amoniak je rozhodující při výrobě hnojiv a je jednou z největších objemových syntetických chemikálií vyráběných na světě. Tento článek zkoumá vývoj výroby amoniaku a popisuje současné výrobní technologie.
většina lidí spojuje štiplavý zápach amoniaku (NH3) s čisticími prostředky nebo vonícími solemi. Použití amoniaku v těchto dvou produktech však představuje jen malou část celkové celosvětové produkce amoniaku, která v roce 2014 činila přibližně 176 milionů metrických tun (1)., Abychom ocenili, kde je dnes průmysl a technologie, nejprve se podívejme, jak jsme se sem dostali.
amoniak je znám již více než 200 let. Joseph Priestley, anglický chemik, poprvé izoloval plynný amoniak v roce 1774. Jeho složení zjistil francouzský chemik Claude Louis Berthollet v roce 1785., V roce 1898 Adolph Frank a Nikodem Caro zjistil, že N2 by mohla být stanovena pomocí karbidu vápníku tvořit dusíkaté vápno, které by pak mohly být hydrolyzován vodou za vzniku amoniaku (2):
CaO + 3C ↔ CaC2 + CO
CaC2 + N2 ↔ CaCN2 + C
CaCN2 + 3H2O ↔ CaCO3 + 2NH3
výroba značného množství amoniaku pomocí kyanamid procesu došlo až na počátku 20.století. Protože tento proces vyžadoval velké množství energie, vědci zaměřili své úsilí na snížení energetických požadavků.,
německý chemik Fritz Haber provedl některé z nejdůležitějších prací ve vývoji moderního průmyslu amoniaku. Práce se studentem na Univ. z Karlsruhe syntetizoval amoniak v laboratoři z N2 a H2.
mezitím, Walther Nernst, profesor fyzikální chemie na Univ. z Berlína vyvinul proces výroby amoniaku průchodem směsi N2 A H2 přes Železný katalyzátor při 1000°C a tlaku 75 bargů. Byl schopen produkovat větší množství amoniaku při tomto tlaku než dřívější experimenty Habera a dalších při atmosférickém tlaku., Nernst však dospěl k závěru, že tento proces není proveditelný, protože bylo obtížné nebo téměř nemožné (v té době) vyrábět velké zařízení schopné pracovat při tomto tlaku.
nicméně Haber i Nernst usilovali o vysokotlakou cestu k výrobě amoniaku přes katalyzátor. Haber konečně vyvinuli proces pro výrobu užitkových množství amoniaku, a v roce 1906 byl schopen dosáhnout 6% koncentrace amoniaku v reaktoru naloženo s osmium jako katalyzátor., To je obecně uznáváno jako bod obratu ve vývoji praktického procesu výroby amoniaku v komerčních množstvích.
Haber si uvědomil, že množství amoniaku vytvořeného v jediném průchodu převodníkem bylo příliš nízké na to, aby bylo komerčního zájmu. Produkovat více amoniaku z make-up plyn, navrhl recyklovat systému, a získal patent na koncept. Haberova recyklační myšlenka změnila vnímání procesního inženýrství jako statického ve prospěch dynamičtějšího přístupu., Kromě chemické reakční rovnováhy Haber uznal, že rychlost reakce je určujícím faktorem. Místo jednoduchého výnosu v jednorázovém procesu se soustředil na časoprostorový výnos v systému s recyklací.
BASF zakoupil Haberovy patenty a zahájil vývoj komerčního procesu. Po testování více než 2500 různých katalyzátorů, Carl Bosch, Alvin Mittasch, a další BASF chemici vyvinuli povýšen železa katalyzátor na výrobu čpavku v roce 1910., Vývoj zařízení, které by odolalo potřebným vysokým teplotám a tlaku, byl ještě obtížnějším úkolem. Časný reaktor z měkké oceli trval jen 80 hodin před selháním v důsledku dekarbonizace. Obložení reaktorů z měkké oceli měkkým železem (které nebylo náchylné k dekarbonizaci) a přidání drážek mezi oběma vložkami k uvolnění vodíku, který se rozptýlil přes měkkou železnou vložku, tento problém vyřešil., Další významné výzvy, součástí návrhu výměníku tepla, aby přívod plynu do reakční teploty a chlazení výstupních plynů, a navrhnout způsob, jak přivést katalyzátoru, reakční teplota.
první komerční zařízení na výrobu amoniaku založené na procesu Haber-Bosch postavil BASF v Oppau v Německu. Závod se rozjel v Září. 9, 1913, s výrobní kapacitou 30 m. t. / den.
