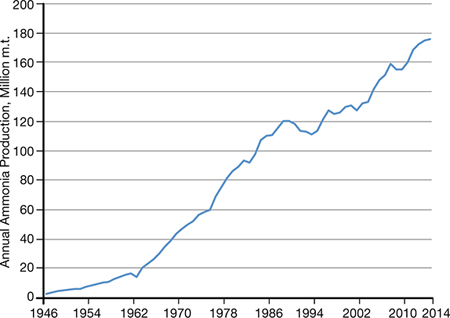
▲図2. 世界的なアンモニア生産量は1946年から2014年にかけて着実に増加している。
アンモニア生産は世界で最も重要な産業の一つとなっています。 アンモニアベースの肥料や化学物質によって可能になった作物収量がなければ、世界の人口は、それが今日(3)よりも少なくとも二から三億になります。, アンモニアの生産量は1946年(図2)以来着実に増加しており、アンモニアの年間生産量は100億ドル以上の価値があり、一部の工場では3,000m.t./日を超えるNH3を生産していると推定されている。
1983年、AIChEの創立75周年を機に、著名な化学技術者のブルーリボンパネルは、彼らが世界の十大化学工学の成果であると信じていたものを命名しました(4)。, ワンダードラッグ、合成繊維、原子力などの偉業を受け入れ、コンパクトな単一ユニットプラントで大量のアンモニアを生産することを可能にした画期的なものも含まれていました。
過去数十年の間に、化学エンジニアは比較的低コストで膨大な量のアンモニアを作るプロセスを作ることに成功しました。 最近80年前に、総合されたアンモニアの総年間生産は300,000m.t.に化学工学の進歩のおかげでちょうどありました、現代アンモニア植物は750,000m.t./yr,
毎年作られるアンモニアの約88%が肥料の製造に消費されています。 残りのほとんどはホルムアルデヒドの生産に入ります。 中国は世界の生産の約32.6%を生産し、2014年にはロシア、インド、米国はそれぞれ8.1%、7.6%、6.4%を生産しました(1)。 アンモニアの世界的な生産のほとんどは天然ガスの水蒸気改質に基づいていますが、石炭ガス化によってかなりの量が生産されています。,
現代の生産プロセス
1950年から1980年にかけてのアンモニア需要の大幅な増加は、より大きく、よりエネルギー効率の高いプラントを必要とした。 これらの数十年はまた、設計哲学の変化を見ました。 それまで、アンモニアプラントは、ガス調製、ガス精製、ガス圧縮、アンモニア合成などの無関係な単位の集合とみなされていました。 新しい革新および必要な設計は最も有効で、最も効率的な方法でプロセス単位を一緒に結んだ。
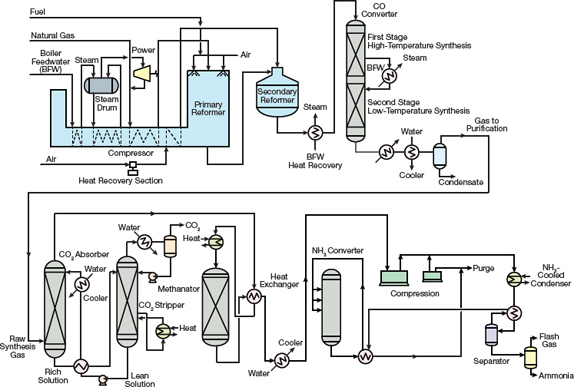
↑図3., KBRは、最初の単車、大容量のアンモニアプラントの一つを設計しました。
1960年代半ば、アメリカの石油株式会社。 M.W.Kellogg(MWK)によって設計されたシングルコンバーターアンモニアプラントをテキサス州テキサスシティに設置し、544m.t./日の容量を持つ。 シングルトレイン設計コンセプト(図3)は非常に革新的で、1967年にKirkpatrick Chemical Engineering Achievement Awardを受賞しました。,
プラントは、合成ガスを152バールの圧力に圧縮するために四ケース遠心圧縮機を使用し、往復圧縮機では324バールの動作圧力に最終圧縮が発生しました。 合成ループおよび冷凍サービス用の遠心圧縮機も実装され、大幅なコスト削減が可能になりました。,
MWKプロセスと以前のアンモニアプラントで使用されていたプロセスの主な違いは次のとおりです。
