Ammoniakki on kriittinen valmistus lannoitteiden, ja on yksi suurimmista-tilavuus synteettisiä kemikaaleja tuotetaan maailmassa. Tässä artikkelissa tarkastellaan ammoniakin tuotannon kehitystä ja kuvataan nykyisiä valmistustekniikoita.
useimmat yhdistävät ammoniakin pistävän hajun (NH3) puhdistusaineisiin tai hajusuoloihin. Kuitenkin käyttää ammoniakkia nämä kaksi tuotetta on vain pieni murto-osa koko maailman ammoniakin tuotanto, joka oli noin 176 miljoonaa tonnia vuonna 2014 (1)., Jotta ymmärtäisimme, missä ala ja teknologia ovat tänään, katsotaan ensin, miten päädyimme tänne.
ammoniakkia on tunnettu jo yli 200 vuotta. Englantilainen kemisti Joseph Priestley eristi kaasumaisen ammoniakin ensimmäisen kerran vuonna 1774. Sen koostumuksen varmisti ranskalainen kemisti Claude Louis Berthollet vuonna 1785., Vuonna 1898 Adolf Frank ja Nikodem Caro todettiin, että N2 voisi olla kiinteä kalsiumkarbidia muodostaa kalsiumsyanamidia, joka voisi sitten olla hydrolysoitu veden kanssa muodostaen ammoniakkia (2):
CaO + 3C ↔ CaC2 + CO
CaC2 + N2 ↔ CaCN2 + C
CaCN2 + 3H2O ↔ CaCO3 + 2NH3
tuotannossa merkittäviä määriä ammoniakkia käyttäen syanamidi prosessi ei tapahdu, kunnes jo 20-luvulla. Koska tämä prosessi vaati suuria määriä energiaa, tutkijat keskittyivät vähentämään energiantarvetta.,
saksalainen kemisti Fritz Haber suorittaa joitakin tärkeitä työn kehittämisessä moderni ammoniakkia teollisuus. Opiskelen Univissa. Karlsruhesta hän syntetisoi laboratoriossa ammoniakkia N2: sta ja H2: sta.
samaan aikaan Univ: n fysikaalisen kemian professori Walther Nernst. Berliinistä kehitettiin prosessi ammoniakin valmistamiseksi kuljettamalla N2: n ja H2: n seos rautakatalyytin läpi 1 000°C: n ja 75 barg: n paineessa. Hän pystyi tuottamaan suurempia määriä ammoniakkia tällä paineella kuin aikaisemmin kokeiluja, joita Haber ja muut ilmakehän paineessa., Kuitenkin, Nernst päätellä, että prosessi ei ole toteuttamiskelpoinen, koska se oli vaikeaa tai lähes mahdotonta (tuolloin) tuottaa suuria laitteita, jotka pystyvät toimimaan paineen.
kuitenkin sekä Haber että Nernst jatkoivat korkeapaineista reittiä ammoniakin tuottamiseksi katalyytin yli. Haber nyt kehitetty prosessi tuottaa kaupallisia määriä ammoniakkia, ja vuonna 1906 hän oli saavuttaa 6% ammoniakin pitoisuus reaktorissa varustettu osmium katalysaattori., Tätä pidetään yleisesti käännekohtana kehitettäessä käytännöllistä prosessia ammoniakin tuottamiseksi kaupallisissa määrissä.
Haber tajusi, että määrä ammoniakkia muodostuu yhdessä läpi converter oli aivan liian alhainen olla kaupallista kiinnostusta. Tuottaa enemmän ammoniakki meikki kaasua, hän ehdotti kierrättää järjestelmä, ja sai patentin käsite. Haberin kierrätysidea muutti käsitystä prosessitekniikasta staattisena dynaamisemman lähestymistavan hyväksi., Kemiallisen reaktiotasapainon lisäksi Haber tunnusti reaktionopeuden olevan ratkaiseva tekijä. Yksinkertaisen tuoton sijaan kertaprosessissa hän keskittyi aika-avaruuden tuottoon järjestelmässä, jossa on kierrätystä.