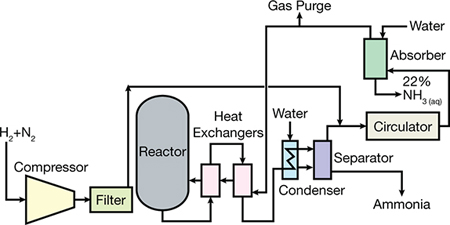
Figure Obrázek 1. Jedná se o zjednodušený průtokový list prvního komerčního závodu na amoniak BASF.,
Obrázek 1 je průtokový list prvního komerčního zařízení na výrobu amoniaku. Reaktor obsahoval vnitřní výměník tepla kromě těch, které jsou uvedeny na schématu.
global production rates
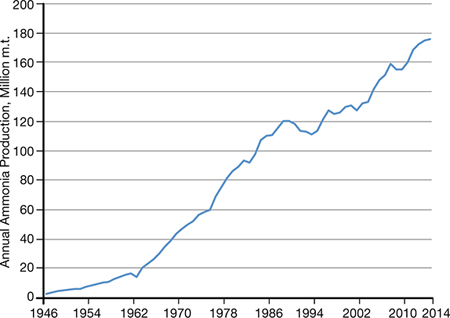
▲figura 2. Celosvětová produkce amoniaku se od roku 1946 do roku 2014 neustále zvyšuje.
výroba amoniaku se stala jedním z nejdůležitějších průmyslových odvětví na světě. Bez výnosu plodin možné pomocí amoniaku na bázi hnojiv a chemikálií, globální populace by být alespoň dvě až tři miliardy méně, než je tomu dnes (3)., Amoniak výroba neustále rostla od roku 1946 (Obrázek 2), a odhaduje se, že roční produkce amoniaku je v hodnotě více než 100 miliard dolarů, s některé rostliny produkují více než 3000 m. t./den NH3.
V roce 1983, u příležitosti 75. výročí AIChE založení, blue ribbon panel významných chemických inženýrů pojmenoval to, co oni věřili být na světě deset největších chemické inženýrství úspěchy (4)., Zahrnuje takové výkony jako zázračné léky, syntetických vláken, a atomové energie, citace také průlom, která umožnila produkci velkého množství amoniaku v kompaktní, single-unit rostlin.
v posledních desetiletích se chemickým inženýrům podařilo vytvořit procesy, které vytvářejí obrovské množství amoniaku za relativně nízké náklady. Jak nedávno jak před 80 lety, celková roční produkce syntetizovaný amoniak byl jen přes 300.000 m.t. Díky chemické inženýrství objevy, jeden moderní amoniaku rostlina může produkovat více než 750.000 m.t./yr.,
Přibližně 88% amoniaku ročně se spotřebuje při výrobě hnojiv. Většina zbytku jde do výroby formaldehydu. Čína vyrobila v roce 2014 asi 32,6% světové produkce, zatímco Rusko, Indie a USA vyrobily 8,1%, 7,6% a 6,4% (1). Zatímco většina světové produkce amoniaku je založen na parní reformování zemního plynu, významné množství je produkován zplyňování uhlí; většina zařízení na zplyňování se nachází v Číně.,
moderní výrobní procesy
obrovský nárůst poptávky po amoniaku z let 1950 až 1980 vyžadoval větší, energeticky účinnější rostliny. Tato desetiletí také zaznamenala změnu ve filozofii designu. Do té doby byla rostlina amoniaku považována za sestavu nesouvisejících jednotek, jako je příprava plynu, čištění plynu, komprese plynu a syntéza amoniaku. Nové inovace a integrální design svázané procesní jednotky dohromady nejúčinnějšími a nejúčinnějšími způsoby.