- 合成ガス圧縮の一部として遠心圧縮機を使用する
- プロセスからの廃熱回収を最大化する
- 蒸気タービンドライバに使用するための廃熱から蒸気を生成する
- ランダウンおよび大気冷凍のための冷凍圧縮機を使用する。
エネルギー消費、エネルギー生産、設備サイズ、触媒量のバランスをとった統合スキームがプラント全体に組み込まれました。,
1963年から1993年にかけて建設されたほとんどの工場では、合成ガス生産が25-35バール、アンモニア合成が150-200バールである大規模な単列車設計が行われていた。 もう一つの変化によるブラウン(KBRキャンパスにおいて、若干の変更、基礎デザイン。 Braunの清浄器の製造プラントは改質器のサイズそしてコストを削減するのに低い出口の温度および高いメタンの漏出が付いている第一次か管状の改 余分な空気は1-2%に一次改質器の出口の流れのメタンの内容を減らすために二次改質器に加えられました。, 過剰の窒素および他の不純物をメタネータの下流で除去した。 合成ガスは本質的に不純物を含まないため,二つの軸流アンモニア転化器を用いて高いアンモニア転化を達成した。
最近建てられたいくつかのプラントには、一つの改質器(二次改質器なし)、H2回収のための圧力スイング吸着(PSA)システム、N2の供給源としての空気分離プラントのみを備えた合成ガス発生システムがある。, ラジアルおよび水平触媒床、内部熱交換器、合成ガス処理などのコンバータ設計の改善により、合成コンバータから出るアンモニア濃度が約12%から19-21%に より高い変換お通い、より効率の高いタービンやコンプレッサーがさらに低エネルギーを消費する。 炭酸カリウムやメチルジエタノールアミン(MDEA)などのより効率的なCO2除去ソリューションは、エネルギー効率の向上に貢献しています。 ほとんどの現代植物は28GJ/m.tのエネルギー消費のアンモニアを作り出すことができます。,
この間に行われた設計、機械、および冶金の改善に加えて、合成ループの動作圧力が大幅に低下しました。 1960年代に最初の単車工場が建設されたとき、それは高圧の合成ループを含んでいた。 1962年、MWKはインペリアル-ケミカル-インダストリーズ(Ici)から、セバーンサイド-サイトに544m.t./dayプラントを建設する提案を受けた。 MWKは152バールの合成ループの代わりに324バールの合成ループを提案した。,
152バールでのアンモニア反応の速度論的データの開発は、MWKがICIの問い合わせに応答しなければならなかったよりも時間がかかるため、彼らはHaldor Topsøeに連絡し、彼らの計画を支援した。 TopsøeはMWKに関心のある全圧力範囲をカバーするデータを持っていました。 さらに、彼らはより低い操作圧力で必要とされた触媒の量を計算するためのコンピュータプログラムを持っていた。 ICIがベクテルを選んでプラントを設計したにもかかわらず、MWKは544-m.tのフローシートを開発することができました。,/一部の人々は、単一列車アンモニアプラントの開発において単一の最も重要なイベントを考慮する遠心圧縮機と低圧合成ループを用いたデザイン。