BASF osti Haberin patentit ja aloitti kaupallisen prosessin kehittämisen. Testauksen jälkeen yli 2500 eri katalyyttejä, Carl Bosch, Alvin Mittasch, ja muut BASF kemistit kehittivät edistää raudan katalysaattorina ammoniakin tuotanto vuonna 1910., Vielä vaikeampi tehtävä oli kehittää laitteita, jotka kestäisivät tarvittavat korkeat lämpötilat ja paineet. Varhainen mieto teräsreaktori kesti vain 80 tuntia ennen hiilestä irtautumisen aiheuttamaa epäonnistumista. Vuori teräs reaktorit pehmeää rautaa (jota ei alttiita decarbonization) ja lisäämällä urien välillä vaipat vapauttaa vetyä, joka oli levinnyt kautta pehmeä rauta liner ratkaista tämä ongelma., Muita suuria haasteita mukana suunnittelussa lämmönvaihdin tuoda sisääntulokaasun reaktion lämpötila ja viileä ulos kaasua, ja suunnitella tapa tuoda katalysaattorin reaktion lämpötila.
ensimmäinen haber-Boschin prosessiin perustuva kaupallinen ammoniakkitehdas oli Basfin rakentama Oppaussa Saksassa. Tehdas aloitti toimintansa syyskuussa. 9, 1913, tuotantokapasiteetti 30 m. t. / vrk.
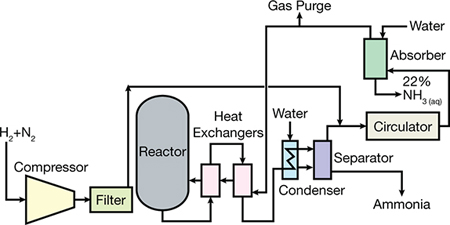
▲Kuva 1. Tämä on BASF: n ensimmäisen kaupallisen ammoniakkitehtaan yksinkertaistettu vuokaavio.,
kuva 1 on ensimmäisen kaupallisen ammoniakkilaitoksen flowsheet. Reaktorissa oli kaavamaisen lisäksi sisäinen lämmönvaihdin.
Maailmanlaajuinen tuotanto hinnat
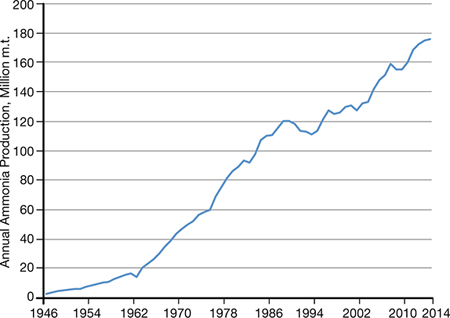
▲Kuva 2. Maailmanlaajuinen ammoniakin tuotanto on kasvanut tasaisesti vuodesta 1946 vuoteen 2014.
ammoniakin tuotannosta on tullut yksi maailman tärkeimmistä teollisuudenaloista. Ilman ammoniakkipohjaisten lannoitteiden ja kemikaalien mahdollistamaa satoa maapallon väestö olisi vähintään kahdesta kolmeen miljardia vähemmän kuin nykyään (3)., Ammoniakin tuotanto on kasvanut tasaisesti vuodesta 1946 (Kuva 2), ja on arvioitu, että vuotuinen tuotanto ammoniakki on arvoltaan yli $100 miljardia euroa, jossa on joitakin kasveja, jotka tuottavat enemmän kuin 3000 m.t./päivä NH3.