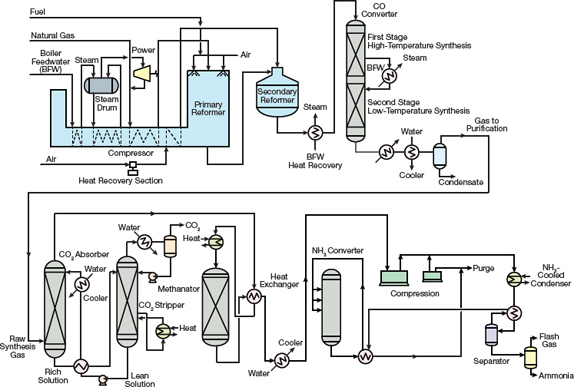
Figure obrázek 3., KBR navrhla jednu z prvních jednokolejných velkokapacitních čpavkových elektráren.
v polovině 1960, American Oil Co. nainstalován jeden-converter amoniaku rostlina inženýrství M. W. Kellogg (MWK) v Texas City, TX, s kapacitou 544 m.t./den. Koncept designu jednoho vlaku (obrázek 3) byl tak revoluční, že v roce 1967 obdržel Cenu Kirkpatrick Chemical Engineering Achievement Award.,
rostliny, které Se používají čtyři-případ radiální kompresor pro kompresi syngas tlaku 152 bar, a konečné kompresi na provozní tlak 324 baru došlo v pístových kompresorů. Byly také implementovány odstředivé kompresory pro syntézní smyčku a chladicí služby, které poskytovaly významné úspory nákladů.,
hlavní rozdíly mezi MWK proces a postupy používané v předchozích čpavek rostliny v ceně:
- pomocí odstředivého kompresoru jako součást syntézní plyn komprese
- maximalizace využití odpadního tepla z procesu
- generování páry z odpadního tepla pro použití v parní turbíny ovladače
- pomocí chladicí kompresor pro náměty a atmosférické chlazení.
integrovaný systém, který vyvážil spotřebu energie, výrobu energie, velikost zařízení a objem katalyzátoru, byl začleněn do celého závodu.,
Většina rostlin postavena v letech 1963 a 1993 měl velké single-vlak konstrukce s výrobu syntetického plynu na 25-35 bar a syntézy amoniaku na 150-200 bar. Další variace od Brauna (nyní KBR) nabídla mírné úpravy základního designu. Braun Čistička proces rostliny využity primární nebo tubulární reformátor s nízkou výstupní teplotu a vysokou úniku metanu snížit velikost a náklady na reformátora. Přebytečný vzduch byl přidán sekundární reforming snížit obsah metanu v primární reformátor výstupní proud na 1-2%., Přebytečný dusík a další nečistoty byly odstraněny za metanátorem. Protože syntézní plyn byl v podstatě bez nečistot, byly k dosažení vysoké konverze amoniaku použity dva měniče amoniaku s axiálním průtokem.