およそ倍の触媒が152バールで324バール、経済的に実現可能と思われる増加で必要とされました。 コンバーターが容積を二度必要とするが、より低い操作圧力は圧力貝の必須の厚さを減らします。 その結果、転炉に必要な金属の重量に触媒を加えた重量はほぼ同じままであった。, 低圧の統合のループはまた圧縮機を交換するかわりに遠心圧縮機の使用を可能にした。 もう一つの改善は、蒸気タービン駆動用の高圧蒸気を生成するための熱回収であった。
21世紀のプラント設計
21世紀の最初の数年間、アンモニアプラント技術において多くの改善が行われ、既存のプラントが生産量を増やし、新しいプラントをより大きな容量で建設することができた。 技術サプライヤー間の競争は非常に激しいです。, KBR(ケロッグ—ブラウンとルート)、Haldor Topsøe、ThyssenKrupp Industrial Solutions(TKIS)の三つの技術ライセンサーが現在市場を支配しています。 軸放射状の触媒のベッドの設計を提供するアンモナルCasaleは既存の植物のrevampsの主導株である。
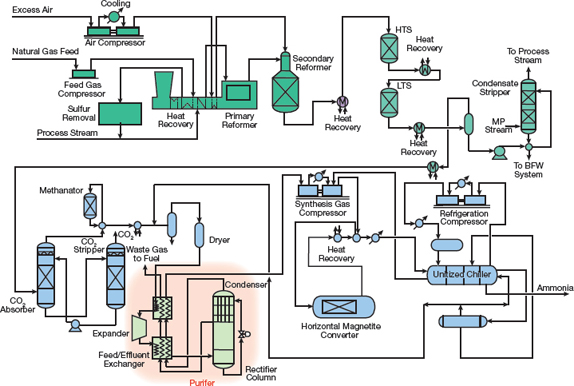
↑図4. 現代アンモニア工場の設計によるKBRの採用、独自の清浄機設計です。,
KBRによって最近設計されたアンモニアプラントのほとんどは、一次改質器における低重大改質、メタネータの下流にある液体N2洗浄清浄器、H2:N2比、独自の廃熱ボイラ設計、ユニット化されたチラー、水平アンモニア合成コンバータを組み合わせた清浄器プロセスを利用している(図4)。
プラントの構成に応じて、エネルギー消費量は28GJ/m.tと低くすることができます。, エキスパンダー、コンデンサー、供給/排水交換器、および整流器カラムからなる極低温清浄器(図4に薄緑、薄いオレンジ色の背景で示されている)は、アンモニアループ内のメイクアップガスのH2:N2比を最適なレベルに調整しながら、合成ガスからCO、CH4、アルゴンなどの不純物を除去する。 アンモニア濃度は20-21%であり、リサイクルコンプレッサーのエネルギー要件を低減している。, KBRはまた磁鉄鉱の触媒および専有ルテニウムの触媒の組合せを用いる低圧のアンモニアループを提供する。
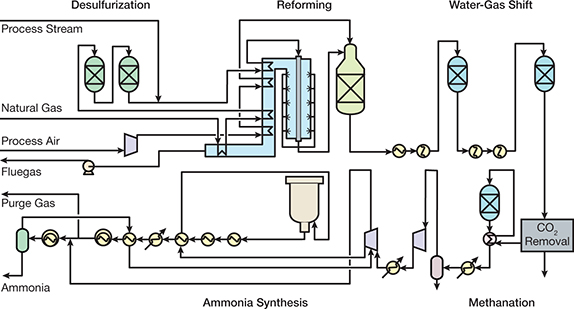
↑図5. Haldor Topsøeは放射バーナーが改良の反作用のための熱を供給する専有側面発射された改質器があるアンモナルプラント設計を提供する。
Haldor Topsøeが設計したプラント(図5)の合成ガス生成セクション(またはフロントエンド)は、放射バーナーを使用して改質反応のための熱を供給する独自のサイド, Haldor Topsøeはまた専有鉄ベースの統合の触媒、一つ、二つ、または三つのベッドから成っている放射状流れのコンバーターおよび専有銃剣管の不用な熱ボイラーを提供する。 より最近の開発はS-300およびS-350コンバーターの設計を含んでいる。 S-300コンバータは内部熱交換器を備えたスリーベッドラジアルフロー構成であり、S-350設計はS-300コンバータとs-50シングルベッド設計を組み合わせて、アンモニア変換を最大にするコンバータ間の廃熱回収を実現している。
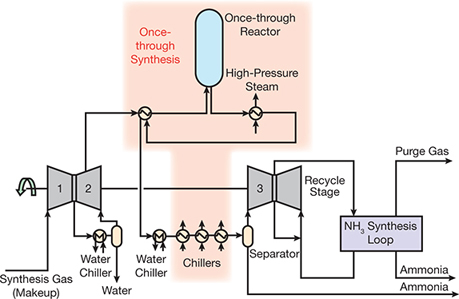
▲図6., ティッセンクルップの二重圧力合成ループ設計は、合成ガスコンプレッサー間のワンスルーリアクターを特徴としています。