Vuonna 1983, kun 75 vuotta AIChE: n perustajajäsen, blue ribbon-paneeli erottaa kemialliset insinöörit nimeltä, mitä he uskoivat olevan maailman kymmenen suurimman kemian tekniikan saavutukset (4)., Syleilee kuten urotekoja kuten ihme huumeita, synteettiset kuidut, ja atomic energy, the citation myös läpimurto, joka saa tuotannon suuria määriä ammoniakkia kompakti, yhden yksikön kasveja.
viimeisen vuosikymmenen aikana, kemialliset insinöörit ovat onnistuneet luomaan prosesseja, jotka tekevät valtavia määriä ammoniakkia suhteellisen alhaiset kustannukset. Niinkin äskettäin kuin 80 vuotta sitten, vuotuinen tuotanto syntetisoitu ammoniakki oli vähän yli 300 000 m.t. Kiitos kemiantekniikan läpimurtoja, yksi moderni ammoniakkia kasvi voi tuottaa yli 750000 m.t./yr.,
noin 88% vuosittain valmistetusta ammoniakista kuluu lannoitteiden valmistuksessa. Suurin osa lopusta menee formaldehydin tuotantoon. Kiina tuotti noin 32,6% maailman tuotannosta vuonna 2014, kun taas Venäjä, Intia ja Yhdysvallat tuottivat 8,1%, 7,6% ja 6,4% (1). Vaikka useimmat maailmanlaajuinen ammoniakin tuotanto perustuu steam reformoimalla maakaasua, merkittäviä määriä tuotetaan hiilen kaasutus; useimmat kaasutus tehtaat sijaitsevat Kiinassa.,
nykyaikaiset tuotantoprosessit
ammoniakin kysynnän valtava kasvu vuosina 1950-1980 edellytti suurempia, energiatehokkaampia tehtaita. Noina vuosikymmeninä myös muotoilufilosofia muuttui. Siihen asti, ammoniakkia kasvi pidettiin kokoonpano liity yksiköt, kuten kaasu valmistelu, kaasun puhdistus, kaasun puristus, ja ammoniakin synteesi. Uudet innovaatiot ja integraali muotoilu sitoivat prosessiyksiköt yhteen tehokkaimmalla ja tehokkaimmalla tavalla.
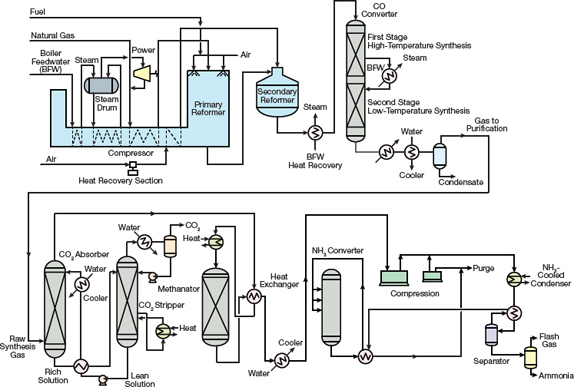
▲Kuva 3., KBR suunnitteli yhden ensimmäisistä yksijunaisista, suuren kapasiteetin ammoniakkitehtaista.
1960-luvun puolivälissä, American Oil Co. asennettu yhden muunnin ammoniakkitehdas suunnitellut M. W. Kellogg (MWK) Texas City, TX, kapasiteetti on 544 m.t./päivä. Yhden junan design-konsepti (Kuvio 3) oli niin mullistava, että se sai Kirkpatrick Chemical Engineering Achievement Award-palkinnon vuonna 1967.,
kasvi käytetään neljä-asia keskipako kompressori puristaa synteesikaasun painetta 152 bar, ja lopullinen pakkaus käyttöpaine 324 bar tapahtui edestakaisin kompressori. Myös synteesilenkki-ja kylmälaitteiden keskipakokompressorit otettiin käyttöön, mikä tuotti merkittäviä kustannussäästöjä.,
avain erot välillä MWK prosessi ja prosesseja, joita on käytetty aiemmissa ammoniakkia kasvien mukana:
- käyttää keskipako kompressori osana synteesikaasun pakkaus
- maksimoi hukkalämmön talteenoton prosessia
- tuottaa höyryä hukkalämmön käyttöä höyryturbiini ajurit
- käyttää jäähdytys-kompressori pilaantunut ja ilmakehän jäähdyttämiseen.