Některé nedávno postavené rostliny mají syntézní plyn generace systému pouze s jedním reformátor (žádné sekundární reforming), tlak swing adsorpce (PSA), systém pro H2 zotavení, a letecké oddělení rostlin jako zdroj N2., Zlepšení converter design, jako jsou radiální a horizontální katalyzátor, postele, vnitřní výměníky tepla a syntézního plynu léčby, přispívá ke zvýšení koncentrace amoniaku ukončení syntézy převodník z 12% na 19-21%. Vyšší konverze na průchod spolu s účinnějšími turbínami a kompresory dále snížily spotřebu energie. Účinnější řešení odstraňování CO2, jako je uhličitan draselný a methyldiethanolamin (MDEA), přispěly ke zlepšení energetické účinnosti. Většina moderních rostlin může vyrábět amoniak se spotřebou energie 28 GJ / m. t.,
kromě konstrukčních, mechanických a metalurgických vylepšení provedených během této doby byl výrazně snížen provozní tlak syntézní smyčky. Když byla v 60.letech postavena první jednolodní elektrárna, obsahovala vysokotlakou syntézní smyčku. V roce 1962, MWK obdržel dotaz od Imperial Chemical Industries (ICI) pro návrh na vybudování 544-m.t./den závodu v jejich Severnside stránky. MWK navrhla 152-barovou syntetickou smyčku namísto 324-barové smyčky.,
Protože vývoj kinetická data pro reakce amoniaku na 152 bar bude trvat více času, než MWK musel reagovat na ICI dotaz, kontaktovali Haldor Topsøe na podporu svých plánů. Topsøe měl údaje pokrývající celý rozsah tlaku zájmu MWK. Kromě toho měli počítačový program pro výpočet množství katalyzátoru, který byl vyžadován při nižším provozním tlaku. I když ICI vybral Bechtel navrhnout závod, MWK byl schopen vyvinout flowsheet pro 544-m. t.,/ denní konstrukce s odstředivými kompresory a nízkotlakou syntézní smyčkou, kterou někteří lidé považují za jednu nejdůležitější událost ve vývoji jednokolejné továrny na amoniak.
přibližně dvakrát tolik katalyzátoru bylo zapotřebí na 152 bar jako na 324 bar, což bylo zvýšení, které se zdálo ekonomicky proveditelné. Přestože by převodník potřeboval dvojnásobek objemu, nižší provozní tlak by snížil požadovanou tloušťku tlakového pláště. V důsledku toho zůstala hmotnost kovu potřebná pro převodník plus katalyzátor přibližně stejná., Smyčka syntézy s nižším tlakem také umožnila použití odstředivých kompresorů namísto vratných kompresorů. Dalším zlepšením bylo obnovení tepla pro výrobu vysokotlaké páry pro pohony parních turbín.
Rostlinné vzory v 21. století
Během několika prvních let 21. století, mnoho vylepšení byly provedeny v amoniaku zařízení technologie, které umožňují stávající zařízení na zvýšení výrobní ceny a nových rostlin, které mají být postaveny s větší a větší kapacitou. Konkurence mezi dodavateli technologií je poměrně tvrdá., Na trhu v současné době dominují tři poskytovatelé technologických licencí — KBR (Kellogg Brown a Root), Haldor Topsøe a ThyssenKrupp Industrial Solutions (TKIS). Amoniak Casale, který nabízí design axiálně radiálního katalyzátoru, je lídrem na trhu v oblasti přepracování stávajících zařízení.
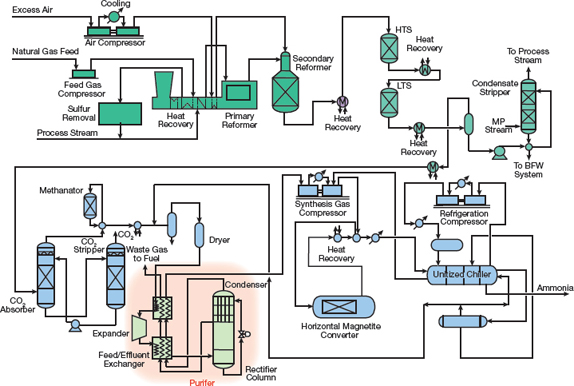
Figure obrázek 4. Moderní čpavkové rostliny navržené KBR využívají svůj vlastní design čističky.,
Většina amoniaku rostliny nedávno navržený KBR využít jeho Čistička proces (Obrázek 4), který spojuje low-závažnost reformy na primárním reformátor, tekutý N2 umýt čistička za methanator k odstranění nečistot a upravit H2:N2 poměr, speciální kotle na odpadní teplo design, unitized chladič, a horizontální syntézy amoniaku converter.