ThyssenKruppは、独自の二次改質器設計、独自の廃熱ボイラ、ラジアルフローコンバータ、および二重圧力アンモニア合成ループを備えた従来のプラント(図6)を提供し 今日、3,300m.t./dayの生産率をTKISの二重圧力プロセスを使用して達成することができる。
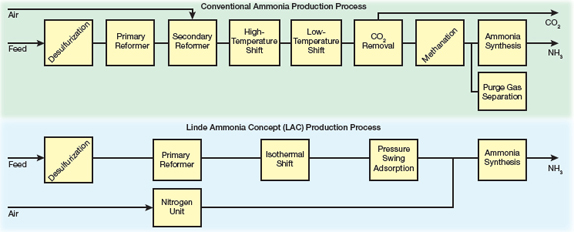
▲図7., リンデアンモナル概念(LAC)は高純度の水素の生産のための圧力振動吸着単位および高純度窒素の生産のための空気分離の単位を特色にする。
リンデアンモニア概念(LAC)はにわたる25年間の200m.t./日からの1,750m.t./日に容量の植物の操作経験の確立された技術プロセス機構である。, LACプロセススキーム(図7)は、従来のアンモニアプラントの高価で複雑なフロントエンドを、PSA精製による蒸気-メタン改質器からの超高純度水素の製造
- 空気分離ユニット(ASU)としても知られる極低温窒素生成ユニットによる超高純度窒素の製造で置き換えるものである。
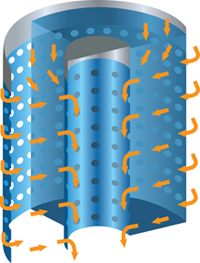
↑図8., アンモナルCasaleのプロセスは標準的な触媒のベッドより低い圧力降下そして高性能がある、軸放射状の技術を利用する触媒のベッドを用いる。
アンモニアCasaleのプラント設計に2,000m.t./dayの生産率があります。 この設計の主な特徴の一つは、触媒床における軸-半径方向の技術です(図8)。 軸方向半径方向触媒床では、合成ガスの大部分が半径方向に触媒床を通過し、非常に低い圧力降下を生じる。, ガスの残りは触媒のベッドのトップ-カバーのための必要性を除去する軸方向の触媒の最上層を通って渡る。 Casaleの軸放射状の触媒のベッドの技術は高温および低温の転位のコンバーターで、また統合のコンバーターで使用される。
その他の技術
一部の技術サプライヤーは、小容量プラントでのアンモニア製造または容量増加のためにガス加熱改質器(Ghr)を提供しています。, 従来設計されていた一次改質器と二次改質器を直列に運転するプラントとは異なり、GHRsを備えたプラントは、二次改質器からのホットプロセスガスを使用して一次改質器に熱を供給する。 これにより、一次改質器のサイズを縮小し、一次改質器スタックからのCO2排出量を排除し、プロセスをより環境に優しくします。,
一部のアンモニア生産者は、小さなアンモニア工場でのアンモニアの分散生産を提唱しているにもかかわらず、ほとんどの企業は、安価な原料源の近くに大きな施設を建設し、船、鉄道、またはパイプラインで消費者に製品を輸送することを好む。
石炭からのアンモニア
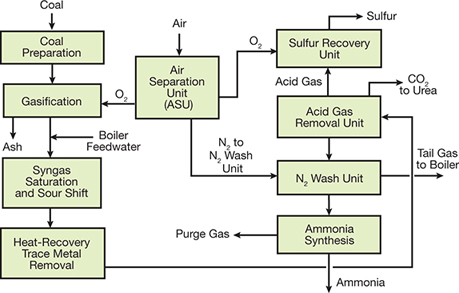
▲図9. 中国は石炭からアンモニアの大部分を生産している。
中国は他のどの国よりも多くのアンモニアを生産し、そのアンモニアの大部分を石炭から生産しています(図9)。,
石炭ベースのアンモニア植物の基本的な処理装置は空気からのO2そしてN2の分離のためのASU、ガス化炉、酸っぱいガスの転位(SGS)の単位、酸ガスの取り外しの単位(AGRU)およびアンモニア統合の単位である。 ASUからの酸素は、石炭を合成ガス(H2、CO、CO2)およびCH4に変換するためにガス化炉に供給される。 多くのガス化炉の設計がありますが、現代のほとんどのガス化炉は、大気圧以上で動作し、異なる石炭供給を利用する能力を有する流動床に基づい 設計によって、容積によって30-60%のCOのレベルは作り出されるかもしれません。,