integroitu järjestelmä, jonka tasapainoinen energia-kulutus, energian tuotannon, laitteiden koko ja katalyytin tilavuutta on sisällytetty koko kasvi.,
Useimmat kasvit rakennettu vuosina 1963 ja 1993 oli suuri yhden-juna malleja synteesikaasun tuotanto 25-35 baari ja ammoniakin synteesi 150-200 bar. Toinen Braunin (nykyinen KBR) muunnelma tarjosi pieniä muutoksia perusmalliin. Braun Puhdistamot prosessi kasvit hyödyntää ensisijainen tai putkimainen uudistaja, joilla on alhainen pistorasiaan lämpötila ja korkea metaanin vuoto vähentää kokoa ja kustannuksia uudistaja. Ylimääräinen ilma oli lisätty toissijainen uudistaja vähentää metaanin pitoisuus ensisijainen uudistaja poistua stream 1-2%., Ylimääräinen typpi ja muut epäpuhtaudet poistuivat metanaattorin alajuoksulta. Koska synteesikaasun oli pääosin epäpuhtauksia, kaksi axial-flow-ammoniakki-muuntimet käytettiin saavuttaa korkea ammoniakin muuntaminen.
Jotkut hiljattain rakennettu kasvit ovat synteesikaasun sukupolven järjestelmä, jossa on vain yksi uudistaja (toissijainen uudistaja), paine-swing adsorption (PSA) – järjestelmä H2 hyödyntämistä ja ilmastointi erottaminen kasvi lähteenä N2., Parannuksia converter suunnittelu, kuten radial-ja vaaka-katalysaattori vuodetta, sisäiset lämmönsiirtimet, ja synteesikaasun hoitoa, auttoi lisätä ammoniakin pitoisuudet poistuminen synteesi converter noin 12% 19-21%. Suurempi muunnos syöttöä kohti sekä tehokkaammat turbiinit ja kompressorit vähensivät energiankulutusta entisestään. Energiatehokkuutta ovat parantaneet tehokkaammat CO2-poistoliuokset, kuten kaliumkarbonaatti ja metyylidietanoliamiini (MDEA). Useimmat nykyaikaiset laitokset voivat tuottaa ammoniakkia, jonka energiankulutus on 28 GJ / m. t.,
lisäksi suunnittelu, mekaaninen ja metallurginen parannuksia tehty tänä aikana, käyttöpaine synteesi silmukka oli merkittävästi vähentynyt. Kun ensimmäinen yksijunatehdas rakennettiin 1960-luvulla, siinä oli korkeapainesilmukka. Vuonna 1962, MWK sai tiedustelun Imperial Chemical Industries (ICI) varten ehdotuksen rakentaa 544-m.t./päivän kasvi niiden Severnside sivuston. MWK ehdotti 152 baarin synteesisilmukkaa 324 baarin silmukan sijaan.,
Koska kehitys liike-tiedot ammoniakki reagoi 152 bar veisi enemmän aikaa kuin MWK oli vastattava ICI-tutkimus, he ottivat yhteyttä Haldor Topsøe tukea heidän suunnitelmia. Topsøellä oli tiedot, jotka kattoivat koko MWK: lle kiinnostavan painealueen. Lisäksi heillä oli tietokone ohjelma laskemiseksi määrä katalysaattori, joka oli vaaditaan pienempi käyttöpaine. Vaikka ICI valitsi bechtelin suunnittelemaan tehtaan, MWK pystyi kehittämään flowsheet 544 m.t: lle.,/vrk suunnittelu keskipako kompressorit ja matalan paineen synteesi silmukka, jota jotkut ihmiset pitävät kaikkein tärkein yksittäinen tapahtuma kehitystä yhden junan ammoniakkia kasvi.