v Závislosti na konfiguraci zařízení, spotřeba energie může být tak nízké, jak 28 GJ/m.t. Protože sekundární reformátor používá přebytečný vzduch, primární reformátor může být menší než u konvenčních konstrukcí., Kryogenní čistička (znázorněno na Obrázku 4 v světle zelené s světle oranžové pozadí), který se skládá z expandéru, kondenzátor, zdroj/odpadní vody výměníku, a usměrňovací sloupce, odstraňuje nečistoty jako CO, CH4, a argonu ze syntézního plynu při nastavení H2:N2 poměr make-up plyn v amoniaku smyčky na optimální úrovni. Koncentrace amoniaku vystupující z nízkotlakého horizontálního měniče je 20-21%, což snižuje energetické požadavky na recyklační kompresor., KBR také nabízí nízkotlakou čpavkovou smyčku, která využívá kombinaci magnetitového katalyzátoru a jeho vlastního katalyzátoru ruthenium.
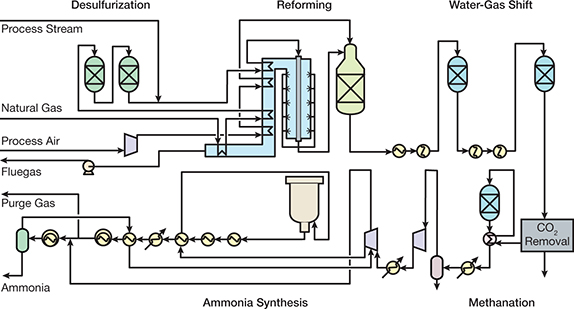
Figure obrázek 5. Haldor Topsøe nabízí konstrukci zařízení na výrobu amoniaku, která má vlastní boční reformátor, ve kterém sálavé hořáky dodávají teplo pro reformovací reakci.
syngas generace sekce (nebo před koncem) Haldor Topsøe-navržen tak, rostlina (Obrázek 5) je poměrně tradiční, s výjimkou jeho vlastní straně, vystřelil reformátor, který využívá sálavé hořáky na dodávku tepla pro reformování reakce., Haldor Topsøe také nabízí proprietární iron-based synthesis catalyst, radiální tok převodníky, skládající se z jedním, dvěma, nebo třemi lůžky, a proprietární bajonet-trubice kotle na odpadní teplo. Novější vývoj zahrnuje návrhy převodníků s-300 A S-350. S-300 converter je tři-postel radiální tok konfigurace s vnitřní výměníky tepla, zatímco S-350 design kombinuje S-300 převodník s S-50 single-postel design s odpady-využití tepla mezi převodníky, aby maximalizoval konverze amoniaku.
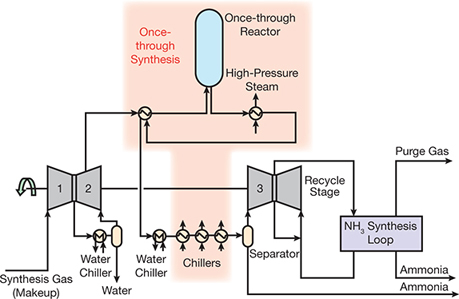
Figure obrázek 6., Konstrukce smyčky syntézy s dvojitým tlakem ThyssenKrupp je vybavena jednou průchozí reaktor mezi kompresory syngas.
ThyssenKrupp nabízí konvenční rostliny (Obrázek 6) s unikátní sekundární reforming design, speciální kotle na odpadní teplo, radiální tok převodníky, a dual-tlak amoniaku syntéza smyčky. Dnes lze dosáhnout výrobní rychlosti 3 300 m. T./den pomocí procesu dvojitého tlaku TKIS.