ガス化後、合成ガス中の粒子状物質が除去され、蒸気がSGSユニットに添加される。 SGSプロセスは、通常、硫黄環境での運転のために特別に設計されたコバルトおよびモリブデン(CoMo)触媒を利用します。
合成ガス中のCO濃度を1vol%未満に低下させた後、合成ガスをAGRUに供給し、冷却されたメタノールスクラブ溶液(例えば、レクチゾール)が合成ガスからCO2と硫黄 CO2オーバーヘッドは、尿素プラントに通気または供給されます。 硫黄出口流は、硫黄回収ユニット(SRU)に供給される。,合成ループに供給される前に、合成ガスから残留COおよびCH4を除去するための窒素洗浄ユニット
AGRUを通過する合成ガスは、典型的には、二つの方法のいずれかによって精製される。
- 合成ガスから残留COおよびCH4を除去するための窒素洗浄ユニット
閉じる考え
過去60年間、アンモニアプロセス技術は大幅に改善されました。 プラントレイアウトは、多くの場合、フロントエンドと合成ループに異なる数の列車を持つ複数の列車の設計から、単一の列車の設計に進化しました。, プラントのフロントエンドにおける合成ガス調製は、大気圧から30-50バーグ圧力に増加した。 容量は100m.t./日から単一の列車で3,300m.t./日に増加しました。
エネルギー効率は、コークスベースの植物におけるアンモニアの60GJ/m.t.をはるかに上回る消費から、最初の天然ガスベースの植物における40—50GJ/m.t.への30-40GJ/m.t.への最初のシングルトレインプラントにおけるエネルギー効率も改善されている。 現代植物は合成ガスの準備セクションおよび統合のループ両方の125barg高い圧力で蒸気の生産によって熱回復を加えた。,
プロセス機器に関しては、往復圧縮機から遠心圧縮機へのシフトがありました。 内部熱交換器は統合のコンバーターでH2およびN2のNH3への転換を高めるために実行された。 デザイナーはタップ穴水素からの回復パージガス(ユニット増設などによるPSAシステムを充実させるために生産の工場のエネルギーを消費する。 設計者は、高温供給ガス脱硫システムも実装しています。 改質、シフト変換、メタン化、およびアンモニア合成に使用される触媒の大幅な改善が行われている。,
プロセス制御と安全性を改善するために、高度なプロセス制御のための分散制御システム(DCSs)と安全計装システム(SISs)は、アンモニアプラントで標準 どのプロセスでもオンラインになる前に、危険および操作性調査(HAZOP)および保護分析(LOPAs)の層は行われる。 術の訓練シミュレーター教育実践を事業者や技術者が業務を遂行する安全かつ有効である。,
これらは、アンモニア産業を世界で最も生産的で安全な産業の一つにするために実施された技術と安全性の何千もの改善のほんの一部です。
謝辞
著者らは、KBR、ThyssenKrupp Industrial Solutions、Haldor Topsøe、Linde、Casaleが、それぞれのプロセス技術に関する技術文献を提供するための支援を受けていることを認めています。