Noin kaksi kertaa niin paljon katalysaattori vaaditaan 152 bar 324 bar, kasvua, joka tuntui taloudellisesti mahdollista. Vaikka muunnin tarvitsisi kaksinkertainen tilavuus, pienempi käyttöpaine vähentäisi vaadittua painekuoren paksuutta. Tämän seurauksena muuntimen ja katalysaattorin tarvitseman metallin paino pysyi suunnilleen samana., Matalapainesynteesisilmukka mahdollisti myös keskipakokompressorien käytön vastavuoroisten kompressorien sijaan. Toinen parannus oli lämmön talteenotto korkean paineen höyryn tuottamiseksi höyryturbiinikäyttöisille.
Kasvi malleja 21st century
ensimmäisten vuosien Aikana 21st century, monet parannuksia tehtiin ammoniakkia kasvi teknologiaa, jonka avulla olemassa olevat laitokset lisätä tuotantoa hinnat ja uusia laitoksia rakennetaan suurempia ja suurempia valmiuksia. Teknologiatoimittajien välinen kilpailu on melko kovaa., Kolme teknologian lisensoijat — KBR (Kellogg Brown and Root), Haldor Topsøe, ja ThyssenKrupp Industrial Solutions (TKIS) — tällä hetkellä hallitsevat markkinoita. Ammoniakki Casale, joka tarjoaa aksiaalis-radial katalyytti bed suunnittelu, on markkinajohtaja revamps nykyisten laitosten.
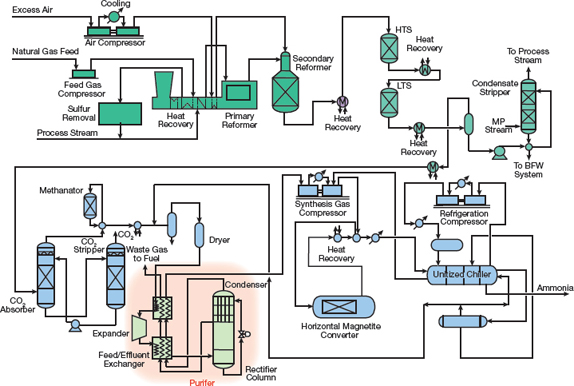
▲Kuva 4. Moderni ammoniakkia kasveja suunnitellut KBR käyttää sen omaa Puhdistamot suunnittelu.,
Useimmat ammoniakin kasveja äskettäin suunnitellut KBR hyödyntää sen Puhdistamot prosessi (Kuva 4), joka yhdistää matalan vakavuus uudistamisessa ensisijainen uudistaja, nestemäinen N2 pestä puhdistamot alavirtaan methanator poistaa epäpuhtauksia ja säätää H2:N2-suhde, oma jäte-lämpöä kattilan suunnittelu, purkamaton chiller, ja vaaka-ammoniakki synteesi converter.
kokoonpanosta Riippuen kasvi, energian kulutus voi olla niinkin alhainen kuin 28 GJ/m.t. Koska toissijainen uudistaja käyttää liikaa ilmaa, ensisijainen uudistaja voi olla pienempi kuin perinteiset mallit., Kryogeeninen puhdistamot (Kuvassa 4 valo vihreä valo oranssi tausta), joka koostuu expander, lauhdutin, rehu/jätevesien lämmönvaihdin, ja tasasuuntaaja sarake, poistaa epäpuhtauksia, kuten CO -, CH4 -, ja argon, synteesikaasun kun säädät H2:N2 suhde meikki kaasu ammoniakki-silmukka optimaalisella tasolla. Ammoniakin pitoisuus poistuminen alhainen paine pudota vaaka converter on 20-21%, mikä vähentää energian vaatimukset kompressori kierrättää., KBR tarjoaa myös matalapaineisen ammoniakkisilmukan, joka käyttää magnetiittikatalyytin ja sen Oman ruteniumkatalyytin yhdistelmää.