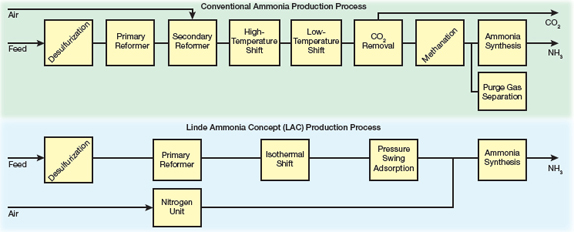
Figure Obrázek 7., Linde amoniak Concept (LAC) je vybaven adsorpční jednotkou s tlakovým výkyvem pro výrobu vodíku s vysokou čistotou a jednotkou pro separaci vzduchu pro výrobu dusíku s vysokou čistotou.
Linde Amoniaku Koncept (LAC) je založena technologie procesu schéma s více než 25 let provozních zkušeností v elektrárnách s kapacitou od 200 m.t./den na více než 1750 m.t./den., LAC proces schéma (Obrázek 7), se nahrazuje nákladné a složité front-end konvenční amoniaku rostlina s dvěma dobře osvědčené, spolehlivé procesní jednotky:
- výrobu ultra-vysoce čistý vodík z parní reforming metanu s PSA čištění
- výrobu ultra-high-čistota dusíku kryogenní dusíku generace jednotku, také známý jako vzduchová separační jednotka (ASU).
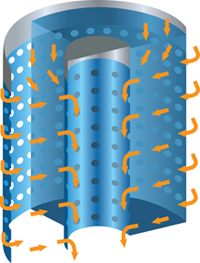
▲Obrázek 8., Amoniak Casale je proces využívá katalyzátor, který využívá axiální-radiální technologie, která má nižší pokles tlaku a vyšší účinnost než standardní katalyzátor postele.
konstrukce závodu společnosti amoniak Casale má výrobní rychlost 2 000 m. t. / den. Jednou z klíčových vlastností této konstrukce je axiálně radiální technologie v katalyzátorovém loži (Obrázek 8). V axiálně radiálním katalyzátoru většina syntézního plynu prochází ložem katalyzátoru v radiálním směru a vytváří velmi nízký pokles tlaku., Zbytek plynu prochází horní vrstvou katalyzátoru v axiálním směru, což eliminuje potřebu horního krytu na loži katalyzátoru. Casale je axiální radiální katalyzátor lože technologie se používá jak ve vysokoteplotních a nízkoteplotních převodníků, stejně jako v syntéze převodníku.
ostatní technologie
někteří dodavatelé technologií nabídli reformátory vytápěné plynem (GHRs) pro výrobu amoniaku v malých kapacitních závodech nebo pro zvýšení kapacity., Na rozdíl od konvenčně konstruované rostliny, které používají reformingu primární a sekundární reforming působících v sérii, rostliny s GHRs použití horkého plynu z procesu sekundární reforming na dodávku tepla pro primární reformátor. To snižuje velikost primárního reformeru a eliminuje emise CO2 z primární reformátor stack, což je proces šetrnější k životnímu prostředí.,
I když některé amoniaku výrobců advokáta pro distribuované výroby amoniaku v malé čpavek rostliny, většina firem dává přednost vybudovat velké zázemí v blízkosti levné zdroje surovin a dopravy produktu po železnici, lodí nebo potrubí pro spotřebitele.
amoniak z uhlí
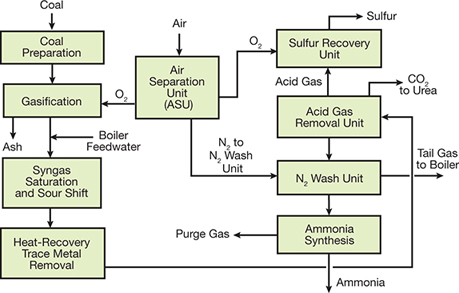
▲obrázek 9. Čína vyrábí většinu svého amoniaku z uhlí.