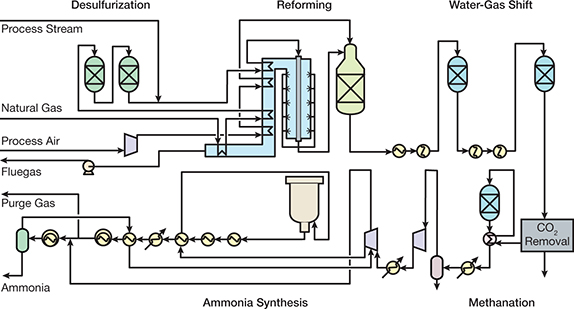
▲Kuva 5. Haldor Topsøe tarjoaa ammoniakkia laitoksen suunnittelu, joka on oma puoli-potkut uudistaja, joka säteilevä polttimet tarjonta lämpöä uudistaminen reaktio.
synteesikaasun sukupolven osa (tai front end) ja Haldor Topsøe suunniteltu kasvi (Kuva 5) on melko perinteinen, lukuun ottamatta sen omaa puolella-potkut uudistaja, joka käyttää säteilevä polttimet toimittaa lämpöä uudistaminen reaktio., Haldor Topsøe tarjoaa myös oma rauta-pohjainen synthesis catalyst, radial-virtaus muuntimet, joka koostuu yksi, kaksi tai kolme vuodetta, ja oma bajonetti-putki jätteen-lämpöä kattilan. Uudempia kehityskulkuja ovat muun muassa S-300 ja S-350 converter-mallit. S-300 converter on kolmen hengen radial-flow configuration sisäiset lämmönsiirtimet, kun taas S-350 muotoilu yhdistyvät S-300 converter S-50 yhden hengen suunnittelu jäte-lämmön talteenotto välillä muuntimet maksimoida ammoniakkia muuntaminen.
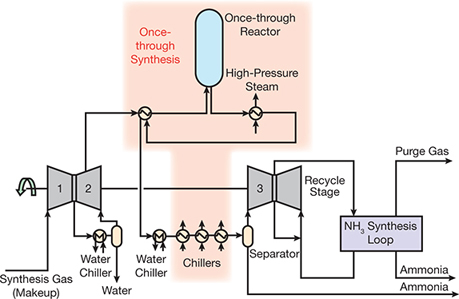
▲Kuva 6., ThyssenKruppin kaksoispainesynteesisilmukkasuunnittelussa on kertareaktori syngas-kompressorien välissä.
ThyssenKrupp tarjoaa perinteisen kasvi (Kuva 6), jossa on ainutlaatuinen toisen asteen uudistaja suunnittelu, oma jäte-lämpöä kattilan, radial-virtaus muuntimet, ja dual-paine ammoniakin synteesi silmukka. Nykyään tkis-kaksipaineprosessin avulla voidaan saavuttaa 3 300 m.t./vrk: n tuotantonopeus.
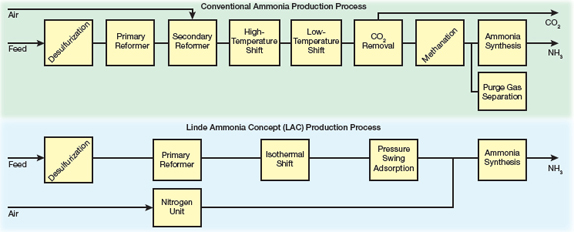
▲Kuva 7., Linde Ammoniakkia Käsite (LAC) tarjoaa paine swing adsorption unit erittäin puhtaan vedyn tuotanto ja air separation unit erittäin puhtaan typen tuotantoon.
Linde Ammoniakkia Käsite (LAC) on vakiintunutta tekniikkaa prosessi järjestelmä, jolla on yli 25 vuoden käyttökokemukset laitoksissa, joiden kapasiteetti 200 m.t./päivä yli 1,750 m.t./päivä., LAC-prosessin kaavio (Kuva 7) korvaa kalliita ja monimutkaisia etupää perinteisen ammoniakkia kasvi, jossa on kaksi hyvin todistettu, luotettava prosessi yksiköitä:
- tuotannon ultra-high-purity vetyä höyry-metaani uudistaja kanssa PSA puhdistus
- tuotannon ultra-high-puhtaus typen, jonka kryogeenisten typen generation-yksikkö, joka tunnetaan myös nimellä air separation unit (ASU).