Čína produkuje více amoniaku než kterákoli jiná země a produkuje většinu svého amoniaku z uhlí (obrázek 9).,
základní procesorové jednotky, ve na bázi uhlí na výrobu čpavku, jsou ASU pro separaci O2 a N2 ze vzduchu, zplyňovače, zakysanou plynu shift (SGS) jednotka, kyselých plynů, jednotky (AGRU), a syntézu čpavku jednotky. Kyslík z ASU je přiváděn do Zplyňovače, aby přeměnil uhlí na syntézní plyn (H2, CO, CO2) a CH4. Existuje mnoho zplyňovače vzory, ale většina moderních zplynovače jsou založeny na fluidního lůžka, které pracují nad atmosférický tlak a mají schopnost využít různé uhlí živí. V závislosti na konstrukci mohou být vyrobeny úrovně CO 30-60% objemu.,
po zplyňování se odstraní všechny částice v syntézním plynu a do jednotky SGS se přidá pára. Proces SGS obvykle využívá katalyzátor kobaltu a molybdenu (CoMo) speciálně navržený pro provoz v prostředí síry.
po snížení koncentrace CO v syntézním plynu na méně než 1 vol% se syngas přivádí do AGRU,kde chlazený roztok pro čištění methanolu (např. CO2 nad hlavou je buď odvětráván nebo přiváděn do močoviny. Proud výstupu síry je přiváděn do jednotky pro obnovení síry (SRU).,
syntézní plyn, který prochází přes AGRU se obvykle čistí pomocí jednoho ze dvou metod:
- dusíku mycí jednotka k odstranění zbytkového CO a CH4 ze syntetického plynu, než je fed syntézu smyčky
- systém PSA, pro CO a CH4 odstranění.
závěrečné myšlenky
během posledních 60 let se technologie procesu amoniaku drasticky zlepšila. Rozložení rostlin se vyvíjelo od návrhů s více vlaky, často s různým počtem vlaků v přední části a syntézní smyčce, až po návrhy s jedním vlakem., Příprava syntézy plynu na předním konci rostliny se zvýšila z atmosférického tlaku na tlak 30-50 bargů. Kapacity zvýšil ze 100 m.t./den, aby tolik, kolik 3,300 m.t./den v jednom vlaku.
Energetická účinnost se zlepšila stejně — od spotřeby i nad 60 GJ/m.t. amoniaku v koksu bázi rostliny, 40-50 GJ/m.t. v první zemního plynu na bázi rostliny 30-40 GJ/m.t. v první single-vlak rostlin. Moderní rostliny přidaly rekuperaci tepla výrobou páry při tlacích až 125 barg jak v sekci Přípravy syngas, tak ve smyčce syntézy.,
pokud jde o procesní zařízení, došlo k posunu od vratných kompresorů k odstředivým kompresorům. V synthesis converter byl implementován vnitřní výměník tepla pro zvýšení konverze H2 A N2 Na NH3. Návrháři si poklepal na vodík zotavení z regeneračního plynu (v jednotkách jako PSA systémy) pro zvýšení výroby nebo snížení energetické spotřeby. Návrháři také implementovali systémy odsiřování plynu za tepla. Došlo k významným zlepšením katalyzátorů používaných při reformování, přeměně směn, metanaci a syntéze amoniaku.,
zlepšit řízení procesů a bezpečnosti, distribuované řídicí systémy (DCSs) pro pokročilé řízení procesů, stejně jako bezpečnost-vybaveno systémy (SISs), jsou nyní standardní v čpavek rostliny. Před spuštěním jakéhokoli procesu se provádějí studie nebezpečnosti a provozuschopnosti (HAZOP) a vrstvy analýz ochrany (LOPAs). Pokroky ve výcvikových simulátorech a vzdělávacích postupech zajišťují, že operátoři a inženýři mohou bezpečně a efektivně plnit své povinnosti.,
Tyto jsou jen některé z tisíců vylepšení v oblasti technologií a bezpečnosti, které byly implementovány, aby se amoniak průmysl jedním z nejvíce produktivní a bezpečný odvětví na světě.
Poděkování
autoři na vědomí, pomocí KBR, ThyssenKrupp Industrial Solutions, Haldor Topsøe, Linde, a Casale pro poskytování technické literatury v jejich příslušných technologií výroby.