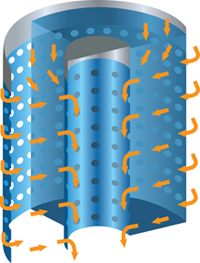
▲Kuva 8., Ammoniakki Casale on prosessi työllistää katalysaattori sänky, että valjaat axial-radial-teknologia, joka on pienempi painehäviö ja korkeampi hyötysuhde kuin tavallinen katalysaattori vuodepaikkaa.
ammoniakin Casalen tehtaan suunnittelun valmistusnopeus on 2 000 m.t. / vrk. Yksi tämän mallin keskeisistä ominaisuuksista on aksiaalis-radial-tekniikka katalyyttisängyssä (Kuva 8). Vuonna aksiaalinen-radial katalysaattori sänky, useimmat synteesikaasun kulkee katalysaattori sängyn radial suuntaan, luo erittäin alhainen painehäviö., Loput kaasusta kulkee alas läpi pintakerros catalyst akselin suunnassa, poistaa tarpeen top kansi katalysaattori sänky. Casale on aksiaali-radial katalysaattori bed teknologiaa käytetään sekä korkean lämpötilan ja matalan lämpötilan muutos muuntimet, sekä synteesi-muunnin.
Muita tekniikoita
Jotkut teknologian toimittajat ovat tarjonneet kaasu-lämmitetty uudistajat (GHRs) ammoniakin tuotannossa vuonna pieni-kapasiteetti kasvit tai kapasiteetti kasvaa., Toisin kuin perinteisesti suunniteltu kasveja, jotka käyttävät ensisijainen uudistaja ja toissijainen uudistaja toiminta-sarjaan, kasvit GHRs käyttää kuumaa prosessi kaasua toissijainen uudistaja toimittaa lämpöä ensisijainen uudistaja. Tämä vähentää koko ensisijainen uudistaja ja poistaa CO2-päästöt ensisijainen uudistaja pino, mikä tekee prosessista entistä ympäristöystävällisempiä.,
vaikka jotkut ammoniakkia tuottajien puolestapuhuja hajautettu tuotanto ammoniakin pieni ammoniakin kasveja, useimmat yritykset haluavat rakentaa suuria laitoksia lähellä halpoja raaka-ainelähteitä ja liikenteen tuotteen laiva -, rautatie -, tai putki kuluttajille.
Ammoniakkia hiilestä
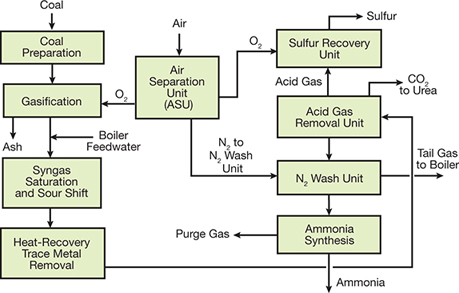
▲Kuva 9. Kiina tuottaa suurimman osan ammoniakistaan kivihiilestä.
Kiina tuottaa ammoniakkia enemmän kuin mikään muu maa ja tuottaa suurimman osan ammoniakistaan kivihiilestä (Kuva 9).,
perus käsittely-yksiköiden hiili-perustuu ammoniakin kasvi ovat ASU erottamiseen O2 ja N2 air, kaasuttimen, hapan kaasu vaihto (SGS) yksikkö, happo kaasun poisto yksikkö (AGRU), ja ammoniakki synteesi yksikkö. Happea ASU syötetään kaasuttimen muuntaa kivihiili osaksi synteesikaasu (H2, CO, CO2) ja CH4. On monia kaasutin malleja, mutta useimmat nykyaikaiset gasifiers perustuvat leijutettu vuodetta, jotka toimivat yli ilmakehän paineen ja kyky hyödyntää eri hiili-syötteitä. Mallista riippuen CO – tasoja voidaan tuottaa 30-60 tilavuusprosenttia.,
kaasutuksen jälkeen kaikki synteesikaasun hiukkaset poistetaan ja SGS-yksikköön lisätään höyryä. SGS-prosessissa käytetään tyypillisesti koboltti-ja molybdeenikatalyyttiä (como), joka on erityisesti suunniteltu toimimaan rikkiympäristössä.
Kun vähentää CO-pitoisuus synteesikaasu alle 1 til -%, n synteesikaasuksi on fed on AGRU, jossa jäähdytetty metanoli pesee ratkaisu (esim Rectisol) poistaa CO2 ja rikki synteesikaasua. CO2-yläpuoli joko tuuletetaan tai syötetään ureatehtaalle. Rikin poistovirtaa syötetään rikin talteenottoyksikköön (SRU).,
Synteesikaasuksi, joka kulkee AGRU on yleensä puhdistetaan kahdella eri tavalla:
- typpi pese yksikkö poistaa jäljellä CO-ja CH4: n päässä synteesikaasuksi, ennen kuin se syötetään synteesi silmukka
- PSA-järjestelmä, CO-ja CH4-poisto.
Sulkeminen ajatuksia
viime 60 vuotta, ammoniakkia prosessi, teknologia on parantunut rajusti. Kasvi ulkoasuja kehittynyt multi-train malleja, usein eri määrä junien etupää ja synteesi silmukan, yhden juna-malleja., Synteesikaasun valmistus tehtaan etupäässä kasvoi ilmanpaineesta 30-50 barg: n paineeseen. Kapasiteetti kasvoi 100 metristä päivässä jopa 3 300 metriin päivässä yhdessä junassa.
energiatehokkuutta on parannettu sekä — alkaen kulutukset sekä yli 60 GJ/m.t. ammoniakin koksi-pohjainen kasveja 40-50 GJ/m.t. ensimmäinen luonnon -, kaasu-pohjainen kasveja 30-40 GJ/m.t. ensimmäinen single-juna kasveja. Moderni kasvit on lisätty lämmön talteenotto höyry tuotannon paineet peräti 125 barg sekä synteesikaasun valmistelu-osiossa ja synteesi silmukka.,
prosessilaitteiden osalta on siirrytty mäntäkompressoreista keskipakokompressoreihin. Sisäinen lämmönvaihdin on toteutettu synteesi converter lisätä muuntaminen H2 ja N2 NH3 to. Suunnittelijat ovat hyödyntäneet vedyn talteenottoa puhdistuskaasusta (yksiköinä, kuten PSA-järjestelmissä) tuotannon lisäämiseksi tai laitoksen energiankulutuksen vähentämiseksi. Suunnittelijat ovat myös toteuttaneet hot feed kaasu desulfurization järjestelmiä. Reformoinnissa, siirtymävaiheen muuntamisessa, metanoinnissa ja ammoniakin synteesissä käytetyt katalyytit ovat parantuneet merkittävästi.,
parantaa prosessin valvonta ja turvallisuus, distributed control systems (DCSs) advanced process control, sekä turvallisuus-varustettava mittalaitteilla järjestelmät (SISs), ovat nyt vakiona ammoniakki kasveja. Ennen kuin jokin prosessi menee verkkoon, tehdään hazard and operability (HAZOP) – tutkimukset ja suojausanalyysien kerros (LOPAs). Simulaattoreiden ja koulutuskäytäntöjen edistysaskeleet varmistavat, että operaattorit ja insinöörit voivat suorittaa tehtävänsä turvallisesti ja tehokkaasti.,
Nämä ovat vain muutamia tuhansia parannuksia in teknologia ja turvallisuus, jotka on toteutettu, jotta ammoniakki teollisuuden yksi kaikkein tuottavimpia ja turvallinen aloista maailmassa.
Kiitokset
kirjoittajat tunnustavat apua KBR, ThyssenKrupp Industrial Solutions, Haldor Topsøe, Linde, ja Casale teknisen kirjallisuuden omilla prosessi teknologioita.